Smart functions integrated with DirectCoating coated parts technology
Car manufacturers and their suppliers face the challenge of integrating smart functions such as display and ambient lighting and touch control, in addition to a wide range of visual and haptic surface properties.
Above all, the aim is to manufacture durable products cost-effectively to achieve broad acceptance in the industry. The goal is car interiors that can easily serve as a lounge, workspace and driver cockpit. In this way, an environment can be created in the car that combines comfort and infotainment with a feeling of safety.
Thus, to allow more design freedom and functionality in car interiors in a cost effective manner, German materials company Covestro worked with a team of three industry partners: coatings specialist Votteler Lackfabrik GmbH & Co. KG, laser texture specialist Reichle Technology Center and pearl effect pigments manufacturer Merck KGaA.
It developed what it says is an effective concept for the production of interior parts with seamless, intelligent surfaces using Covestro’s DirectCoating technology. The coated component is produced in two steps using a polyurethane reaction injection moulding (PU-RIM) process.
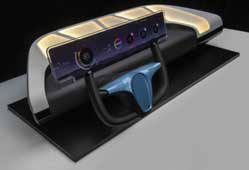
Puriflow paint systems from Votteler Lackfabrik enable surface properties such as good scratch resistance and a selfhealing effect, but also a feel that ranges from soft leather to hard metal. In implementing the solution, Votteler drew on the manufacturing expertise of Reichle, which operates Europe’s largest laser texturing site. The company provided laser-textured PU-RIM moulds for the project.
Covestro, meanwhile, supplied process technology know-how, coating raw materials from its Desmodur and Desmophen ranges without solvent additives, and Makrolon and Bayblend polycarbonate plastics. Effect pigments from Merck can be used to achieve various colour and transparency effects.
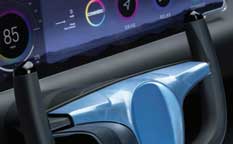
In Covestro’s DirectCoating process, the plastic substrate is first produced in an initial cavity by injection moulding. The resulting part is then transferred to a second, minimally larger mould.
The cavity between the substrate and the laser-engraved RIM mould corresponds exactly to the desired volume of the coating that is injected there. This creates a coated precision part in just two steps. It requires little rework and is highly resistant to chemicals and daylight, adds Covestro. DirectCoating also offers advantages over conventional coating methods, including a shorter and faster process, no overspray and no need for a separate drying step.
(IMA)Subscribe to Get the Latest Updates from IMA Please click here
©2021 Injection Moulding Asia. All rights reserved.