Automation: The era of human/robotic collaborations
With human workers and robots beginning to work together in tandem, automation for output-intensive industries has come of age, says Angelica Buan in this report on Industry 5.0.
Modern twist to industrial revolution
Industrialisation has increased overall economic output, creating more jobs and raising living standards. Obviously, the industrial revolution aims to advance technology, socioeconomics, and culture – but at what cost? Workers were displaced by migration throughout the early stages of industrialisation, and they endured low wages, long hours of toil, and exploitation.
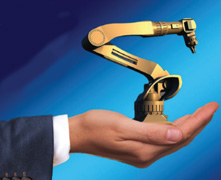
The term “industrial revolution,” which was once used to describe economic and industrial developments in Europe and the US between the 18th and 19th centuries, has been given a modern twist. As demand for goods begins to exceed output from conventional machines, the second wave of the industrial revolution aims to boost productivity and efficiency with technologies.
The use of robots, artificial intelligence (AI), and smart machines became increasingly important in the latter stages of the industrial revolution. This, however, led to the perception that such technologies will eventually infiltrate manufacturing floors, render human labour obsolete, and disenfranchise humans – much like in sci-fi movies.
Moreover, the cyborgification of industries, in response to the skilled labour shortage, has sparked an uncanny valley fear that a robot will outperform a human worker. Newer generation technologies, such as collaborative robots or cobots, are, nevertheless, reducing human hostility towards them. It’s only a matter of time before a peaceful coexistence between humans and robots becomes a reality.
Remedy to close the gap in skilled labour shortages
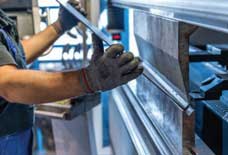
The generational skilled labour shortage has been a barrier to achieving full industrial ambitions. For years, unemployment has been at an all-time high, yet thousands of skilled jobs have gone unfilled, owing to a lack of training and experience, to name a few factors.
The recent pandemic has been a disruptive factor to the labour climate. Although deemed to be only a temporary situation, the pandemic has caused an employment crisis with many businesses ceasing operations, or reducing capacity. Indeed, the pandemic has put to the test not only the manufacturing sector’s resiliency, but also its ability to recover.
In the US, the manufacturing industry lost more than 500,000 jobs in 2020 during the pandemic, according to findings by Deloitte and The Manufacturing Institute, which polled an online research of more than 800 US manufacturers across all sectors, between December 2020 and February 2021.
The Deloitte study revealed that the pandemic cost the US manufacturing industry 1.4 million jobs, but 820,000 of those jobs were rehired by the end of 2020.
The irony, according to this report, is that there were roughly 500,000 positions available, mostly for qualified people that could not be filled. By 2030, the US manufacturing industry is expected to have 2.1 million skilled labour vacancies.
This opinion is also echoed by US advocacy group National Association of Manufacturers (NAM)’s recent Manufacturers’ Outlook Survey, which had 453 responses in August. Recruiting and maintaining qualified employees, as well as supply chain and logistical difficulties, and healthcare expenses, were cited as top challenges by respondents.
Meanwhile, the expanding skilled labour gap is being exacerbated by digitalisation, automation, and an ageing population.
In a recent article titled “Creating pathways for tomorrow’s workforce today”, Deloitte stated that the rapid digitalisation of the manufacturing industry will almost certainly continue to reshape human labour, adding that it will be a challenging factor over the next ten years.
The reason for this is that the skills required to perform jobs in a smart factory will most likely differ from those required today. Unfortunately, many of these talents are lacking in today’s manufacturing workforce and if this issue is not addressed, vacancies will increase, affecting productivity, innovation, competitiveness, and the GDP.
Automation as a disruptive force
Worker safety and efficiency remain central to technologically-driven industrial shifts. Worker safety has improved as a result of automation. Furthermore, the introduction of AI-connected technologies and robotics has improved manufacturing efficiency and productivity, particularly in major industries such as the plastics industry, where manufacturers are focused on lowering costs while increasing capacity and output.
The application of software-integrated machines that either stop or alert the operator when it detects a defect or self-adjusts to ensure that processes are not disrupted is on the rise. These machines allow for greater precision and less wastage on the factory floors.
While machines and robots will never completely replace humans in the supply chain, they help relieve employees of redundant, highly technical, and physically demanding tasks while assisting organisations in improving their bottom lines.
Thus, does automation create more jobs? According to an article published by Forbes and World Economic Forum (WEForum), automation will result in a 58 million increase in employment. Automation is anticipated to turn two-thirds of occupations into higher-skilled jobs, while the remaining one-third will become lower-skilled jobs.
Cobots in the plastics industry
The plastics industry, which every year has new technologies being launched, has also borne the brunt of a gap in skilled workers. While robots are generally used to augment this shortage, especially in areas that require precision and consistency, they do not necessarily disregard human interaction.
Cobots are robotic assistants to human workers that help them be more productive. They are less expensive than traditional industrial robots used for automation, costing less than a quarter of the price. They are safe to use and are equipped with sensors and other devices to ensure that they behave appropriately, particularly when working in close proximity to humans. In many industrial settings, cobots work alongside humans, but they accomplish tasks independently or sequentially.
Industrial robots are mostly used in injection moulding applications in the plastics sector, automating processes without requiring human interaction. They are required in environments where human error is to be avoided.
Cobots, on the other hand, are designed with human safety in mind (unlike traditional industrial robots) and to function in close proximity to employees, preventing workplace risks by being disabled with just a light touch. For industries, cobots can increase productivity in the manufacturing line and the ability for businesses to expand.
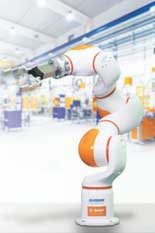
It can be recalled that German multinational chemical company BASF, in 2017, showcased its prototype cobot for industrial use, made by Siasun, one of China’s largest robotics manufacturer. The cobot, showcased at a Guangzhou-held plastics event, is built with BASF’s Elastollan thermoplastic polyurethane elastomer (TPU), Ultramid glass fibre-reinforced PA and 3D-printed PA6. The partnership is part of BASF’s Trio project, which brings together prominent designers and brand owners. According to BASF, its Elastollan TPU and Ultramid PA are easier to process than standard materials and allow for more colour and decorating options, while allowing for flexible manufacturing. Because cobots are only employed when they are needed, a lightloading cobot will be easier and faster to move about the manufacturing site.
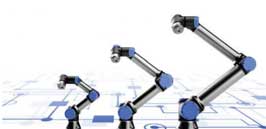
BASF adds that cobots made with its elastic material solutions allow for good insulation and elastic properties, providing greater shock absorption and thus making flexible manufacturing safer as well as more user-friendly for humans.
Similarly, cobot innovation is the focus of a tie-up between French manufacturer of robots Sepro Group and Universal Robots (UR), a Danish manufacturer of smaller industrial collaborative robot arms.
Sepro’s Visual Control System will be integrated with UR’s cobots as part of the agreement. Sepro created the Visual Control Platform specifically for robots used in injection moulding equipment and is featured in all its products, including co-branded lines, with the same user interface of any robot types.
Sepro adds that it will be able to offer a comprehensive range of automation solutions to injection moulders as a result of the new cooperation. Cartesian robots, six-axis articulatedarm robots, and now cobots are all part of this portfolio, according to Sepro. It added that cobots, like the sic-axis robots, are well-suited to peripheral operations that are in high demand in the plastics industry.
The integration also allows processors to build safe, open configurations for a variety of processes, such as peripheral operations or advanced automation cells, Sepro furthered. Both the partners’ solutions enable faster process creation and installation, resulting in easy to deploy and testing of post-processing operations and turn-key automation systems.
Meanwhile, Swedish industrial robot supplier and manufacturer ABB offers its range of cobots, which feature the speed, robustness, and precision of an industrial robot while also having the safety features and ease of use of a cobot.
Early this year, ABB introduced its CRB (Collaborative Robot) 1100 SWIFTI, which combines a payload of 4 kg and reach of up to 580 mm; and GoFa CRB 15000. The latter features intelligent sensors in each joint to support close human and robot collaboration, enabling reach and speed for payloads up to 5 kg.
These new cobot versions of ABB’s IRB 1100 industrial robot joined the YuMi and Single Arm YuMi (introduced in 2015) in the company’s cobot portfolio for applications ranging from less than 0.5 kg to 5 kg.
According to ABB, SWIFTI has a maximum Tool Centre Point (TCP) speed of more than 5m/second, which is more than five times faster than other cobots in its class and comparable to industrial robots. Easy to use and install, safe working zones for the robot can be configured using SafeMove’s simple fast setup tools, such as the SafeMove Configurator App on the ABB FlexPendant. Users can programme the cobot either via a clip-on lead through programming device, or ABB’s new Wizard easy programming software.
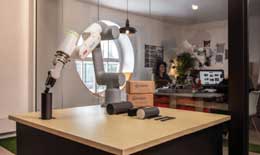
Both SWIFTI and GoFA have capabilities that allow them to function alongside humans without the need for physical barriers or fences, saving both space and money.
Thereby, allowing a robot and a human to work together in the same space and on the same tasks, without sacrificing speed or safety, results in maximum flexibility and efficiency; and above all, harnesses the combined power of a human mind and machine.
(IMA)Subscribe to Get the Latest Updates from IMA Please click here
©2021 Injection Moulding Asia. All rights reserved.