Materials News: Making plastics from food and biomass a reality - August digital issue
Also, download this story from the electronic issue here
Agricultural crops and food wastes are helping restore faith in plastics as an eco-friendly material, says Angelica Buan in this report.
Plastic is shedding its image as an environmental offender with materials derived from agricultural feedstock and wastes. Firms are also starting to embrace the necessity of developing and utilising biobased plastics as part of their sustainability plans.
The market is also becoming favourable towards consumption of eco-friendly products. Allied Market Research finds that the key drivers for the growth of bioplastics market is indeed an increasing adoption of biodegradable plastics that usher in new trends; and increasing popularity of bioplastics use in the end user industries. Nevertheless, there is still the high production cost that gets in between wider adoption and maximised growth.
Food, glorious food
Food, being a renewable feedstock, is now becoming more available and accessible for industrial use. Technology is also enabling agricultural feedstock not to compete with human food consumption; and government policies are incentivising towards utilisation of these renewable resources.
Just the same, challenges in production costs may be surmounted over time, against the environmental savings that can be accrued. For example, Infiniti Research in its Global Bioplastics Market report projects an environmental savings of US$1.3 billion/year if aerated beverage manufacturers utilise algae-based bioplastics.
Meanwhile, according to the United Nations Environment Programme, 5 billion tonnes/year of agricultural biomass waste is produced. Thus, the supply of materials is abundant and often underutilised, yet the materials can be relatively low cost and help manufacturers offset the use of glass fibres and talc for more sustainable, lightweight products.
Seed technologies to harvest bio-oils
Australia’s abundance in safflower has led to the country developing a technology for deriving oil from the flower’s seeds. Currently, the national science agency, Commonwealth Scientific and Industrial Research Organisation (CSIRO) and the Grains Research Development Corporation (GRDC), are involved in a joint project, under Crop Biofactories Initiatives (CBI), to produce safflower seed oil that contains over 92% oleic acid, hence called Super-High Oleic (SHO) safflower.
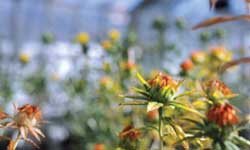
Safflower is easy to grow, is resistant to heat and drought, and is adaptable to dry climates and irrigation and also works well in rotational cropping. Though the agencies say it is currently a relatively minor and underutilised crop in Australia due to a small domestic market for safflower oil. Only about 10,000 ha were grown in 2014 and the seed is mainly used for confectionery and birdseed.
However, the potential is there. CSIRO says that SHO safflower has performed well in field trials. “The oil produced in the seed has significantly higher stability than conventional oils and performs as well or better than synthetic oils derived from fossil reserves. These properties will see it attain a higher market value than normal crop oils, which should be reflected in a higher farm-gate value for growers,” it said.
It also says the stability of the oleic acid makes the bio-oil especially suitable for high temperature industrial applications such as lubricants and transformer fluids, and it can also be processed to build a range of complex polymers for use in bioplastics and surface coatings.
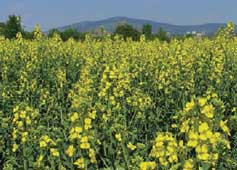
The technology required to produce SHO safflower, consisting of a standard cold press or solvent extraction process used currently to extract seed oil from sunflower, canola, soybean, and cotton, has been licensed to Australian clean technology firm GO Resources, which has expertise in biotechnology, industrial lubricants and oleochemicals. The commercialisation agreement will work towards the deregulation of GM events within Australia aiming for an intended commercial release of SHO safflower by 2018/2019, and the potential to export as much as 125,000 tonnes/year of the bio-oil. CSIRO, GRDC and GO Resources also expect to see significant areas of SHO safflower grown in Australia by 2020.
Meanwhile, a joint venture formed between a unit of French industrial and financial entity, Avril Group, and Israeli start-up Biopolymer Technologies, known as Evertree, will be developing a formaldehyde- f ree addi t ive resin der ived f rom rapeseed meal . The first application for this plant-based alternative to traditional VOC-emitting chemicals, a protein- r ich biomass produced when oil is extracted from rapeseed, will be the wood composite panel industry, with the firm saying that 20-30% less resin will be required for use in wood panels.
With an investment of US$79 million, Evertree expects to start a pilot plant in 2017 in Compiègne, France, and open a production facility in 2018, ramping it up to 50,000 tonnes/year by 2020.
A sweet alternative to conventional foam
Fossil oil-based packaging is no longer palatable for green packaging conscious users . Thus , German chemicals firm BASF is offering a sugar-based alternative, ecovio EA, which is available in the market (with a particle size of 1.05 mm and soon, a 0.8 mm-diameter grade) , as the first expandable, closed-cell foam material that is biobased and certified compostable. It consists of BASF’ s biodegradable polymer Ecoflex and polylactic acid (PLA), which is derived from corn or other sugar-generating plants like manioc.
To produce ecovio EA, expandable granules are charged with pentane blowing agent, thus enabling what the firm says is a trouble-free pre-expansion of the material on conventional EPS pre-expanders and subsequent moulding . The raw granules themselves have adensity of approximately 700g/l.
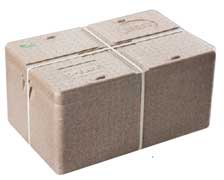
Compared with EPS , the material has lower rigidity and when it comes to its energy absorbing capacity, it comes between EPS and EPP. These properties make it ideal for use in the E&E sector, in particular for heavy and delicate packaged goods such as washing machines or televisions, where a high level of impact resistance and robustness is vital, says BASF.
Furthermore, Ecovio EA has a minimum thermal conductivity of 34 mW/(mK) and is therefore suited to all thermal insulation applications in the transport sector, such as helping to maintain the cold chain for temperature-sensitive goods such as packaged vegetables, fruit, meat, frozen goods or even medicines.
Due to the inherent properties of the raw materials, Ecovio EA can also be stored at temperatures of up to 100°C over a period of several hours and is therefore also suitable for hot-melt adhesive applications. In addition, it also displays good resistance in solvents such as acetone. As a certified compostable product, it also does not contain any flame retardants.
In the future, BASF will also offer Ecovio EA approved for food applications, extending the range of applications to all of the areas in which foam is in direct contact with processed food.
Olive leaves serve as barrier for pasta packaging
A great pasta recipe cannot do without olives. Now, olives can also do wonders for biodegradable and compostable cheese and pasta packaging.
The combination of different layers of bioplastics – PLA, Polyvinyl alcohol (PVOH), and adhesives; and a wax coating obtained from olive leaves – has resulted in a sustainable packaging, suitable for packaging of food in modified atmosphere, insulating the product from oxygen and humidity in order to avoid the growth of bacteria and fungi.
PLA is an easy-recyclable material with mechanical properties, and PVOH provides barrier to gases and is water-soluble, so it disappears in the washing process, thus allowing PLA to be recycled, according to Spainbased plastics technology centre AIMPLAS. Both layers are joined by biodegradable adhesives, while a wax coating made from olive leaves provides water vapour barrier. This coating, which does not disappear in the washing process, acts like a plasticiser for PLA, thus improving its flexibility.
AIMPLAS adds that the new packaging results in a cost 25% lower than conventional packaging, with a lower environmental impact and a lower carbon footprint of up to 29%.
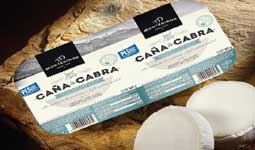
AIMPLAS’s research is coordinated within the European project BIO4MAP. The 30-month long EU-funded project has a budget of EUR1.5 million. The partners for this project include Central Quesera Montesinos, a potential user of the new packaging for goat cheese slices; Vallés Plàstic, responsible for applying a new coating made of natural waxes; and Artibal, a manufacturer of waxes, lacquers and inks, responsible for the formulation.
Other end users of the packaging are Altoni- Kelderman, a Belgian manufacturer of fresh pasta, and Germany-based Sachsenmilch, that packages sliced cheese; French compounding company MAPEA that has developed the biodegradable adhesive together with the research centre; Abo Akademi from Finland; French packaging transforming and manufacturing company Bobino Plastique; and Germany’s technology centre Fraunhofer IVV that developed the coating’s wax.
Perfect brew of bio-coffee cups
Coffee is for drinking, but can you also drink from coffee? German company Kaffeeform answers this riddle with its cups made of dried coffee grounds combined with a biopolymer to produce durable and dishwasher-safe coffee cups and saucers.
The coffee grounds are leftovers from brewed coffee, waste that is usually recycled as fertiliser or incorporated in beauty products or scrubs, if not thrown away in landfills. But German product designer Julian Lechner has found a creative use for this waste.
A coffee-drinker himself, Lechner first hatched the idea of creating crockery with coffee grounds, while attending university in Italy.
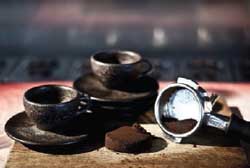
After several attempts, he developed a method of combining 40% coffee grounds with wood grains and a biopolymer of cellulose, lignin, and natural resins. He explains that a firm known as Mosaik helps dry and pack the ground coffee, and pack the finished product while a factory in Baden-Württemburg mixes the coffee waste with wood grains, biopolymers and natural fibres; and the mixture is sent to Cologne for melting and compression into moulds.
One cup and saucer can be made from the waste of six consumed cups of espresso. The creator of Kaffeeform coffee cups and saucers is planning to launch more products like sheets and travel mugs.
Tequila and cars – a combination made in bioplastics
Drinking and driving is not an advisable combination but not for this partnership that will utilise plant wastes obtained from manufacturing tequila for the automotive sector.
US-headquartered Ford Motor Co has tied up with family-owned and operated tequila connoisseur Jose Cuervo to develop sustainable bioplastics from the distilled beverage maker’s agave plant byproduct and for use in automotive parts.
Ford and Jose Cuervo are testing the bioplastic for use in vehicle interior and exterior components such as wiring harnesses, HVAC units and storage bins. Initial assessments suggest the material shows durability and aesthetic qualities. Success in developing a sustainable composite could reduce vehicle weight and lower energy consumption, while paring the use of petrochemicals and the impact of vehicle production on the environment.
The growth cycle of the agave plant is a minimum seven-year process. Once harvested, the heart of the plant is roasted, before grinding and extracting its juices for distillation. The Mexican tequila producer uses a portion of the remaining agave fibres as compost for its farms, and the rest are turned to paper and crafts by local artisans. With the partnership with Ford, the waste fibres can now be utilised for automotive parts.
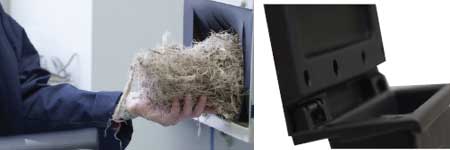
The collaboration with Jose Cuervo is the latest example of Ford’s innovative approach to product and envi ronmental stewardship through the use of biomaterials. Ford began researching the use of sustainable materials in its vehicles in 2000. Today, the car maker uses eight sustainable-based materials in its vehicles including soy foam, castor oil, wheat straw, kenaf fibre, cellulose, wood, coconut fibre and rice hulls.
Oil not just for frying
Recycled cooking oil is definitely a no-no in a healthy diet. But used cooking oil can still be put to good use without the fear of high cholesterol!
India-based manufacturer of speciality polymers, compounds and additives Vikas Ecotech is converting waste cooking oil into bioplastics. The Delhi-headquartered company has partnered with Czech Republic-based Nafigate Corporation, which will provide technology, for converting waste cooking oil into biopolymer PHA.
Nafigate’s Hydal technology can process waste cooking oil through fermentation and subsequent PHA polymer isolation. PHAs are used in the production of bioplastics.
Vikas Ecotech, which is currently constructing the first phase of its manufacturing plant and innovation centre at Dahej, Gujarat, to produce 6,000 tonnes/year and 5,000 tones/year of organotin stabilisers and speciality polymer compounds, respectively, is already converting waste cooking oil into plasticisers for plastics and rubber, using a technology called Wastol-P. It says that the addition of Hydal technology is expected to further bolster the company’s position in the area of bioplastics.

Hence, surprising discoveries on how food and biomass can be transformed into plastic materials continue to excite the industry, and in the long run pay heed to the environment.
(PRA)Copyright (c) 2016 www.plasticsandrubberasia.com. All rights reserved.