Green tie-ups: Covestro/Li Auto collaborate on sustainable material solutions for EVs; Lygos/CJ Bio to partner on biorefinery plant in US
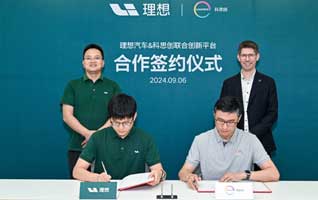
The automotive industry is undergoing a profound transformation driven by electrification, autonomous driving and the shift towards a circular economy. Responding to these trends, materials manufacturer Covestro has entered into a Memorandum of Understanding (MOU) with Chinese electric vehicle maker Li Auto to cooperate in the development and application of more sustainable engineering plastics with alternative feedstocks, such as bio-waste and recycled sources, across various automotive components.
Covestro and Li Auto will establish a “Joint Innovation Platform” Key initiatives will involve integrating materials attributed with bio-circular content through mass balancing into automotive lighting, functional interior and exterior parts, and smart system components. The two sides also agreed to explore innovative processes and business models for using recycled lighting materials in new automotive parts together with value chain partners.
Under the joint platform, the two sides also seek to deepen their collaboration in developing lighting, smart systems, and thermal management solutions. This will include high-performance optical-grade materials, smart surface technologies and thermally conductive solutions.
The two parties also unveiled two jointly-developed, industry-leading materials: innovative light-diffusing and infrared-transparent Makrolon polycarbonates. The light-diffusing polycarbonate allows for a more refined and evenly-distributed illumination effect for smart headlights.
Meanwhile, the new infrared-transparent polycarbonate achieves a high transmittance of over 85% in the near-infrared spectrum. Compared to conventional black polycarbonate, which absorbs solar energy across the entire spectrum, this new material significantly enhances the light aging resistance of components, contributing to greater durability for the smart headlights of Li Auto.
“Li Auto is dedicated to implementing the ‘Smart + Electric’ strategy with innovative materials and designs, aiming to offer users a safer, more comfortable, convenient and refined travel experience,” said Liao Mengjun, Vice President of R&D Operations at Li Auto. “Our partnership with Covestro will expedite our exploration in advanced materials, supporting the ongoing enhancement of user product demands.”
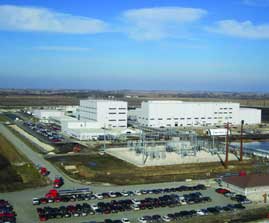
Meanwhile in other news, speciality chemical firm Lygos is partnering with fermentation and biotechnology firm CJ Bio to build a facility in Fort Dodge, Iowa, US, that will produce 40,000 tonnes/year of biodegradable polyaspartates and biobased malonates from aspartic acid and malonic acid.
Lygos has developed yeast strains that can convert sugar into the two organic acids, which are normally derived from fossil fuels.
CJ will use that technology to produce the acids at a plant in Fort Dodge, where it already makes fermentation-derived amino acids. Lygos will build adjacent facilities that chemically transform the acids into products with applications in personal care, coatings, and agriculture.
The facility location features 100% renewable electricity, access to sustainable feedstock, and excellent logistics, making it an ideal location to build a biorefinery. CJ’s existing site is next to Cargill’s Fort Dodge Corn Mill, which will provide utilities and access to plant-derived sugar, a biobased feedstock that can be fermented into the key intermediates for Lygos’ products. Lygos is expected to employ up to 350 temporary workers during construction and create approximately 60 highly skilled jobs once the facility is fully operational.
The company says the site could eventually produce up to 100,000 tonnes/year of biobased chemicals.
The initial phase of Lygos’s project would result in one of the largest biobased chemical plants in the US.
Qore is building a facility that will produce 65,000 tonnes/year of biobased 1,4-butanediol using technology from Genomatica. Solugen is building a plant to make 75,000 tonnes/year of biobased glucaric acid, gluconic acid, and hydrogen peroxide.
According to Lygos CEO Eric Steen, polyaspartates can be used to make products as diverse as fertiliser additives to increase nutrient uptake and corrosion inhibitors for water treatment.
Like aspartic acid and malonic acid, succinic acid can be transformed into multiple derivatives.
Soltellus polymers are sustainable, biodegradable, and water-soluble with applications in home care, personal care, agronomy, and water treatment.
Ecoteria malonates offer safety, sustainability, performance, and supply resiliency benefits in fragrances, coatings, agriculture chemicals, pharmaceuticals, and other specialty applications.
Subscribe to Get the Latest Updates from IMA Please click here
©2024 Injection Moulding Asia. All rights reserved.