Medical Sector: Transforming patient care with next generation medical-grade plastics
Leading resin providers are offering advanced materials that improve the production of medical devices, promising to elevate patient care and enhance treatment outcomes, says Angelica Buan in this article.
Plastics technology is a perennial force in modern healthcare, enhancing cost-effectiveness, safety, and hygiene while driving innovation. Commonly used yet essential medical devices such as syringes, IV bags, catheters, surgical tools, and prosthetics rely on plastics for their versatility, strength, and lightweight properties.
These advanced plastics are engineered to offer enhanced functionality and performance, such as better biocompatibility and resistance to environmental stressors. Furthermore, the development of eco-friendly innovations, such as recyclable and biodegradable materials, helps mitigate the environmental impact of single-use items while maintaining high standards of patient care.
According to a recent report by Vantage Market Research, the global medical plastics market is projected to reach nearly US$51 billion in 2024 and US$86.4 billion by 2032, with a CAGR of 7.9% during the forecast period. This growth reflects the increasing importance of advanced plastics in healthcare technologies and their role in treatment success, ultimately enhancing patients’ quality of life.
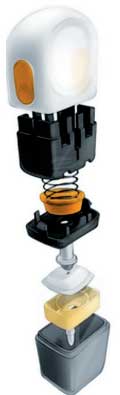
Resins for high precision, high performance components
Medical-grade resins are significantly improving the performance and reliability of high-precision medical devices. Chemicals firm Sabic has introduced a medical-grade PBT, Valor HX325HP, designed specifically for injection moulding components such as insulin delivery pens, insulin pumps, autoinjectors, and continuous glucose monitors.
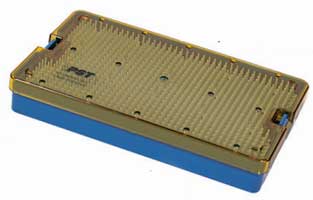
The new medical-grade PBT resin is said to have passed rigorous injection moulding trials, showing high flow even in complex designs and mould release properties with lower shrinkage variation, compared to competing engineering plastics.
This resin also offers robust resistance to a wide range of chemicals, minimising environmental stress cracking (ESC), and is compatible with ethylene oxide (EtO), gamma irradiation, and steam sterilisation. The resin also offers a formaldehyde-free alternative to polyoxymethylene (POM) materials. It is available as an unreinforced, neat material and in a limited range of standard colours, according to Sabic.
In a related development, Sabic showcased its Ultem HU resins at a US trade show earlier this year. These resins are designed to offer medical device manufacturers alternatives to EtO sterilisation.
Ultem HU resins are stable across various sterilisation methods, including vaporised hydrogen peroxide (VHP) gas plasma, steam autoclave, gamma radiation, electron beam, X-ray, and ultraviolet-C. They can endure multiple sterilisation cycles while maintaining high strength, dimensional stability, and aesthetic quality, potentially extending the lifespan of devices made from these materials. The Ultem HU resins are available in different grades: Ultem HU1000, an unfilled polyetherimide (PEI) with mechanical and thermal properties, and Ultem HU1004, a PEI blend offering enhanced ductility and hydrostability. Both grades are biocompatible, chemically resistant, and inherently flame retardant.
The unreinforced Ultem HU resins’ strength and stiffness make them suitable for replacing metal in medical device components.
Subscribe to Get the Latest Updates from IMA Please click here
©2024 Injection Moulding Asia. All rights reserved.