Green news: Producing apparel from waste oil; Sabic/Microsoft make the first “mouse” with recycled ocean plastic

A demonstration plant for industrial-scale production of polyamides (nylon) applicable to many production sectors, including fashion. Putting sustainability and circularity principles into practice. An investment of almost EUR6.2 million, of which a EUR1.7 million grant from the Region of Piedmont.
A pioneering objective: for the first time, to demonstrate the feasibility of industrial-scale production of polyamides (nylon) starting from bio adipic acid obtained from renewable raw materials, including waste oil and by-products of the oil industry. Potential application sectors for the process and products are textile/fashion, automotive, design, electrical and electronics. This major sustainability-and-circularity-oriented goal has been achieved by RadiciGroup, an Italian multinational headquartered in Bergamo, a producer of a wide range of chemical intermediates, polymers, high performance engineering polymers and advanced textile solutions.
The research was conducted through the Ulysses project and experimentation was performed in collaboration with research centres and universities. Partial funding was received from the Region of Piedmont, within the scope of the “Call for Proposals IR2 (Industrialisation of research results)”. The ambitious, innovative multiyear project was launched in March 2018 and stemmed from RadiciGroup's desire to increase the sustainability of its products, whilst delivering the same quality and performance as required by product standards. What is more, the Group wanted to meet the demand coming from its various strategic sectors, in line with the European targets for the development of low-emission businesses and a circular economy.
The funding amounted to EUR6.2 million, of which EUR1.7 million was contributed as a grant by the Piedmont Region. This investment confirms RadiciGroup's great commitment to scientific research, which is strongly supported by the Group’s shareholders.
The Ulysses project focused on three main areas of research, all of which had the same general approaches: firstly, the experimental processes developed within the Ulysses project framework were industrialisation oriented; secondly, they had a strong innovative component; and, lastly, they implemented the principles of sustainability and the circular economy in real-world applications.
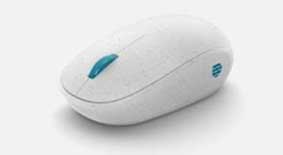
Meanwhile, as part of a new effort to advance the use of recycled ocean plastic, chemical firm Sabic and Microsoft Corporation have collaborated to create Microsoft’s first consumer electronic product – The Microsoft Ocean Plastic Mouse – with an exterior shell containing 20% recycled ocean plastic.
Ocean plastic is defined as plastic that has been certified by a third party as recovered from any ocean or ocean-feeding waterways or where it washed ashore from these locations. Ocean plastic differs from ocean-bound plastic in that ocean-bound plastic is recovered from ocean-feeding waterways, shorelines, and inland areas within a 50-km radius of the ocean. The two recycled products play complementary roles in helping address the issue of ocean plastic waste.
Microsoft began this project with an objective of creating a plastic resin made from at least 10% recycled ocean plastic as part of its commitment to achieve zero waste by 2030. After hearing the initial vision for the project, Sabic joined the effort to source the recycled material and to formulate a resin that satisfied Microsoft’s demanding quality standards. The Microsoft design team collaborated with technologists at Sabic to provide feedback on prototypes made with the new resin. This effort resulted in several rounds of reformulation prior to arriving at a final version that exceeded Microsoft’s initial 10% goal. The final product contains 20% recycled ocean plastic by weight in its external casing or “shell.”
The collaboration envisions Sabic providing a new Xenoy resin for Microsoft product use that is comprised of 20% ocean plastic, as part of Sabic’s Trucircle portfolio and services. This new Xenoy resin with recycled ocean plastic can help reduce plastic waste in the ocean. For example, based on a resin grade comprised of 20% recycled content, for every 1 kilotonne of product containing recycled ocean-plastic Xenoy PC/PET compound, an equivalent of 24 million single-use 0.5 liter PET water bottles is removed from the ocean, ocean-feeding waterways, or ocean-adjacent shores.
This project has also provided a blueprint to demonstrate to the broader industry sector that recycling and reusing valuable plastic resins that have been recovered from the ocean, ocean -feeding waterways or where they have been washed ashore from these locations, is achievable when value chain partners use their knowledge and expertise and work together.
The collaboration builds on Sabic’s announcement in April of this year that it had become a frontrunner in the industry for the development of ocean-bound plastics. These ocean and ocean-bound materials form part of the Trucircle portfolio and services, which showcase the company’s circular innovations and can help to provide our customers with access to more sustainable materials.
(IMA)Subscribe to Get the Latest Updates from IMA Please click here
©2021 Injection Moulding Asia. All rights reserved.