Solvay & 9T Labs in tie-up for 3D mass composites manufacturing
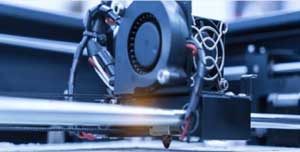
Materials firm Solvay is working with advanced manufacturing solution OEM 9T Labs AG (Zürich, Switzerland) to help bring additively manufactured carbon fibre-reinforced plastic (CFRP) parts to mass production.
The joint effort enables 9T Labs’ innovative additive manufacturing technology to produce low-to-medium volume size parts for the aerospace, medical, luxury/leisure, automation, and oil and gas industries. Solvay will focus on the development of carbon fiber-reinforced polyetheretherketone (CF/PEEK), CF-reinforced bio-based high performance polyamides and CF-reinforced polyphenylene sulphide (CF/PPS) composite materials. The partnership significantly expands the types of neat and carbon fiber-reinforced materials portfolio that 9T Labs currently offers to customers.
“With 9T Labs’ innovative process and equipment and Solvay’s high-performance thermoplastic materials, we are well positioned to address problems that have long plagued manufacturers in many industries trying to use advanced composites — namely high incremental costs, high scrap, and problems achieving repeatability and traceability at high volumes,” explains Marco Apostolo, director of technology at Solvay. “We believe this collaboration will help solve many challenges and will open entirely new markets and mass production applications to CFRP materials.”
Solvay offers a portfolio of high-performance thermoplastic polymers and expertise in the production of thermoplastic composite prepreg tape.
“For the fabrication of structural parts metals still prevail because the manufacturing of structural CFRP parts has not been cost-competitive,” adds Giovanni Cavolina, 9T Labs’ co-founder and chief commercial officer. “The Red Series platform in combination with Solvay’s high-performance and recyclable materials will change this and make CFRP parts more sustainable, accessible and cost-competitive, especially at higher volumes.”
9T Labs’ hybrid manufacturing technology enables high-performance structural parts — in challenging small-to-medium size and thick sections — to be produced in carbon fiber-reinforced thermoplastic composites in production volumes ranging from 100 to 10,000 parts/year. By combining 3D printing (which offers unexcelled design freedom, part complexity, and control of fiber orientation) with compression molding in matched metal dies (providing rapid cycle times, high production rates, excellent surface finishes with low voids, plus high repeatability and reproducibility (R&R), the hybrid production system offers the best of both additive and conventional / subtractive manufacturing.
(IMA)Subscribe to Get the Latest Updates from IMA Please click here
©2021 Injection Moulding Asia. All rights reserved.