Green tie-ups: Covestro/Ausell to advance end-of-life automotive recycling; Toray/PTT Global Chemical to explore biomass-derived nylon
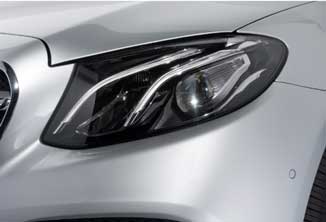
German materials firm Covestro has announced an enhanced collaboration with Chinese plastics recycling company Ausell. Building on their previous partnership in recycling polycarbonate water barrels, this new collaboration aims to accelerate the recycling of plastics from end-of-life vehicles.
Since 2020, Covestro has been partnering with Ausell to recycle 1 million/year 19-liter polycarbonate water barrels, converting them into high-performance post-consumer recycled (PCR) polycarbonates for various industries such as electronics, home appliances and automotive.
With this strengthened collaboration, Ausell will supply recycled polycarbonates derived from discarded automotive headlamps, which Covestro will then process into high-quality PCR materials for automotive engineering applications.
Lily Wang, Global Head of the Engineering Plastics Business Entity at Covestro, said: “We are excited to deepen our partnership with Ausell as we work closely with our value chain partners to accelerate the circular transformation of the automotive industry. Together, we are committed to pioneering sustainable solutions that will lead the way toward a circular and climate-neutral future.”
Xia Wenjun, CEO of Ausell, added: “Our enhanced collaboration with Covestro represents a significant step toward achieving our shared vision of a circular economy. By turning end-of-life automotive components into valuable resources, we are not only reducing waste but also contributing to the development of sustainable materials for future vehicle production.”
The automotive industry, facing increasing regulatory pressures for sustainability, as well as following their own roadmap to “close the loop” of materials, is looking for robust and adapted solutions to their challenges.
The recycled polycarbonates will not only enhance the sustainability of automotive components but also demonstrate the potential for high-value recycling solutions, the firms say.
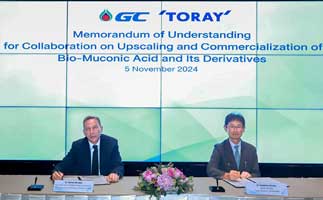
In other news, Japan’s Toray Industries has signed a memorandum of understanding with major Thai petrochemicals producer PTT Global Chemical Public Company Limited (GC) to explore mass production technology for adipic acid made from non-edible biomass*1.
Toray and GC will jointly evaluate the feasibility of mass production technology and commercialisation in Thailand and Japan. If business is determined viable, they aim to commercially manufacture several thousand metric tonnes of bio-based muconic and bio-based adipic acid annually by 2030.
Last year, both companies began jointly developing technology to produce these raw materials for nylon-6,6 from non-edible biomass-derived sugars made at Cellulosic Biomass Technology Co Ltd, a Thai company in which Toray has an 84% stake.
GC employs its proprietary fermentation technology to quickly convert non-edible sugars into high yields of muconic acid. Toray uses its hydrogenation process to produce high yields of high-purity bio-adipic acid from muconic acid.
The resulting bio-based adipic acid can serve as a raw material for nylon-6,6 for resins and fibres similar to the petroleum-derived nylon-6,6. On top of that, the manufacturing process does not generate nitrous oxide, a greenhouse gas by-product typically associated with chemical synthesis-based processes.
Toray and GC will build a supply chain to manufacture tens of thousands of metric tonnes of bio-based adipic acid from agricultural waste in Thailand, which is rich in natural resources. They will use this acid to make eco-friendly nylon-6,6, assisting efforts to create a circular economy and lower greenhouse gas emissions.
Subscribe to Get the Latest Updates from IMA Please click here
©2024 Injection Moulding Asia. All rights reserved.