Green tie-ups: Walki/Lactips to develop biodegradable/paper food packaging; Indorama/Suntory collaborate on commercialised PET bottles from bio-paraxylene
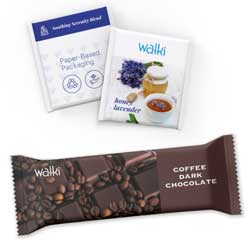
The EU has taken the lead in addressing the growing plastic waste problem with the Single-Use Plastics Regulation, pushing customers in the food packaging industry to find ways to replace traditional fossil-based plastics with biodegradable alternatives. The SUP regulation targets plastics products that are typically used once and then discarded such as yoghurt cups, salad bowls and snack pouches.
Finland’s Walki Group has been working on developing a wide portfolio of biopolymer materials for several years and is collaborating with different companies that develop natural polymer-based coatings. There are numerous sources of natural polymers such as cellulose, algae and even chitin derived from insects and crustaceans, that can be used as a substitute to fossil-based plastics.
Walki has now entered into a strategic partnership with Lactips, a French startup that develops and produces industrial plastic-free natural polymers, to develop a paper-based food packaging material with a polymer coating based on casein.
“When you process milk, you end up with casein as a side stream. Lactips has developed this casein into a bio-based natural polymer that is 100% biodegradable. Thanks to its water solubility, the material is recyclable in the paper stream without leaving any microplastics behind or polluting the wastewater streams. Finding the optimal material that protects the food from being spoilt while still being fully biodegradable is challenging. Casein ticks all the boxes when it comes the SUP regulation,” explains Mats Käldström, Manager, Development & Innovation at Walki Group.
Lactips will provide Walki with the casein-based polymer, while Walki will do pilot trials on an extrusion line in its Technical Competence Center in Pietarsaari, Finland. During the partnership spanning two years, Walki will also conduct properties analyses for the produced materials regarding coating weight, adhesion, barrier and heat-sealability properties.
Walki has a long tradition of collaborating with universities, customers and startups to develop future-proof solutions.
“We are proud to collaborate with Walki to create innovative, fully recyclable solutions for the food packaging industry that are fit to be recycled in the paper stream. This partnership combines our expertise in formulation and development of natural polymers with Walki's state-of-the-art production capabilities, marking an important step towards reducing plastic waste and advancing circularity in packaging solutions. We are delighted to work with a partner who shares our values of sustainability and environmental responsibility, strengthening our shared commitment to a cleaner, plastic-free future,” says Bertrand Dupeyroux, Vice President Sales & Marketing at Lactips.
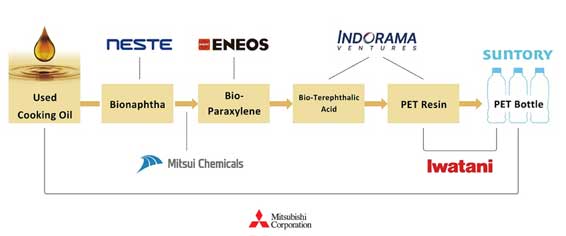
In other news, Thai integrated chemical firm Indorama Ventures Public Company Limited, as part of a supply chain collaboration with Japan’s Suntory, Eneos Corporation, Mitsubishi Corporation, Iwatani and Finnish materials firm Neste, will launch what it says is the world’s first bio-PET bottle for commercial scale, made from ISCC+ certified bio-paraxylene. It adds that “this collaboration marks a significant milestone in the journey toward sustainable packaging, introducing PET bottles derived from used cooking oil. PET bottles made from this technology can significantly reduce CO2 emissions of products”.
From November onwards, the Suntory Group will successively introduce these bio-PET bottles for selected products in Japan. The collaboration will see the launch of approximately 45 million PET bottles for beverages made with this innovative material with further introduction for Suntory products to be considered in the future.
Each company brings unique capabilities to the table, ensuring the success of this breakthrough initiative. Within the global supply chain through cross-industry collaboration, Indorama Ventures the world’s largest producer and recycler of PET, took bio-paraxylene to create terephthalic acid, then reacted it with monoethylene glycol to produce PET resin.
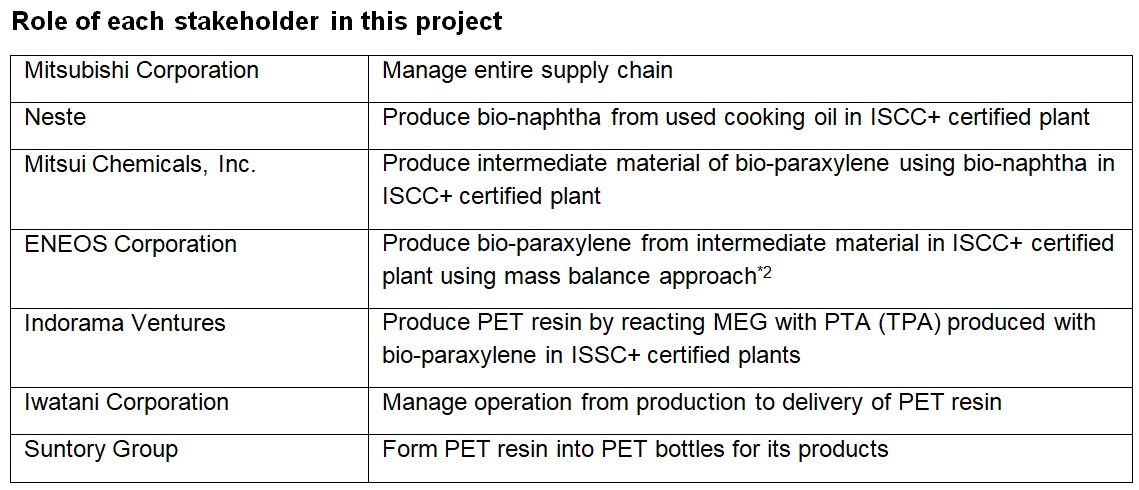
This launch represents a major step forward in reducing the environmental footprint of PET production. The mass balance approach applied throughout the production process ensures that the bio-based materials are transparently and effectively integrated into the PET bottles.
As a partner in this initiative, Indorama Ventures says it “remains committed to fostering a circular economy for the future of packaging through various avenues. The production of bio-PET resin aligns with Indorama Ventures’ long-term sustainability strategy and strengthens its commitment to providing environmentally responsible solutions to its customers.”
Subscribe to Get the Latest Updates from IMA Please click here
©2024 Injection Moulding Asia. All rights reserved.