Lego opens giant China facility; relies on solar energy to power it
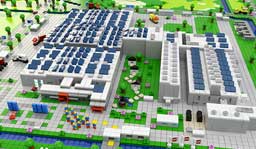
Danish toy maker Lego Group recently inaugurated its mammoth a 165,000 sq m-factory in Jiaxing, China, to cater to China and Asia. The investment amounts to a three-digit million Euro figure.
The group also owns and operates factories in Denmark, Hungary, Mexico and the Czech Republic.
The factory in Jiaxing currently employs more than 1,200 people, and is expected to produce between 70 and 80% of all Lego products sold in Asia.
Jørgen Vig Knudstorp, President/CEO said, “We have built a state-of-the-art factory in Jiaxing that adheres to the same global production standards as our factories across the world.”
The Jiaxing factory has a high focus on integrating sustainable solutions from recycling and reusing waste and water to minimising the energy consumption, the firm says. Thus, it will install solar panels, reducing CO2 emissions by more than 4,000 tonnes/year.
Almost 20,000 solar panels will be installed on the roof during the coming months and when it is fully operational in the summer of 2017. The panels will produce almost six gigawatts/year – equivalent to the electricity use of more than 6,000 Chinese households. The solar panels will provide approximately 7% of the factory’s total electricity consumption – or enough to run 76 moulding machines.
The investment in solar panels in China follows the group's investments in offshore wind farms off the coasts of Germany and the UK in recent years – investments that will support the ambition of balancing the Lego's total energy consumption with renewable energy by 2020.
“We want to reduce the impact we have on the planet when making Lego products. Our investments in renewable and clean wind energy as well as the solar panels at the factory in Jiaxing are important additions to the many other initiatives we are already taking globally to reduce our impact on the environment,” says Tim Brooks, Vice President, Environmental Sustainability at the Lego Group.
“The panels cover an area equivalent to more than five football fields – the maximum number possible given the roof layout and need for access,” says Tim Brooks.
The Jiaxing factory also has 100% LED lighting, twice the required level of insulation, solar thermal panels to generate hot water for washrooms, efficient moulding machines, use of rainwater for irrigation, and electric vehicles for on-site transportation.
As an example, over the course of the last three years the amount of energy used to manufacture a Lego brick has reduced by 16%, says the firm. The ambition for 2016 is a further 2.5% reduction.
The company set up its Sustainable Materials Centre in 2015. The centre aims to deliver on the group’s ambition of ensuring that all raw materials used for manufacturing LEGO products, including packaging, are sustainable by 2030.
Every Lego product starts its life in the headquarters in Billund, Denmark, where more than 250 designers representing 35 nationalities develop hundreds of new play experiences every year, according to the company.
It takes between one to four years for a new Lego product to complete the journey from design concept to stores around the world.
Early this year, the company said sales growth was particularly strong in both Europe and Asia with both regions achieving high double-digit growth, while sales development in the Americas region was flat year over year.
(PRA)Copyright (c) 2016 www.plasticsandrubberasia.com. All rights reserved.