Country Focus: Taiwan; Asia’s catalyst for manufacturing innovation
Taiwan’s technological assets establish the country as a vital player in the region’s sustainability transition, says Angelica Buan in this report based on the recently concluded Taipeiplas show in Taiwan in September.
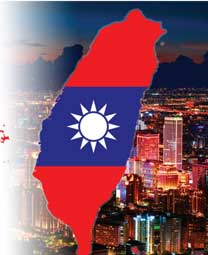
Taiwan, often referred to as the “Silicon Valley of Asia”, produces 90% of the world’s most advanced chips, powering industries globally—from consumer electronics to automotive. But Taiwan is not stopping at technology; it is also emerging as a hub for sustainable manufacturing, with ambitious goals for netzero emissions and greener solutions.
The Asia Silicon Vall ey Development Plan aims to transform Taiwan from a traditional manufacturing base into an innovative startup destination. This initiative encourages achieving net-zero carbon emissions by 2050.
Taiwan harnesses its technological prowess to advance eco-friendly manufacturing. Companies are adopting energyefficient processes, cutting emissions, and producing smart machinery, thereby setting a new standard for industrial growth.
Along the same vein, machinery makers are taking the lead. Several Taiwanese companies are already deeply invested in sustainable practices, with long-term strategies in place.
PRA recently interviewed three major players in Taiwan’s machinery sector, all of whom are offering global customers advanced, sustainable, and cost-effective solutions to meet the growing demand for environmentally compliant technologies. These homegrown companies are ready to take the global market by storm.
Yi Tzung: A legacy of continuing innovation in rubber machinery
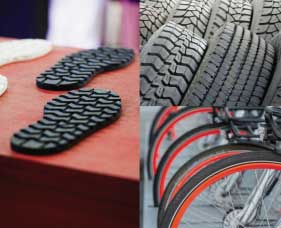
Weilin Liu, the fourth-generation head of Yi Tzung Precision Machinery Corp, is a Certified Machinery Safety Expert (CSME) and Executive Assistant to the President. Liu drives the company’s innovative direction.
Established in 1946, Yi Tzung has deep roots in the manufacturing of rubber and plastics machinery, with Liu noting that it is Taiwan’s oldest rubber machinery brand.
Highlighting the durability of the machines, Liu shared an anecdote about a customer who inherited Yi Tzung machines from his grandparent, and that are still in mint condition. “Stories like this prove that Yi Tzung machines can last for decades. It is not uncommon for our machines to be in use for 20 years or more!” Liu remarked.
Yi Tzung specialises in major mechanical processes, including rubber and EVA (ethylene-vinyl acetate) material from mixing, kneading, calendaring, coating, sheeting, and cooling, with applications ranging from automotive and bicycle tyres to shoe soles, silicone rubber products, medical items, and industrial rubber goods. The diverse product line includes over 20 different machines, and the company’s global sales network. Yi Tzung also operates its own casting factory.
Best in class solutions
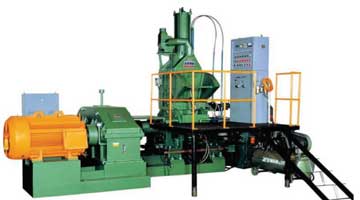
At the exhibition, Liu highlighted that one of Yi Tzung’s best sellers is the intensive mixer, specifically designed for mixing compounds and various plastics. The machine features a robust structure, including a main air cylinder, floating weight, feeding door, mixing chamber, rotors, and discharge device.
A key feature is its method of mixing: during compounding, materials and ingredients are simultaneously fed into the mixing chamber, where they are repeatedly sheared and squeezed by the rotors. This process facilitates a series of chemical interactions, enabling the material to coalesce into a paste-like mass. Mixing operations are conducted according to preset temperature and conditions.
This specially designed mixing machine provides efficient mixing and refining for a wide range of raw materials, including raw rubber, resins, asphalt, cellulose, PVC, and EVA. It offers several advantages, such as a short mixing time, high efficiency, ease of operation, an advanced cooling system, mixing performance, effective dispersion, and no material leakage, ensuring a clean working environment.
Other technologies offered by Yi Tzung include the HD dispersion kneader, designed for processing single or multiple raw materials, such as natural rubber, synthetic rubber, plastic, and more. This model boasts a sturdy construction, large mixing capacity and high speed, complemented by fully automated temperature control, a simplified operating process, labour savings, and stable product quality.
The rear input and front output design facilitate smooth production flow, while the back window allows for easy observation of mixing conditions. Its sealed mixing chamber ensures safe operation and addresses environmental pollution concerns.
Additionally, the mixing chamber features a 135-degree dumping inclination, simplifying the removal and replacement of colouring ingredients.
The machine is easy to install and is characterised by its durability, low failure rate, and straightforward maintenance.
Another top-tier offering from Yi Tzung is the intermesh dispersion kneader mixer for rubber and plastic, which features a unique engage-type rotor designed for mixing and kneading compounds with varying characteristics. Notable features include a rapid mixing time of 3 to 8 minutes per batch (depending on material characteristics, feeding time, and cleaning time), an accurate temperature control system, and an efficient cooling system. Its sturdy construction eliminates shaking during the mixing process, and the pressure lid, driven by an oil hydraulic system, can be adjusted to reduce energy consumption, making it suitable for various composite materials.
These machines serve as a cornerstone for a myriad of industries such as tyres, footwear and more that benefit the company’s customers in Southeast Asia, which Liu described as “our largest market,” along with India, Romania, Germany, and over 62 other countries.
Most importantly, these machines are homegrown. “They are locally made in Taiwan, and Yi Tzung has its own casting factory. Over 70% of the machinery is produced in-house, while only certain critical components are outsourced to ensure quality,” Liu added.
Liu intoned that major brands in tyres—ranging from automotive and bicycle brands to sportswear, footwear, medical devices, and electronics—are among Yi Tzung’s customers.
Smart manufacturing
One of Yi Tzung’s pivotal focuses is advancing small-scale manufacturing by transitioning to smart systems. Liu provided an example, explaining that in traditional rubber manufacturing, such as tyre production, equipment used to require manual recording of processing status and product quality checks.
“This process was time-consuming and demanded the presence of an on-site technician or engineer,” he said. Today, however, machinery can be integrated with sensors and linked to industrial computers, creating an API (application programming interface) system. This shift reflects the growing importance of data-driven technology, allowing customers to collect and organise data into actionable information for better analysis of settings like rotor speed, temperature, and pressure.
The system provides standardised data for quality checks and remote monitoring. “The future is moving toward smart manufacturing, incorporating automated functions for more efficient production processes,” Liu added.
Subscribe to Get the Latest Updates from IMA Please click here
©2024 Injection Moulding Asia. All rights reserved.