Plastic wastes for sourcing energy and fuel
Also, download this story from the electronic issue here
Plastic wastes as feedstocks are helping pedal the wheels of a closed-loop economy through energy recovery technologies that are able to extract valuable products such as oil, gas and electricity from solid wastes, says Angelica Buan.
More than 50 years ago, marine litter was almost unheard of, except for a few anecdotal reports of indigestible materials eaten by marine animals that have led to what was considered the first scientific studies on plastic waste ingestion by seabirds like the Laysan Albatross.
Plastics comprise the larger bulk of wastes , according to studies collected and summarised by Litterbase, an online portal for marine litter that aims to prune down results from more than a thousand scientific studies into easy-to-understand global maps and figures.
Litterbase summarises the proportion of different litter types in di f ferent realms. Currently it has condensed over 1,300 scientific publications, which showed plastics as a dominant material in the litter mix. In terms of global composition of marine litter, for example, plastics account for 60.89% of total based on 401 publications, and covering 1,626 locations. It also contributes to more than half of the litter composition in the seafloor; and to nearly 80% on the sea surface.
Plastics are deemed the biggest culprit here. However, the initiation of a closed-loop economy (also known as the circular economy model), whereby recovered wastes become resource is turning the tide for plastics.
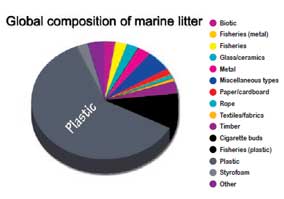
The European Commission (EC) , a leading campaigner for a circular economy, says that marine litter is “one of the clearest symbols of a resource inefficient economy”. I t adds that “shifting our perspective on waste plastics as valuable materials rather than envi ronmental plague enables the awareness that these materials, once recycled, can be pumped back into the economy.” The EC claims that the circular economy approach, which puts the emphasis on waste prevention, recycling and reusing of materials/products, is the “best solution to the marine litter problem”.
Plastic wastes as assets rather than liabilities – China an example
Plast ic wastes have become int r insic to growing economies, as urbanisation, fast-paced lifestyle and rise in affluence are portent for throw-away convenience of modern packaging and portability of lightweight items made of plastic.
The World Bank’ s data revealed that global municipal solid waste (MSW) generation levels will continue to rise from 1.3 billion tonnes/year to 2.2 billion tonnes/year by 2025.
Most emerging economies are generating more waste than they can manage. The 1.3-billion populated China tops the 2015 marine litter study led by University of Georgia research on 20 top countries with mismanaged waste. The study, which based its figures on 2010 estimates, cited China as responsible for 11% of plastic litter and hogging 76% of mismanaged waste. The country is exploiting means to halt the waste plague, one of which is to recycle 23 million tonnes/year of waste plastics by 2020.
China also takes credit as being the first country to convert waste plastics to fuel/oil (WTF). In 2001, an oil refinery in Hunan province successfully processed 30,000 tonnes of plastic wastes into 20,000 tonnes of provincial standard-compliant gasoline and diesel oil. The technology used for the process was not disclosed but Dr Mae-Wan Ho of the Institute of Science in Society, author of an article on plastics to oil, guessed that thermal depolymerisation was used.
According to a recycled plastics and WTF forecast by
Transparency Market Research (TMR), depolymerisation or pyrolysis is the basis for WTF conversion technology.
The technology, i ts disti l lates and other refined
petroleum products complement already existing
traditional plastic recycling processes. In short, it serves
a dual purpose: it forms a reliable source of alternative
energy from an abundant feedstock having negligible
economic value and is an eco-friendly disposal of nonrecycled
plastics.
Like any other technologies, commercialisation is key to wider adoption of WTF. According to the TMR study, pol icymakers and energy indust ry player s in North America and Europe are focusing on the commercialisation of the technology.
Thus, investments are being piped in to increase plastic recycling capacity. While the West is leading, the Asia Pacific market , likewise, is modernising different WTF technologies and countries such as Saudi Arabia, Brazil , and the UAE, are also contributing, TMR reports.
Breakthroughs in recycling technologies
Crossing out landfilling, a 2016 Science for Policy report by the Joint Research Centre (JRC), the EC’s science and knowledge service, says recovery of energy content of combust ible waste is an ideal option, especially for wastes that are not recyclable.
Currently , new recycling technologies are
advancing. An example i s UK-based Recycling
Technologies’s RT7000, a chemical recycling plant
capable of processing up to 7,000 tonnes/year of all
types of plast ic wastes, including non- recyclable
plast ic waste. The technology, which Recycling
Technologies describes as “the greenest and cheapest
solutions yet for end-of-life plastic”, produces refined gas that is condensed into Plaxx, while the noncondensables
are recirculated back into the process.
Petrochemical/oil giant Shell’s foray into WTF is a
technology called IH2 at its newly opened Bangalore
Shel l Technology Cent re in Bangalore, India.
The technology was developed by US-based Gas
Technology Institute (GTI) in 2009 and has licensed
it to CRI Catalyst Company, Shell's catalyst business,
for exclusive worldwide deployment. The centre is
helping pioneer efforts, using the IH2, to turn forestry
and agri-wastes; and MSW into transportation fuels,
with a new demonstration plant being built at the site.
No-waste solution to manage waste – India an example
Meanwhile, India is making a case with its eco-friendly waste management solution. The country was ranked 12th in the University of Georgia’s study of top 20 polluting countries. As the country generates more than a 100 million tonnes/day of MSW, the government had to increase its adoption of waste management solutions, including wider implementation of the plastic bag ban. But being a staunch innovator, India utilises waste plastics in building asphalt-modified roads, which has halved construction costs.
In between these efforts , a unique process was developed by the Indian Institute of Petroleum (IIP) to deal with recycling of PE and PP, which account for more than half the total amount of plastics consumed in the country. The technology can convert the PE/PP wastes to gasoline, diesel or aromatics, while simultaneously producing LPG in each case.
For 1 kg of clean waste PE around 750 ml of
automotive grade gasoline or 850 ml
of automotive
grade diesel or 500 ml of toluene and xylene-rich
aromatics can be produced. IIP describes the process
as completely environment - friendly, leaving no
toxic residues. IPP says that the process is ready for
commercialisation.
Not only can the adoption of this process free urban and semi-urban areas from too much plastics use, it can also generate jobs and provide livelihood for the community.
A viable option for sourcing electricity
Waste-to-energy (WTE) via thermal (incineration, gasification, pyrolysis) or biological, as a method for solid waste treatment holds huge growth potentials. Grand View Research reports that the WTE market size will reach US$44 billion by 2024.
The European WTE market led the global industry in 2015. The region is projected to grow at a CAGR of 6.2% over the forecast period, against the back of stringent regulat ions to minimi se industrial waste. Countries such as Germany, Austria and the Netherlands have adopted WTE technologies to utilise industrial waste.The European WTE market led the global industry in 2015. The region is projected to grow at a CAGR of 6.2% over the forecast period, against the back of stringent regulat ions to minimi se industrial waste. Countries such as Germany, Austria and the Netherlands have adopted WTE technologies to utilise industrial waste.
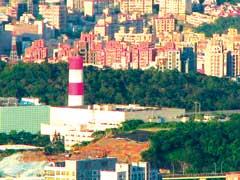
Asia Pacific is projected to account for the second largest share of the market. Emerging economies, such as India and China, have been wi tnessing a sharp increase in energy demand on account of rapid industrialisation and urbanisation, which has prompted energy producers to look for alternative energy sources. Since these countries generate a lot of industrial waste, they have become high potential markets for WTE technologies and are expected to provide ample opportunities to companies involved.
Meanwhile , Taiwan’s venture into WTE complements its landfilling of MSW. With limited landfills, the 23-million populated Taiwan, which generates about 942 kg/person/day (citing 2012 data by Global Alliance for Incinerator Alternatives) of MSW, is turning to incineration or combustion as its primary method of waste treatment.
Since WTE is a viable technology for energy recovery and electricity generation, the Taiwan Environment Protection Agency (EPA) has adopted a one incinerator per county plan. In 1990, it built 21 large-scale WTE incinerators and 15 MWS incinerators in 1996. These are located mostly in the west coast of Taiwan where there is a higher concentration of inhabitants, especially in Taipei and Kaohsiung City, which have highest number of WTE plants.
The government ’ s “Zero Waste Policy” has seen most, if not all, of its MSW being carted to incinerators, which for the long term are being transformed into regional biomass centres for comprehensive classification and zero waste process, and resource recycling.
So far , the country’s recycling rate has been exemplary. According to the latest data of National Statistics of Taiwan, the country has recycled 3 million tonnes of waste, comprising 6,447 tonnes of plastic packaging and 275,221 tonnes of plastic containers.
The recycling efforts are partially to augment its energy requirement since the country imports almost 98% of its energy, according to EPA Taiwan.
The WTE plants’ output is estimated to total more than 18 tonnes/day of MSW, or 85% of the 21,900 tonnes-design capacity. Per year, the plants process 65% of the total MSW generated or 7.2 million tonnes.
In a related development, a new technology known as R-One (Regenerative Oil New Energy) has been developed by Taipei-based EVP technology utilising plastic waste as feedstock . For one standard production line, 20 tonnes/day of MSW can be converted, such as plastics bags, disposable containers, food packaging, films, cables, and nonrecyclable scraps from PE, PP, PS, nylon, or others, EVP technology said.
It uses a proprietary patented method to compress
the scraps into R-ONE Compressed Feedstock or RCF.
Majority of the plastics are converted into light fuel
oil, and other by-products in smaller quantities like
carbon black and gas. EVP technology said that one
standard production line produces 17 kL light, lowsulphur
renewable oils (85%), 2 tonnes of carbon
black (10%), and syngas (5%).
As the world seeks out better solutions to solid waste and marine litter problems, more WTE and WTF technologies are expected to be developed. These will bring back the material assets in plastic wastes that would have otherwise been lost in landfills as well as aid nature in its work of breaking down waste that usually takes million years to be decomposed. It is hoped that the WTF and WTE technologies will be able to accomplish this – all in a matter of minutes.
(PRA)Copyright (c) 2017 www.plasticsandrubberasia.com. All rights reserved.