Green tie-ups: Schneider Electric/GR3N partner on open automation system for recycling industry; Dow-Mitsui Polychemicals market biomass EVA/LDPE
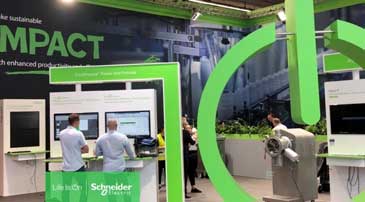
Digital transformation of energy management and automation firm Schneider Electric has partnered with PET recycler GR3N to create the first open automation system for the advanced plastic recycling industry, to allow the scaling up of GR3N’s chemical recycling technology for PET.
With 50% of global plastic waste ending up in landfills and only 9% recycled GR3N developed MADE, the Microwave Assisted DEpolymerization solution. This new process breaks down PET into its chemical building blocks that can be recombined to create new PET pellets with virgin-like quality for packaging and textiles, effectively closing the loop for hard to recycle plastic. The technology is based on alkaline hydrolysis, and it can manage a higher amount of impurities compared to the existing ones.
In March 2024, GR3N successfully demonstrated MADE and the power of Schneider Electric’s open automation technology, EcoStruxure Automation Expert at its demonstration site in Italy. MADE plant is conceived to anticipate the usage of all the technologies that will be finally adopted for the first industrial-scale facility, foreseen to be installed in Spain and with an expected capacity of over 40.000 tonnes/year of PET waste treated. The intrinsic modularity of GR3N’s proprietary recycling process has allowed MADE to be the first plastic recycling plant to use the shared automation runtime managed by Universal Automation, based on the IEC 61499 standard.
The software-defined automation system decouples hardware from software, allowing devices and equipment to be freely connected across architecture layers, regardless of manufacturer. It acts as the digital backbone of industrial operations at the plant, providing the foundation to make more informed decisions. This approach allows MADE to be also technological demonstration of a new generation of automation systems, where the intertwining between OT and IT enables the exploitation of advanced functionalities for operations management and data analytics.
“Through software-defined automation and hardware independence, we have been able to effectively de-risk our operations and push the boundaries of our technology,” said Fabio Silvestri, Head of Marketing and Business Development at GR3N. “We’ve been able to reconfigure our systems quickly when we see opportunities to improve efficiency, while avoiding supply chain issues due the hardware agnostic nature of the system. This is what is needed to make advanced plastic recycling at reality at scale.”
Due to EcoStruxure Automation Expert’s modular, agnostic nature, GR3N was able to choose the optimal technology for the demonstration plant and easily scale to new sites. Benefits include:
- Industrial scalability – significantly minimizes the risk of investment during the scale-up of GR3N’s technology towards the First of a Kind (FOAK) industrial plant, while offering a new way to protect its intellectual property as process licensor.
- Design flexibility – vendor and hardware agnostic system enabled GR3N to design the best possible solution without being held back by vendor lock in or being impacted by supply chain issues.
- Engineering time and time-to-market reduction – the modular design of control software, supported by digital continuity across the whole plant lifecycle with automation-focused decision making happening at conception, reduces human error at the development stage by 40%.
- Control simplification – Vendor-independence allows controls to be distributed or centralized depending on need.
- New opportunities – OT/IT integration provides new opportunities for efficiency and optimization across the whole value chain. thanks to a seamless incorporation of advanced data analytics techniques.
- Reduced costs – the software-defined approach to automation is expected to reduce engineering costs by 30%.
- Next-gen workforce – attracts the next generation of workers with a systems that shared similarities with those in IT.
The partnership between GR3N and Schneider Electric, that has started with the signature of a Memorandum of Understanding, will enable the chemical recycler to scale operations to new sites quickly and cost-effectively. The solution is expected to reach industrial scale by 2027 with the construction of a 35-40 kilotonnes/year plant which will include the pre-treatment, depolymerisation and repolymerisation.
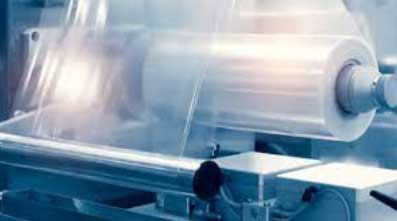
In other news, Japan’s Mitsui & Dow Polychemicals have started marketing biomass ethylene vinyl acetate copolymer (EVA) and biomass low density polyethylene (LDPE) based on the mass balance method.
Biomass EVA and biomass LDPE have the same resin properties as conventional petroleum-derived products because the raw material, biomass ethylene, exhibits the same physical properties as conventional petroleum-derived ethylene. Therefore, they can be easily switched from conventional products, while contributing to the reduction of GHG emissions over the entire product life cycle.
Since obtaining the ISCC PLUS certification at its Chiba Plant (Ichihara City, Chiba Prefecture) in May 2024, it has been preparing to start production and marketing of biomass EVA and biomass LDPE products.
Subscribe to Get the Latest Updates from IMA Please click here
©2024 Injection Moulding Asia. All rights reserved.