Davis-Standard, extending its reach to Asia
Also, download this story from the electronic issue here
Global extrusion systems manufacturer and supplier Davis-Standard is staying ahead of the curve. The specialist in high-performance plastics and rubber extrusion and converting systems, adopts the mission of supplying technologically-advanced solutions to the processing industries. At Chinaplas 2017, the US-headquartered company, that has a regional manufacturing presence and full-scale R&D laboratory in Suzhou, China, will display the HPE-H extruder at Hall 9.2, Stand J41.
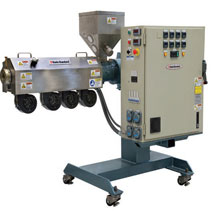
According to market research company Ceresana, in its latest report on flexible plastic films, the sale of plastic films for the packaging, agriculture, construction and technical sectors will reach a volume of about US$250 billion until 2024.
Emerging countries in the Asia-Pacific region, particularly China and India, are expected to expand their packaging requirements, owing to rapid industrialisation and urbanisation, among other aspects in the region.
Plastics are also enablers of healthcare innovations and medical breakthroughs due to their barrier properties; light weight, low cost, durability, compatibility with other materials, and sterilisability, among other characteristics.
One of the most important developments in modern healthcare that is aided by medical-grade plastics is the rising preference for minimal to non-invasive surgeries and diagnostics, as well as drug delivery systems, all of which require precision devices.
This trend bodes well for the medical tubing market, which is poised to nearly double from US$3.7 billion in 2015 to US$5.8 billion by 2021, or an estimated CAGR of 8%, during the period covered by research firm Markets & Markets.
The report predicts further growth for the medical tubing market, given that awareness about healthcare has significantly increased; and quality of healthcare delivery has become pivotal to the extent that government initiatives and policies are including healthcare and medical infrastructure in priority agenda.
As the market needs become more sophisticated, the requirements for processors and machinery suppliers are being increased, to up the ante with innovative processes.
Thus, extrusion systems supplier Davis-Standard, LLC offers solutions that impact everyday life, from food packaging and data cables to IV tubing. In other words, the markets served by Davis-Standard are broad, ranging from packaging, construction, medical, consumer products and electronics to automotive, agriculture, energy, and more.
What’s more, the company offers a comprehensive range of plastics and rubber extrusion machinery, wire/cable machinery, blow moulding machinery, and converting systems and technology; as well as a full range of extrusion aftermarket services.
PRA caught up with Davis-Standard President/CEO Jim Murphy to find out more about the company’s plans for the year and highlights from last year.
- What has Davis-Standard lined-up for this year’s Chinaplas 2017 show in terms of technology offerings?
- Davis-Standard, Hall 9.2, Stand J41, will promote its growing regional presence and capabilities during the upcoming Chinaplas show. As an example of the company’s extrusion technology, Davis-Standard will exhibit an HPE-H extruder for medical tubing applications.
- The HPE-H offers a compact design and is one of the industry’s most widely used extruders. Available in 20 mm, 25 mm, 30 mm, 40 mm, and 45 mm sizes, the HPE-H is known for a fast delivery and rugged design that is energy efficient and easy to maintain.
- Which growth markets is Davis-Standard looking at expanding to?
- As far as geographic markets, we seek to be strong in every market where we have a presence. North America and Europe continue to be staples for us. China, the rest of Asia and South America continue to present growth opportunities that we will capitalise on.
- With regards to applications, we can support all of them no matter where our customers are located. Film, extrusion coating, sheet and medical tubing are among our strongest areas worldwide.
- Davis-Standard also continues to enjoy strong growth in the Chinese marketplace, benefitting from a regional manufacturing presence and full-scale R&D laboratory at Davis-Standard (Suzhou) Plastics Packaging Machinery Co., Ltd.
- Davis-Standard has continued to gain market share in China due to outstanding customer service, innovative feedscrew designs, control systems and modular technologies.
.jpg)
- How has the Suzhou facility contributed to the company’s services since it opened in 2012?
- Last year, Davis-Standard grew its sales team in Asia while also increasing manufacturing and laboratory capabilities at its subsidiary in Suzhou, China. This has improved Davis-Standard’s response and delivery time while providing versatile and cost-competitive equipment options.
- Davis-Standard now manufactures several products in Suzhou including extruders up to 114 mm, PLC control systems, high-speed systems for medical tubing and a full offering of wire and cable systems. Additionally, the facility is equipped for gearbox and control panel assembly and refurbishing services, and there are plans to add fabrication and assembly of downstream equipment.
- Regional manufacturing has been key to Davis- Standard’s ability to serve every major converting and extrusion market in Asia. To support regional customer trials and application development, the Suzhou laboratory offers a high-speed FPVC extrusion system and multi-purpose microbore tubing line.
- The FPVC line is capable of line speeds from
5 to 100 mpm for processing 2 mm to 8 mm
OD tubing with accuracy of +/-50 microns. Line
components include a 63 mm extruder, 8 m watercooling, precision internal air supply, OD gauge and combination puller-cutter.
- The multi-purpose microbore tubing line is
designed for single or dual-layer tubing, and
single lumen tubing with or without a stripe. It is equipped with two extruders, OD/ID wall thickness measuring and controlling system, closed-loop control via vacuum sizing tank and puller, and a high level central control system.
- How will China’s Made in China 2025 agenda impact Davis-Standard?
- The Made in China 2025 agenda is consistent with our plan to support our customers in Asia from our Suzhou site. We will continue to add capabilities and products to support the high growth in the region.
- With the full integration of Gloucester Engineering Company (GEC) technology into Davis-Standard, how has this expanded the offerings from Davis-Standard?
- Gloucester Engineering Company (GEC) has always been a market leader. Having the brand under our umbrella broadens and strengthens our product offering in blown film, cast film and foam sheet.
- Together, we offer industry technology that is going to be tough to beat. We offer aftermarket support to the largest installed base of GEC equipment including opportunities to improve performance and machine control upgrades.
- Our customers now benefit from single-source
manufacturing and service from a company with
one of the largest installed base of blown film
equipment in the world. This includes lines from
one to 11 layers and up to 9 m in width, preengineered
options, precision gauge control,
air rings, screw designs and dies from 7-11
layers, plus pending innovations to improve
productivity further.
- In fact, Davis-Standard recently patented a spiral design for reducing thermally sensitive polymer degradation in blown film dies and has provisional patents for a unique driven lay-on winder and self-threading winder.
- Fully integrating GEC also included an expansion of our primary manufacturing facility in Pawcatuck, Connecticut. The 15,000 sq ft addition is complete with manufacturing cell for producing highly technical blown film dies used in multilayer packaging and pharmaceutical applications.
- Since end-users/consumers are more aware now when it comes to quality and cost effectiveness of products across a majority of applications, how does Davis-Standard contribute to these changing consumer standards?
- Davis-Standard is committed to supplying advanced extrusion solutions to the global polymer and rubber processing industries, providing exceptional value to our customers.
- Our laboratory in Suzhou is a huge part
of supporting the healthcare/medical tubing
sector. Healthcare continues to grow in Asia
and the need for medical products and devices
grows with this demand.
- Plastics are a high-performance material
for the medical industry, providing disposable
products that reduce the possibility of
infections. We are seeing increased
development of multi-layer structures and
smaller diameter tubing to provide better
- physical property performance across a range of new applications. Customers are able to test new resins and processes prior to making a large capital investment. The versatility of our systems is also essential.
- We’re able to accommodate customers with
technology that addresses a variety of tubing. In
the flexible packaging market, Davis-Standard
developed the dsX flex-pack™ (extrusion coating).
- Asian converters are seeking the advantages of high-speed lamination, subsequent waste reduction and improved quality offered by this machine. The economical benefit of these 450 mpm machines is allowing many regional converters to separate themselves from the competition. The flex-pack is also built with an adaptable machine configuration to support a variety of end-use markets.
- Packaging continues to grow in Asia based on strong demand for packaged products and continued growth of the economy. Flexible packaging is growing faster than the overall packaging market due to the many benefits it provides. Flexible packaging provides a lightweight package that is durable and often re-sealable – these are features that consumers desire.
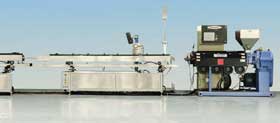
- What strategies does Davis-Standard employ to stay competitive?
- Davis-Standard is recognised as the global leader in high-performance plastic and rubber extrusion and converting systems.
- Our capabilities go far beyond our extrusion technology and extruder processing equipment. They extend to our professional design engineers, laboratory personnel, training experts, talented commercial force, hands-on field engineers, and aftermarket parts and service specialists.
- As a team, we work together to support our extrusion and converting customers from the very first inquiry to commissioning and final acceptance of the project, and beyond. Our focus has always been, and continues to be, excelling in price, performance, delivery and service.
- What were the highlights of the company last year?
- We finished 2016 stronger than 2015, with a 10% growth, and anticipate 2017 to be even better.
- One of the highlights of 2016 was the transition of our blow moulding accumulator head production to Fulton, New York.
- We also created a new cutting and feeding machine for low voltage wire and cable processes for insulating applications. This unit facilitates timely transfers from one take-up to another and minimises operator involvement, speeding up reel change.
- We introduced a new energy-efficient barrel heating/cooling system to reduce energy consumption by up to 50%. The patented design acts as a blanket for the extruder and is available on new machines or as a retrofit for existing machines.
- We developed an extruder adapter called the QSE (Quick Screw Exchange) to enable fast screw changes without dismantling feed pipes - a big time saver!
- For thin substrates, we engineered a high-speed film and foil unwind for 800 mpm splice speeds for sensitive webs such as aluminium foil at 6 microns.
- Lastly, we installed the largest seven-layer blown film die in the world. The 2.3-m, seven-layer Centrex IBC die is for agriculture applications.
- For more information about Davis-Standard’s regional capabilities, visit www.davis-standard.com
Copyright (c) 2017 www.plasticsandrubberasia.com. All rights reserved.