Materials News: Composites: going bone-deep into medical applications - Sept.digital issue
Also, download this story from the electronic issue here
Polymer composites, reinforced plastics and advanced composites have been used in the manufacture of medical prostheses and implants over the last decade. Advanced composites, containing approximately 60% of resistant continuous fibres made of carbon, glass or aramid materials, are increasingly being used in medical equipment such as surgical instruments, orthopaedic products and biocompatible implants, in this report on the medical applications market.
Medical composites market a boon
Bone fractures are not just about contending with the pain from an injury. More often than not, and especially if not treated immediately, this medical condition will lead to far more serious complications that could debilitate a patient. In serious cases, orthopaedic devices may be required.
The growing ger iat r ic populat ion and number of sports injuries are major drivers for the global orthopaedic implants market that will be worth US$6.2 billion by 2024, according to Grand View Research. The increasing number of road accidents and sports injuries, as well as an ageing population (people above the age of 65 years), are factors in the rising number of orthopaedic conditions.
The need for high quality devices at more affordable costs underpins the demand growth for implants, prostheses, splints, and other similar apparatus. Thus, could composites fit into this mould?
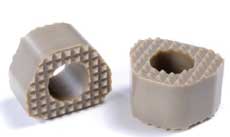
Expected to post a CAGR of 6.91% between 2016 and 2020, the global medical composite materials market is pacing towards increased demand from medical applications, according to a new report, Global Medical Composite Materials Market 2016-2020, by Research and Markets.
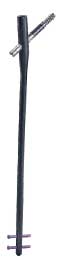
The report says that carbon fibre and fibre glass composites are not suitable for prosthetic socket materials because they are brittle, despite their high tensile strength. This limitation has resulted in the use of nylon, polyester and acrylic and epoxy resins in the manufacture of prosthetic and orthotic devices. The adhesive and mechanical properties of the resins and fibres influence the performance of these products, the report says.
Research company Technavio states in its Global Medical Composite Material Market for Orthopaedics report that medical composite materials are being used in implantable medical devices; and the composite materials help in biocompatibility and osteoconductivity.
Biodegradable polymers are modified with a ceramic component to form implants. Carbon fibre/PEEK polymer composites are also being used to manufacture orthopaedic implantable material as other materials can lead to osteolysis and implant loosening.
Improving robotic devices with composites
In a related development on composite advancements, to improve features of robotic devices, a team from the US agency National Science Foundation (NSF) is tinkering with the idea of using a synthetic material, ionic polymer-metal composite, which is a kind of an electroactive polymer with electricity running through it to change shape, into artificial muscles.
Also called soft robotics, these devices can be more manoeuvrable and have better interaction with humans, the researcher says, adding that the advancement in soft robotics with composite-made artificial muscles will benefit physically challenged people across the globe.
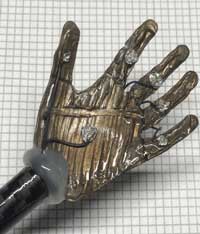
The research team working on the composite muscles is led by Kwang Kim of the University of Nevada, together with researchers from South Korea and Japan. The other US collaborators include the University of Utah, the Rensselaer Polytechnic Institute, and the Polytechnic Institute of New York University.
According to the researchers, creating artificial muscles requires not only developing a powerful, flexible material, but figuring out how to precisely control and cleverly manufacture it. One of the big challenges in soft robotics is finding the right material, which “has to be soft, but also has to produce enough power to do lots of different things.”
Still in its infancy stage, the research is supported by NSF's Partnerships for International Research and Education (PIRE) programme, which supports global research collaborations across all fields of science and engineering.
Biodegradable composites for bioresorbable implants
Bioresorbable polymers, likewise, are capturing a significant share in the medical composites market. MarketsandMarkets reported that major applications such as orthopaedics and drug delivery are boosting demand for bioresorbable polymers. The market size, in terms of value, is expected to reach over US$1.4 billion by 2021, with a CAGR poised at 13.42% between 2016 and 2021.
Equally important as an orthopaedic application in driving market growth is the drug delivery application, which MarketsandMarkets assesses to partake the highest growth rate within five years.
In drug del ivery appl icat ions, as pat ients do not prefer taking injections and other procedures repeatedly, a bioresorbable controlled drug delivery matrix is implanted in their body . This , then, encourages consumers to pay more for the better quality products that do not need to be removed by a second surgery, as they get absorbed in the body once they complete their function.
Meanwhile, researchers at the US Brown University say that the degradation rate of biodegradable polymer polylactic acid (PLA) can be decreased by treating it at various temperatures and pressures, thus broadening the scope of potential medical applications. PLA is a semi-crystalline material with a molecular structure that is partly ordered into crystals whi le the rest is disordered, or amorphous, l ike glass. Work by previous researchers had shown that treating PLA with heat could increase the material’s crystalline makeup, which could help to increase its strength.
Researchers treated PLA samples under different temperature and pressure condi t ions for varying amounts of t ime. The t reatments increased the amount of crystalline area in the material, but there was another , more surpr ising f inding. At higher temperatures and pressures, the amorphous parts of the material became birefringent, meaning that they bend light differently depending upon how the light is polarised. Birefringence is typically observed in crystalline materials, so seeing it in the amorphous regions of PLA was a surprise.
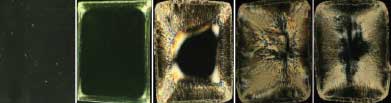
The new amorphous phase combined with the overall increase in crystallinity in the treated samples could have significant implications for the material’s mechanical properties, according to the researchers. The higher crystallinity could make it stronger, while the more ordered amorphous sections could make it last longer. That slower rate of degradation could be particularly useful in medical applications.
If the rate at which PLA degrades can be controlled, the rate at which it delivers a drug can be altered. There is also interest in using PLA for plates and screws used to stabilise broken bones. The advantage of PLA-based implants is that they degrade over time, so a patient would not need a second surgery to remove them. PLA may degrade too quickly for some of these applications, but if this new polymer phase slows degradation, it may become a better option. The researchers plan more research aimed at quantifying changes in material properties as well as investigating whether this phase can be induced in other semi-crystalline materials.
In the same token, German speciality chemicals company, Evonik is researching the potential of using biodegradable composites for bioresorbable implants, to potentially replace metal in implants used for the internal fixation of fractured bones.
Implants play a key role in supporting bones until they heal. Today’s metallic devices typically remain in the body for the rest of the patient’s life or require additional surgery for removal; while, devices made with Evonik’s new composites will be absorbed by the body gradually once the bone healing process has taken place. These materials consist of polymers and of substances that naturally occur in bones.

Benefits include doing away with additional surgical procedures to remove the implanted devices and faster regeneration of bones, says Evonik, adding that it wants to create bioabsorbable implants to replace damaged tissues with healthy tissues. Its current work on biodegradable composites is a first step in this direction, it says.
The company says that its knowledge in PLA “is an excellent foundation for the development of materials and solutions for regenerative medicine.” Resorbable pol ymers are popular in such applications a s dissolvable and drug-eluting stents and implantable fixation devices. In all of these applications, the rate of resorption is a key property.
Consequently, Evonik researchers are exploring composite materials that reinforce biodegradable polymers with inorganic substances, such as derivatives of calcium phosphate. Not only do these additives strengthen the material, they enhance its biocompatibility. As the polymers gradually break down, calcium and phosphate can be absorbed into the newly formed bone tissue.
In the near term and wi th the r ight mater ials, Evonik also plans to dabble in 3D printing to create made-to-measure implants for individual patients.
Cutting-edge laser with ceramics
More popularly associated with pottery, ceramics are also showing beneficial potentials in medical composites. In MarketsandMarkets latest repor t on the technical ceramics market, it highlights the market’s potential worth of US$8.49 billion by 2021. The market, with an estimated CAGR of 6.43%, will be driven partly by increased usage in the manufacturing of medical devices and implants that are used for bone and tooth replacements.
Technical ceramics have been an area of interest for innovat ive medical appl icat ions. One of the more recent concoctions is a ceramic-based laser developed by scientists from the Moscow Institute of Physics and Technology (MIPT). The ceramic laser will be used as a minimally traumatic laser scalpel for surgical operations, and also for cutting and engraving composi te mater ials. Ivan Obronov, a researcher at MIPT, and his colleagues from the Institute of Applied Physics of the Russian Academy of Sciences (IAP RAS), and Moscow-headquartered company, IRE-Polus, used a ceramic obtained from compounds of rare-earth elements – lutetium oxide with added thulium ions (Tm3+:Lu2O3). It was the thulium ions that enabled the ceramic to generate laser radiation.
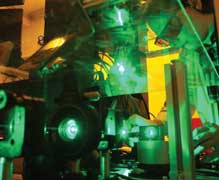
Obronov commented that ceramics are a promising type of medium for lasers because they are produced by sintering powders into a polycrystalline mass. Moreover, the materials are cheaper and easier to manufacture than single crystals, which is important for mass adoption.
The new laser converts energy into radiation with an efficiency of more than 50%, while other types of solid state lasers have an average efficiency of approximately 20%, and it generates infrared radiation with a wavelength of about 2 microns. Radiation from the most common infrared lasers, with a wavelength of about 1 micron, has very little absorption and penetrates deep into biological tissue, which causes coagulat ion and large areas of “dead” t issue. A surgical scalpel needs to “operate” at a very specific depth, which is why 2-micron lasers are used, as they do not damage underlying tissue.
Compared to the usual 2-micron flashlamppumped holmium lasers used by physicians that are expensive and bulky, ceramic lasers are cheaper to manufacture, simpler, more reliable, and four times more compact.
Aside from medical applications, ceramic lasers present more advantages than the widely used 1-micron laser s used for cut t ing metal , wher e polymers are practically transparent to them. However, a 2-micron ceramic laser can effectively cut and engrave plastics, such as composite materials.
Thus, with advancing technology, lightweight and heat-resistant polymer composites, as alternatives to metals and alloys, will play a prominent role in future market growth.
(PRA)Copyright (c) 2016 www.plasticsandrubberasia.com. All rights reserved.