Arburg’s latest all-electric machine boasts slimmer design
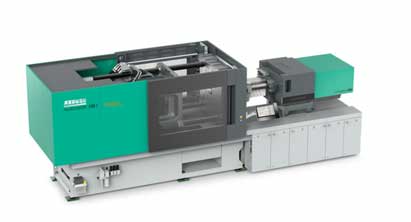
Germany-based machine maker Arburg is pulling all the stops on its latest electric machine: the new Allrounder 720 E Golden Electric with a clamping force of 2,800 kN. It extends the product range of the electric series and boasts a slim design with a price to match, adds the machine maker that will showcase it at Fakuma 2024 (hall A3, stand 3101) trade fair in Germany. It combines electrical precision, process stability and a small installation area with high component quality, low investment costs and short delivery times, says Arburg.
The extension of the electric machine portfolio helps customers to meet current challenges such as increasing price pressure coupled with rising costs for labour, energy and materials as well as ever-shorter product life cycles and faster product changes. To enable attractive investment costs and a rapid return on investment (ROI), Arburg uses standardised equipment without compromising on quality and performance. So the new "Golden" combines a high level of precision with a slimline design at a particularly attractive price/performance ratio.
Arburg has optimised the design so that the new Allrounder 720 E Golden Electric, with a width of just 1,848 mm, has a significantly reduced installation area compared to other machines in its class. This has been achieved through features such as a new safety door with recessed handles. At the same time, the door opening has been widened to 1,400 mm, making the ejector area more accessible, for example. Due to its smaller installation area, the new Allrounder fits into existing production grids and lines. This is of particular interest when old machine technology needs to be replaced. However, even for new production facilities that are being planned, every achievable space saving is a valuable resource. Thanks to the slim design, more machines can be set up in injection moulding production, resulting in an increased output per square metre.
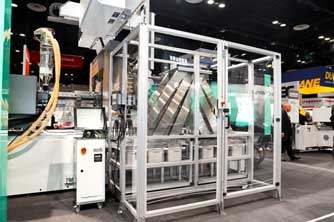
The Allrounder 720 E Golden Electric also includes a toggle-type clamping unit and direct drives from Arburg's subsidiary AMKmotion. With an electric mould height adjustment system, mould installation heights of up to 800 mm are possible. The drive components are optimised for a clamping force of 2,800 kN. The proven high-quality Arburg plasticising with the "aXw Control ScrewPilot" ensures reproducible injection and moulded part quality.
Optimised mould venting with two-stage mould locking also plays a part in this. For convenient maintenance, the new electric Allrounder has the same easily accessible control cabinet concept as the new hybrid machines. A lubrication unit and an optional pneumatic system are located on the operating side. The parts chute in the machine base has been widened, making it easily accessible.
The new electric machine is not limited to a specific product and is quickly available, which is particularly advantageous for short-term replacement purchases and capacity expansions. It is relevant for almost every industry and of particular interest for technical injection moulding. Other typical areas of application include dimensionally stable housings for electromobility, thick-walled closures for household goods, precision components for medical technology, and the construction and leisure industries.
It is equipped with the Selogica ND control system as standard. If required, additional options and functions such as core pulls and heating and cooling circuits can be easily integrated and programmed, enabling a wide range of plastic parts to be produced flexibly, efficiently and reliably.
At Fakuma the 2,800 kN exhibit will be equipped with a Multilift V 30. With a size 800 injection unit, it will be producing PP razor covers by way of example. A 24-cavity mould from Hack will be used. The cycle time is around 11.5 seconds, with each moulded part weighing 1.2 g. The 24 finished parts are then ejected in groups of four, clustered by cavity, into six boxes.
The company will also show its "Moldlife Sense" computer system that enables sensor-controlled mould monitoring over the complete life cycle and detects changes to the mould at an early stage. The measured values from various sensors on the mould can be visualised in the machine controller. If these are outside specified tolerances, an event is automatically generated. The same applies to the indicators for the built-in acoustic emission sensors, where the "noise ID" is visualised and checked to see whether it is within the given tolerances. Individual events, such as warnings, alerts and error messages, can also be displayed in the controller and documented. This allows users to identify anomalies in the process quickly and reliably and better assess what needs to be done. In an emergency, the machine stops and issues a corresponding message so that the operator can react correctly.
Subscribe to Get the Latest Updates from IMA Please click here
©2024 Injection Moulding Asia. All rights reserved.