Green Materials: DS Smith/Aquapak work on biodegradable packaging; Lanxess launches biobased prepolymer line
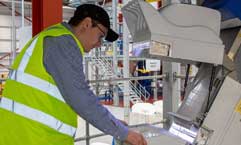
US-based packaging firm DS Smith and UK’s Aquapak, a developer of biodegradable polymer, are teaming up to develop the next generation of packaging solutions. By working together, the two organisations say they can provide sustainable fibre-based packaging solutions that will replace hard to recycle packaging made from combined materials such as cardboard and plastic.
After a period of pilot trials with the combined materials, focusing on both performance and recyclability, the partnership will now begin developing practical applications. This includes a range of fibre-based packaging where traditional plastic films can be replaced with Aquapak’s Hydropol, a biodegradable and water-soluble polymer that will help to improve the recycling process.
DS Smith’s exclusive partnership with Aquapak will support the company’s long-term sustainability targets, which include manufacturing 100% reusable or recyclable packaging by 2025. With a focus on tackling hard to recycle items, the adoption of this biodegradable technology will allow for less contamination in the recycling and paper-making process.
The partnership promises to transform the sustainable packaging market with potential scope across a variety of industries. Working closely with customers, this brings an opportunity to reduce single-use plastic pollution and support successful recycling for both consumers and recyclers.
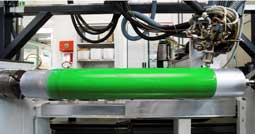
Meanwhile in other news, German specialty chemicals company Lanxess has developed a new range of MDI polyether prepolymers containing renewable, biobased raw materials. Marketed under the brand name Adiprene Green, the products are suitable as replacement for existing fossil-based polyether prepolymers to manufacture polyurethane (PU) elastomers.
The overall objective to develop Adiprene Green was to create a range of biobased prepolymers which allow the PU processor to produce components with a reduced CO2 footprint. Depending on the system, a reduction of CO2 between 20 to 30% is possible compared to fossil-based prepolymers due to the use of polyether polyols based on starch. The share of biobased raw materials varies between 30 to 90% dependent on the targeted system hardness. At the same time the existing PU processing capabilities would remain applicable and the properties of the final polyurethane elastomer would be similar to established elastomers based on fossil based polyether or even better.
Lanxess says the above is in line with its goal to be climate neutral until 2040.
Adiprene Green prepolymers are said to be easy to handle – they are processed in an identical manner to conventional prepolymers. No modifications to material handling, process temperatures or mixing ratios are necessary. In addition, the reactivity profile and demoulding times are similar to fossil based polyether prepolymers.
When reacted with 1,4 butanediol, a range of PU elastomers with a hardness from 40 Shore A to 60 Shore D can be achieved. As the PU system is versatile, Adiprene Green can be hand-mixed or machine mixed. Moreover, the prepolymers can be processed with Vibracat catalysts from Lanxess. Products of the Adiprene Green line are well suited for demanding applications such as roll covers, wheels, press sleeves or non-pneumatic tyres.
(PRA)
Subscribe to Get the Latest Updates from PRA Please click here
©2020 Plastics and Rubber Asia. All rights reserved.

©2020 Plastics and Rubber Asia. All rights reserved.
Home Terms & Conditions Privacy Policy Webmail Site Map About Us