Consortium develops lower-cost and lighter battery for e-mobility
Although millions of electric cars and plug-in hybrids from many manufacturers are already on the road, there are still no generally recognised standards for the individual components in terms of service life or materials used. Moreover, the vehicles themselves are under rapid development.
One way of increasing the range of electric cars is by improving battery storage capacity and through efficient energy recovery. A second approach is to reduce the weight of the individual components, in order to reduce the energy needed to overcome driving resistance (tyre rolling, inclination, and acceleration).
The effect of weight reduction on the efficiency of the drive depends on the propulsion strategy of the electric vehicle.
Thus, a consortium consisting of Lorenz Kunststofftechnik, Forward Engineering, Evonik, LION Smart, Vestaro, and Minth (the European headquarters of Chinese automotive supplier Minth Group) has developed a solution to help improve efficiency through lightweight construction.
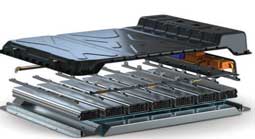
In late 2019, work started on a brand-independent, lowcost battery housing solution in different sizes for electric vehicles. The result of the cooperation was a significant weight reduction of the battery by about 10% over other commonly used material combinations, without sacrificing any mechanical properties. In addition, the glass fibre-reinforced epoxy SMC – purpose-developed for the battery housing – meets all fire resistance requirements and is easy to work, even with complex geometries. The entire concept has been tested and shown to be suitable for series production and is said to be safe even under extreme conditions.
Components used in lightweight construction for hybrid and electric vehicles, such as battery housings, must not only be low in weight, but also exhibit high rigidity and strength. Carbon fibre-reinforced SMC materials can be used for this purpose, but they are very expensive and typically non-recyclable. Beyond that, there were few available materials with the necessary attributes, as they were either too heavy or had insufficient mechanical strength.
For the battery housing, Evonik’s Vestalite S epoxy hardener was used to develop a new SMC with a density between 1.5 and 1.7 g/cm³. It also features a bending strength of > 350 MPa, a flexural modulus of elasticity of > 18,500 MPa, and an impact resistance of > 150 kJ/m2.
By using an epoxy resin instead of the usual polyester resin, it was possible to eliminate other problems that normally arise in working with glass fibre-reinforced SMC materials. The moulding material can be worked into complex geometries without adhering to the mould, the formulation has better mechanical properties than conventional SMC materials and features good fibre course in the moulding process, say the firms.
Moreover, Lorenz has an established process for recycling glass fibre-reinforced SMC materials, which is an important consideration given the sustainability requirements in the automotive industry.
For the supporting structure of the battery housing, the cooperation partners chose aluminium as a proven lightweight material. The general goal for the supporting structure was simple geometries and thus lower production costs.
“The bottom plate is the basis of the entire battery construction and has cross-members that the battery module is mounted on. The carrier plate for the battery management system is also attached to the aluminIum base,” reports Philipp Taschner, Project Engineer of Vestaro.
Two aluminium deformation elements provide the necessary side impact protection through absorption. The module alignment of the battery cells enables separation of the electric poles, which provides higher safety in the event of a crash and enables easy cooling.
Another partner LION Smart’s supercell concept was used for the batteries. “The design of the battery cells with a low number of components is intended for fully automated, cost-efficient production,” explains Taschner. “In addition, the battery design is particularly safe, as the individual cells are enclosed in a non-flammable dielectric coolant.” This not only provides higher safety, it also ensures a constantly low average temperature within the battery, which reduces cell aging. The modular series connection design of the battery also allows flexibility in the number of modules, with a very low overall height of 90 mm.
Furthermore, to verify the safety of the concept and its viability under conditions of actual use, the Computer Aided Engineering (CAE) department at Forward Engineering performed structural and safety simulations, according to Taschner.
The tests included a simulation of overall torsion and bending rigidity, lateral pole impact of up to 350 kN and short pressure resistance in thermal runaway, all of which were passed without problems. The limited mechanical performance of the base structure resulting from its intentionally simple geometry was effectively compensated by the optimised GF SMC, thanks to the design freedoms provided by the material.
The insulating properties of the epoxy SMC housing came to the fore in the thermal 2D simulation of the battery pack, noted Lorenz, adding that the material can withstand 10 minutes at 800°C without burning through, and its insulating properties protect surrounding components and materials from temperatures over 300°C.
In the past, glass fibre-reinforced SMC materials have been difficult to work with, so this point was likewise thoroughly tested.
Lorenz made multiple complex hardware demonstrators to verify the series suitability of the material and the production process, by using Evonik’s diamine-based epoxy hardener to create a simple and fast-curing SMC material with the required mechanical properties.
The company also adds that it was able to have curing times of three minutes in tests, without workpieces adhering to the mould. Moreover, the SMC with Vestalite S has no styrene emissions and only low VOC emissions.
The cooperation partners have made several configurations of their battery concept.
“Currently, we offer three energy configurations, which are competitive with or superior to current battery models on the market in terms of energy density, safety, and costs,” says Taschner.
“With all-in weights of 412.1 kg at 65 kWh, 527.3 kg at 85 kWh and 789.2 kg for the configuration with 800 V at 120 kWh, and the modularity and flexibility of the overall concept, we consider ourselves in a very good position to compete with other suppliers,” he concludes.
(IMA)Subscribe to Get the Latest Updates from IMA Please click here
©2021 Injection Moulding Asia. All rights reserved.