Materials: recycled content HDPEs from Total; NEC’s cellulose-bioplastic with lacquerware colour
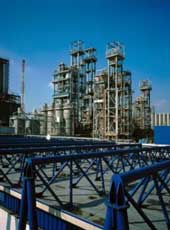
French petrochemicals firm Total has introduced a new range of HDPE products under the brand name Circular Compounds that contain high levels of recycled content. The materials, which are targeted at packaging applications, offer a performance equal to or exceeding that of virgin resins, thus actively contributing to the circular economy.
The new range consists of HDPE polymer products, in natural colour, cover all the manufacturing needs for blow-moulded bottles and heavy-duty containers for household and industrial liquids with a guarantee of 25% or 50% minimum of Post Consumer Recyclate (PCR). Total’s initial production capacity of HDPE Circular Compounds amounts to 20 kilotonnes, coming fully on stream during the course of 2017.
The composition and manufacturing process of these Circular Compounds is especially designed to minimise their environmental footprint. Their recycled content originates from post-consumer household waste collected in Western European countries and is recycled by selected partners chosen by Total for their outstanding product quality and recycling process capabilities. In its Antwerp plant in Belgium, Total says it applies a last deep decontamination step, which transforms the PCR into fragrance-free resin.
The PCR is compounded in Total’s plant with HDPE virgin products, specifically designed and produced as intermediate resins in order to overcompensate for any lack of performance and consistency of the PCR. Total says the resulting compounds are meant to be fully equivalent to any virgin resin sold in the same application, “but in reality they largely outperform them in all key aspects for their application”.
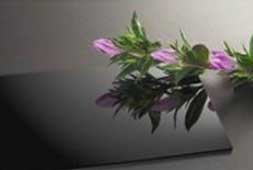
Meanwhile, Japanese firm NEC Corporation, in collaboration with the Kyoto Institute of Technology and a representative Japanese lacquerware artist, Dr. Yutaro Shimode, has developed a bioplastic using resin (cellulose resin) from grass, trees and other non-edible plant resources that features the highly regarded "Urushi black" colour of Japanese traditional lacquerware.
In order to create the new cellulose-based bioplastic, NEC developed a unique technology for mixing additives to adjust colouration and light reflectance of the material, enabling, for the first time, the realisation of optical properties (low brightness, high glossiness, etc.) similar to the deep and shiny "Urushi black" colour of high-grade Japanese lacquerware. The new plastic balances a high level of environmental friendliness and decorativeness and makes it possible to mass produce products of various shapes and patterns using the usual moulding process for ordinary plastics.
"In response to the depletion of resources and food shortage problems, the need for non-edible-plant-based plastics is increasing. In addition to NEC's history in the development of a unique cellulose-based plastic (NeCycle) using non-edible plant materials for use in durable electronic products, we have now developed a new bioplastic that, in addition to high functionality, realises the decorativeness of Japanese lacquerware, which is highly evaluated throughout the world, and illustrates a beauty well beyond what petroleum-based plastics can provide," said Dr. Masatoshi Iji, Research Fellow, IoT Devices Research Laboratories NEC Corporation.
This development was carried out in collaboration with the Kyoto Institute of Technology's Future-Applied Conventional Technology Centre, which is known for its achievements in future-applied conventional technology research (scientific analysis of traditional crafts and their applications in advanced material science), and Dr. Yutaro Shimode, a prominent Japanese lacquerware artist.
The development process involved, first, the fabrication by Dr. Shimode of a Japanese lacquerware "Urushi craft" model (transparent resin plate repeatedly coated with Japanese lacquer and polished by hand) that served as the standard for the advanced optical properties exhibited by high-quality Japanese lacquerware. Scientific analysis was performed on Japanese lacquerware at the Kyoto Institute of Technology. Based on the results, NEC then developed an optimised technology for modifying and mixing of the additives.
Going forward, NEC will pursue business partnerships aimed at commercialising the new bioplastic in durable products and high-grade materials that require a high level of decorativeness, such as the interior components of luxury cars.
Key features of the "Urushi black" bioplastics is the use of non-edible plant materials that are readily available as the main ingredient, such as cellulose resin produced from cellulose that is widely available from non-edible plant resources, such as grasses, the stalks of cereal crops and wood, and has the potential to be used as a substitute for petroleum. Plus, it realises the advanced optical properties (Urushi black) of high-grade Japanese lacquerware. The new bioplastic can be also mass-produced into products of various shapes using the moulding process for ordinary plastics
Conventionally, lacquerware is produced by coating the surface of substrates with lacquer and polishing them. For this newly developed bioplastic, the materials can be heated, melted, and injected into moulds (mirror-finishing) to form shapes (injection moulding), as with ordinary plastics. This makes it possible to mass-produce the bioplastic into products of various shapes and patterns.
(PRA)Copyright (c) 2016 www.plasticsandrubberasia.com. All rights reserved.