3D printing updates: BASF to build capacity for catalyst shaping technology in Germany; Research shows biobased resins offer recyclable future for 3D printing
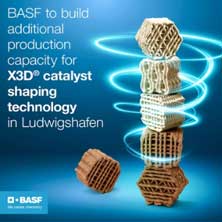
German chemicals firm BASF announced that it will invest in additional production capacity for its X3D technology, a new additive manufacturing technology for catalysts based on 3D printing. The plant will produce catalysts on an industrial scale and is expected to be operational in 2026.
The X3D technology represents a transformative leap in catalyst design and production. Catalysts produced using this technology are not only mechanically robust but also feature an open structure, which significantly reduces pressure drop across reactors and increases surface area. These advancements translate into improved catalyst performance, helping customers to achieve greater efficiency in their plants. They can benefit from an increased reactor output, higher product quality and a lower energy consumption, contributing to the customer’s green transformation goals.
One of the key benefits of the X3D technology is its versatility. It can be applied to a wide array of catalytic materials, including both precious and non-precious metal catalysts, as well as carriers. This flexibility allows BASF to customise catalysts according to specific customer requirements by fine-tuning parameters such as infill patterns, fibre diameters, and orientations.
“BASF remains committed to leading the charge in innovation within the chemical catalysts industry. X3D represents a step-change advancement in technology for catalyst production. We are proud to give our customers new opportunities to boost the performance of their production and at the same time reduce their carbon footprint,” said Detlef Ruff, Senior Vice President, process catalysts at BASF.
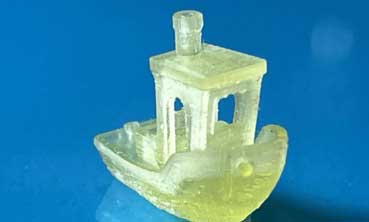
Meanwhile in other news, researchers from the University of Birmingham, UK, have designed a new type of photocurable resin, that offers two key benefits over existing 3D printing resins: it is made entirely from bio-sourced materials, and can be 3D printed, recycled, and then printed again.
While current 3D printing usually relies on epoxies or acrylics, which come mostly from petrochemical feedstock, the new resin is made from lipoic acid, a naturally occurring fatty acid molecule that is 100% bio-sourced, and commonly sold as a dietary supplement.
Additionally, the recyclability of conventional resins is still limited, because they rely on irreversible bonds created when the resin cures (hardens), and this poses challenges when the material needs to be recycled.
In contrast, the resin designed by the Birmingham team can be printed, then broken back down to its constituent parts, recycled and reprinted, with the addition of just a small amount of photoinitiator to maintain the material’s curable properties, meaning 3D printed products can be recycled in an almost fully closed-loop system.
The new resin is compatible with light-initiated printing techniques such as DLP, SLA or by direct ink write, or InkJet printing, and provides high fidelity, with resolution down to 0.05mm.
The researchers who invented the resin were led by Professor Andrew Dove from Birmingham’s School of Chemistry.
They have shown the resin can complete two ‘recycles’, and anticipate further recycling is possible, meaning the material could be used in sustainable packaging, industries that do rapid prototyping, optical and electronic devices, construction and architecture, or fashion and jewellery.
University of Birmingham Enterprise has filed a patent application covering the composition of the resin, and its use in 3D printing, and is now seeking to licensing or co-development partners.
Subscribe to Get the Latest Updates from IMA Please click here
©2024 Injection Moulding Asia. All rights reserved.