K2022: injection moulding machinery and automation highlights
Moulding Machinery
- At the K2022, Germany-based Arburg is showing its
largest injection moulding machine hybrid Allrounder
1120 H. The 6,500 kN exhibit is integrated with a turnkey
system with robotic systems for foil and parts handling
and finishing using hot stamping. The AI-supported
variant analysis is newly integrated for the production of a
premium tool case in the Arburg design
Over-moulded 3D design films on the corners of the toolbox, for example, provide the necessary styling and high-grade aesthetics. A Scara robot processes the film inserts from project partner, Leonhard Kurz, while further handling is taken on by a linear robotic system, the Multilift V 40. The films undergo in-mould lamination in the injection mould and are refined afterwards with embossed Arburg lettering in a hot stamping station. The lid and lower tray are discharged via a conveyor system. The toolboxes are completed manually outside the turnkey system using pre-manufactured components like centre section, handle, closing clips and feet, and then given to the trade fair visitors.
The exhibit with Gestica control system has lots of smart functions, such as the new Varimos plug-in from Simcon for AI-supported variant analysis. Through the cross-linking of the software with the Gestica control system, even more precise machine parameters can be generated during the filling simulation with the “aXw Control FillAssist,” and the configuration of moulded part and injection mould shortened from several weeks to a few days. - Austria’s Engel will showcase its e-motion 160 combi M machine with a clamping force of just 1,600 kN and a horizontally rotating turning plate. Under clean room conditions, the all-electric machine will produce two-component sample containers for medical diagnostics in a 32-cavity mould on a minimised system footprint. In a first injection moulding step, the base body, which has cylindrical cavities, is injected from black-coloured PC. Then the turning plate rotates 180 degrees in order to close the cylinder on one side with lens-shaped covers in the second moulding step with transparent PC. At the same time, another set of tool bodies is produced on the other side of the insert. The two tools, each with 32 cavities, come from Hack Formenbau.
- Germany’s KraussMaffei will showcase the production
of PP insulin pen caps on an all-electric PX 200-1400 in
a cleanroom design, with mould temperature control. It
allows for fast and precise filling of the 96 cavities, thanks
to a plasticising drive with increased drive power. An
enhanced electric ejector drive allows clean demoulding in
a cycle time of 6 seconds and a shot weight of 105 g.
On a downstream mill, these caps are subsequently shredded to regrind, for an upcycling process with a ZE 28 BluePower twin-screw extruder. Here, additives such as adhesion promoters and liquid colour will be homogenised to create the recompound that goes to the next new 13,000 kN powerMolding machine, where an automotive front-end carrier made from 100% recyclate will be produced. - Swiss machine maker Netstal will mould a thinwall 150- ml, IML-finished yoghurt cup from certified renewable PP from Sabic on ots Elios 4500, which now features a fully electric clamp unit. By switching to all-electric mould closing, Netstal says the machine’s dry cycle is now 0.1 sec faster while average power consumption is reduced by 7kW and the machine is 450 mm shorter.
- German-Japanese machine maker Sumitomo (SHI) Demag will introduce the new high-speed Pac-E series, based on the El-Exis SP hybrid platform and IntElect all-electric series. It features a new injection unit developed specifically for high-speed packaging. At the show, it will have an all-electric 350-tonne model with a 72-cavity cap mould, to show that the electric model can achieve the same cycle time as the El-Exis.
- Wittmann Battenfeld, together with its customer
Wago, has studied the possibility of how continuous
solar cell-powered current can be used for running
machinery, without loss by first passing through inverters,
transformers and high-voltage power lines. It has
demonstrated the solution on its all-electric EcoPower
series, and applied for a patent jointly with Wago.
At the show, an EcoPower 180/750+ operating with direct current will produce an electrical part for Wago from flame-retardant PA on a 24-cavity mould supplied by Wago. The parts are removed by a modified Wittmann WX142 robot in a DC version powered directly via the intermediate DC circuit of the EcoPower, for lower energy costs via direct use of renewable energy like solar power, and the direct current can also be stored in conventional batteries. - Taiwanese machine maker Fu Chun Shin Machinery (FCS) will debut an all-electric multi-component injection moulding machine series, with 1,800-2,800 kN clamping force. It features a rotary table that is up to 50% faster, more stable switching speeds and a positioning accuracy of up to 0.005°. The spars are not held by the plates to reduce pollution, abrasion and power consumption, making the machine suitable for medical products. The use of servomotors and several independent cylinders for injection reduces cycle time, while the linear guide on the injection unit ensures that the back pressure during injection approaches 0, thus reducing overflow of the melt.
- Haitian Group will feature five machines, including three from its Zhafir electric line. On the 122-tonne Zeres Med series it will demonstrate a cleanroom set-up utilising a laminar airflow box from German cleanroom equipment provider Max Petek. Also, an electric 305- tonne Zhafir Zeres Multi series will feature a piggybackstyle auxiliary injection unit, moulding tape-measure housings from ABS and TPE, while a 370-tonne hybrid Zhafir Jenius series will mould an automotive part handled by a Success 33 robot from Sepro. A two-platen servohydraulic 460-tonne Haitian Jupiter will mould a fruit box from HDPE and TetraPak recyclate compound and in packaging, a servohydraulic Haitian Mars K series, with injection speeds up to 1,000 mm/second, will produce an IML food container
- Since Italy’s injection moulding machinery maker Negri Bossi became a part of Japanese firm Nissei Group in 2020, both companies will exhibit under one booth. Nissei will debut an allnew all-electric machine, as well as an update to its existing PLA bioresin moulding package, and exhibit an automotive application targeting electric vehicles. Regarding PLA and bioresin processing, Nissei said it will build upon its exhibit at K2019 where it moulded thinwall transparent PLA champagne flutes.
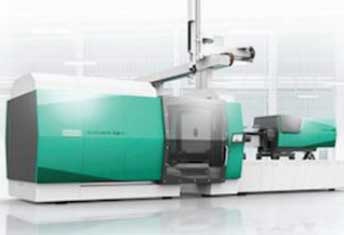
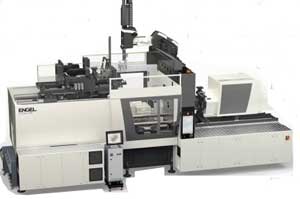
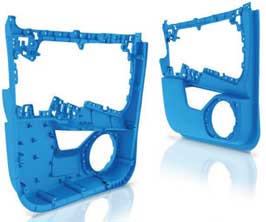
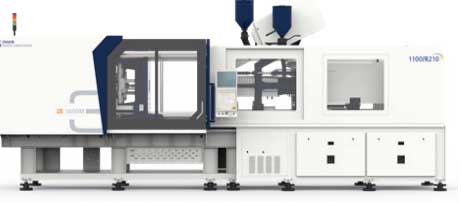
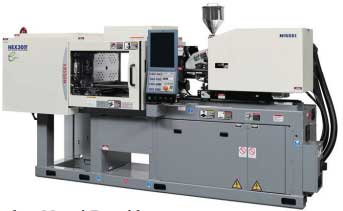
Subscribe to Get the Latest Updates from IMA Please click here
Home | Terms & Conditions | Privacy Policy | Contact | Webmail | Site Map
©2022 Injection Moulding Asia. All rights reserved.