Battery funds: Entek secures US$1 bn DOE loan for lithium ion facility; Neo to partner in US$14 mn recycled silicon battery project by South Korean govt
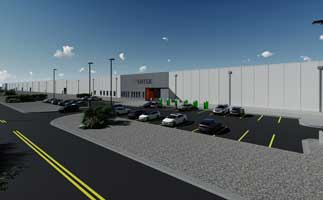
US-based producer of ‘wet-process’ lithium-ion battery separator materials Entek has announced that it has received a direct loan of up to US$1.2 billion to Entek Lithium Separators LLC from the US Department of Energy’s (DOE) Loan Programs Office (LPO).
It says the loan will “substantially” finance the new facility in Terre Haute, Indiana, to manufacture lithium-ion battery separators to be used primarily in electric vehicles (EVs). This project will strengthen and onshore the lithium-ion battery cell supply chain, enabling the creation of batteries used in advanced technology vehicles.
A battery separator is a microporous membrane sandwiched between the anode and cathode of a battery. The principal functions of the battery separator are to prevent electronic conduction (i.e., shorts or direct contact) between the anode and cathode while permitting ionic conduction via the electrolyte. Separators play an essential role in the performance and safety of lithium-ion batteries. Entek manufactures both ceramic coated and uncoated separators.
“Entek is a technology company at its core with expertise in equipment design and fabrication, process technologies, and materials science,” stated Entek CTO Richard Pekala, “These competencies make Entek the right company to lead the U.S. expansion of separator component manufacturing.”
The company adds it will be able to customize battery separators to accommodate numerous EV battery designs. The separators produced will be able to accommodate all existing lithium-ion EV battery chemistries, including NMC, NCA, LMFP, and LFP. Additionally, it will be able to sell its separators to manufacturers of lithium-ion batteries for energy storage applications.
Entek says it aims to become US’s first end-to-end, domestic supplier of “wet process” battery separators for the North American lithium-ion EV battery market. The project will make a significant contribution to domestic separator capacity and help US EV battery manufacturers satisfy the Inflation Reduction Act’s domestic content rules under the 30D Clean Vehicle Credit.
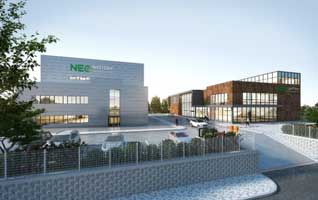
In other news, South Korea has established a consortium to run a recycled silicon battery materials project worth US$14 million. Neo Battery Materials, a low-cost silicon anode materials developer that enables longer-running, rapid-charging lithium-ion batteries, announced that the company has been awarded as a consortium partner along with major battery value chain companies and universities by the South Korean Ministry of Trade, Industry, and Energy.
"The project will focus on developing high-performance silicon anode materials based on recycled silicon scrap from semiconductor and photovoltaic wafer manufacturing," the Canadian battery materials technology company said.
Neo will act as a downstream value chain participant. Using recycled silicon inputs optimised with low-cost technologies, it will jointly develop silicon anode materials with consortium partners to manufacture high-content silicon anode batteries.
With Hansol Chemical, a South Korean chemical materials company, as the head project organisation, several major battery and chemicals companies are participating as consortium partners, including South Korea’s largest cathode materials producer, INNOX eco-M (Neo’s recycled silicon collaborator), and LiBEST.
Neo said the South Korean Ministry of Trade, Industry, and Energy (MOTIE) and the Korea Evaluation Institute of Industrial Technology (KEIT) will invest the stated amount "in government contributions for the next five years in consortium partners."
In June, Neo and INNOX eco-M signed a collaboration agreement to jointly develop silicon anode products by integrating INNOX eco-M's high-purity recycled silicon and silicon-oxide powders as the raw material.
Silicon anode materials are seen as next-generation materials capable of increasing energy density by about four times compared with graphite anodes typically used in lithium-ion batteries.
Neo's participation in the South Korean project comes after it signed a memorandum of understanding with Linde Korea Co Ltd on recently to scale up its silicon anode manufacturing for lithium-ion batteries.
Neo operates an R&D scale-up centre at Gyeonggi Technopark in Ansan Science Valley, South Korea.
Subscribe to Get the Latest Updates from IMA Please click here
©2024 Injection Moulding Asia. All rights reserved.