Recycling: Ineos Styroluion/Recycling Technologies jv for PS; Huhtamaki integrates APK’s LDPE-recyclate into laminated tubes
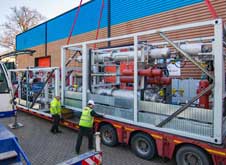
Styrenics maker Ineos Styrolution and UK recycler Recycling Technologies have tied up to further advance the development of recycling of polystyrene (PS) in Europe. The joint venture brings Ineos Styrolution’s knowledge in polymer science and production backed by its advanced technology and process with Recycling Technologies’s expertise in the area of building reactors, suitable to thermally recycle mixed plastics using pyrolysis.
Recycling Technologies has already completed a detailed research and trial process with Ineos. This activity included scientific research and processing of PS on Recycling Technologies’ Mark II test reactor, the RT7000, which turns hard-to-recycle plastic such as films, bags, laminated plastics into an oil, called Plaxx, used as a feedstock for new plastic production. The RT7000 is modular and small-scale, designed to fit easily onto existing waste treatment and recycling sites, providing a scalable solution to recycle waste plastic anywhere in the world.
Both companies will now further advance this depolymerisation solution based on Recycling Technologies’ fluidised bed technology, currently used for mixed plastics to adapt it for the commercial recycling of polystyrene.
Ineos Styrolution and Recycling Technologies believe recycled PS has the potential to meet the high specifications demanded for food packaging regulations making it attractive to the food industry.
Adrian Griffiths, CEO/Founder of Recycling Technologies adds: “To date we have focused on the recycling of mixed plastic waste, this initiative will allow us to develop and expand our feedstock recycling technology solutions to address a new and important market, recycling polystyrene.”
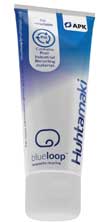
Meanwhile in other news, flexible packaging maker Huhtamaki Flexible Packaging Europe says it has been successful in integrating the first quantities of recycled plastics into one of its standard plastic barrier laminate for tubes. The polyethylene (PE) recyclate that facilitated this innovation is Mersalen, produced by APK AG, Merseburg (Germany).
APK’s solvent-based Newcycling technology generates Mersalen from complex polyethylene/polyamide multilayer film waste that is difficult for most conventional recycling processes to recycle. “The quality and purity of our LDPE recyclate shows properties close to virgin plastics and is suitable for a wide range of packaging applications,” says Florian Riedl, APK AG’s Director of Business Development.
The tube produced with Huhtamaki’s laminate contains 19% Mersalen recyclates and its performance is nearly identical with the standard referenced PBL structure produced with virgin LDPE. The ambitious R&D unit at Huhtamaki Flexible Packaging Europe plans to further increase the percentage of recycled content in their products and will test recyclates based on different feedstock streams.
With regard to the different input streams for plastics, recycling post-consumer waste streams stands at the centre of the circular economy discussion. Still, significant volumes of post-industrial waste need to be taken into account when implementing a truly circular plastics economy.
In addition, if the plastics and the packaging industry aspire to reaching the goals of the European Plastics Strategy by 2030, post-industrial waste must become circular.
“When it comes to our waste feedstock streams, APK is looking into all options. We are producing recyclates from post-industrial material, we research compounds of post-industrial and post-consumer streams and, of course, we ultimately aim to provide excellent quality from post-consumer mixed plastic waste,” says Riedl.
Currently, LDPE-recyclates based purely on post-consumer waste and suitable for food and cosmetic packaging, which requires food contact compliance, are not yet available on the European market. Huhtamaki and APK are cooperating closely to solve this challenge.
At its industrial-scale plant in Merseburg (Saxony-Anhalt, Germany) APK currently employs around 130 engineers, researchers, and administrative staff and features a recycling capacity of up to 20,000 tonnes/year. The two well-established plastic recyclate products produced in Merseburg are marketed as Mersalen and Mersamid.
(PRA)
Subscribe to Get the Latest Updates from PRA Please click here
©2020 Plastics and Rubber Asia. All rights reserved.

©2020 Plastics and Rubber Asia. All rights reserved.
Home Terms & Conditions Privacy Policy Webmail Site Map About Us