Green tie-ups: Lanxess/BP join forces on renewable raw materials; Dow and Haldor Topsoe to turn waste plastics into circular plastics
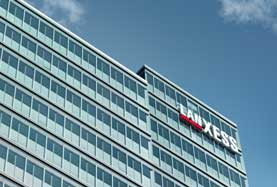
German specialty chemicals company Lanxess and energy company BP are entering into a strategic partnership for the use of sustainable raw materials in high-tech plastics production. BP will supply sustainably produced cyclohexane to the Lanxess’ production site in Antwerp, Belgium, starting in the fourth quarter of 2021. The sustainable origin of the raw materials is certified according to ISCC Plus rules (“International Sustainability and Carbon Certification”).
Lanxess uses cyclohexane as a precursor in the production of polyamide 6, a high-performance plastic that is used primarily in the automotive industry as well as in the electrical and consumer goods industries.
BP uses bio-based and bio-circular feedstocks for the production of “green” cyclohexane. These can be, for example, rapeseed oil or biomass.
“The chemical industry plays an important role in the expansion of the circular economy and efficient sustainable management. To meet the global challenges of climate change, creative approaches to solutions and collaboration are needed in service of our customers. We are pleased to accompany Lanxess as a strong partner with a broad portfolio of raw materials from renewable sources,” says Wolfgang Stückle, Vice President Midstream Refining and Specialities Solutions Europe and Africa of BP.
“High-performance plastics are the solution for many sustainable products, for example in various e-mobility applications. It is now important to also make the production of this valuable material sustainable. In this context, the use of bio-based raw materials, along with modern recycling processes, is a key lever. We are delighted to have bp as a strategic partner at our side,” says Marcel Beermann, Head of Global Procurement and Logistics at Lanxess.
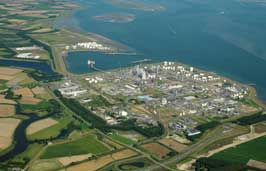
In other news, US chemical firm Dow and catalysts firm Haldor Topsoe will leverage lab-scale capabilities to support the design and engineering of the new 10,000-tonne/year market development unit (MDU), which will be built at Dow’s site in Terneuzen, the Netherlands, to convert waste plastics to circular plastics.
Waste plastics in the environment is a climate issue. Advancing the circular economy for plastics maximises the sustainability benefits that plastics bring across the value chain in a more carbon-efficient way. The construction of a market development purification unit will help solve a key challenge in closing the loop for waste plastics.
Topsoe will support Dow in meeting its 2030 circularity targets, including Dow’s target to enable 1 million tonnes of plastic to be collected, reused or recycled through its direct actions and partnerships.
“Advancing the circular economy for plastics requires scale for feedstock recycling and clean up that does not yet exist broadly, so we are partnering to help accelerate it,” said Diego Donoso, President of Dow’s Packaging and Specialty Plastics business. “Leveraging Haldor Topsoe’s technology and expertise will help us de-risk scale-up of purification capabilities aligned with our efforts to Stop the Waste and Close the Loop.”
The objective for Dow’s new purification MDU is to validate the technology to produce circular products and to accelerate the scale needed to support strong market demand for circular polyethylene.
PureStep utilises Topsoe’s hydroprocessing technology to remove impurities from liquified feedstock. This means new plastics can now be created from low-grade mixed waste - including tyres, municipal solid waste and products containing PVC. Not only does this revolutionary solution remove the need of fossil-based resources, it also reduces reliance on costly and time-consuming sorting or decreases used plastic going to landfill or incineration.
(IMA)Subscribe to Get the Latest Updates from IMA Please click here
©2021 Injection Moulding Asia. All rights reserved.