R&D expansions: BASF opens facility in South Korea; Evonik enhances PU additives with German innovation centre
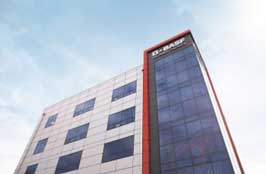
German materials firm BASF has opened a new Research & Development (R&D) facility at Ansan, Korea’s Engineering Plastics Innovation Centre (EPIC). The new facility houses the combined R&D team and competencies from its recent acquisition of Solvay’s polyamide business, other new competencies, as well as a Consumer Electronics Competency Centre (CECC).
Through the recent acquisition of the Solvay polyamide business, BASF enhanced its R&D capabilities in Asia Pacific. Its R&D capabilities in Korea include new technologies, technical expertise, and upgraded material and part testing services.
More material tests can be done in Korea, and covering a wide range of polymers, including polyamide (PA), Polybutylene terephthalate (PBT), and polyoxymethylene (POM). New test methods can be designed to better support customer projects. Product development capabilities for flame retardant and color grades have been upgraded to meet rigorous industry regulations and market demand driven by eMobility and E&E segments. With the reinforced Computational Fluid Dynamics simulation expertise, BASF can now support more projects linked to efficient cooling systems or reduction of overheating. As such, the enhanced technical skills and R&D capabilities expand BASF’s innovation competencies.
Housing the combined R&D team, competencies, and a new material evaluation team under one roof translate to greater efficiency & synergy – which better enables BASF to speed up and capitalize on the combined business when developing advanced customer-oriented products and applications. The synergy between new R&D team in Korea and R&D team in Shanghai will serve the markets around the Asia more efficiently.
The Consumer Electronics Competency Centre is said to be the first-of-its-kind competence centre that combines product development, quality control, testing, and Mixed Reality Experience – creating a one-stop advanced manufacturing ecosystem that helps Consumer Electronics brands and OEMs identify the right material solutions for their next innovation. The CECC is where companies can experience hands-on exposure to an advanced end-to-end material solution production supported by the CECCs ecosystem of partners and technology machines. It fills the gap between material solution R&D and commercialisation by letting companies carry out prototyping supported by on-site experts.
BASF adds it has also strengthened R&D capabilities for Ultraform POM. This includes a dedicated extruder for new product development also improves sampling time efficiency, and the set-up of a new research lab for upstream process and reinforced equipment for faster testing with better testing quality.
Ultraform is primarily used in consumer electronics, automotive, and medical devices, where many key players are located within APAC. It is highly rigid with good resilience properties, excellent chemical resistance, and sliding friction properties, making it ideal for tough applications.
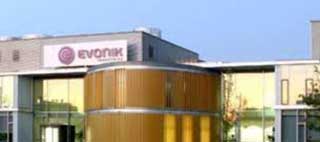
In other news, German materials firm Evonik has further expanded its position in the polyurethane (PU) industry with a new laboratory and innovation facility at its Essen Goldschmidt site in Germany, which was inaugurated at the end of October.
The new 400-sq-m laboratory will enhance the group’s development capabilities for high-performance specialty PU additives and processing aids for a variety of PU applications. The focus is on high-growth application areas such as the production of sustainable artificial leather, low emission catalysts for high-quality coatings and adhesives, performance additives for making PU shoe soles more durable and comfortable, and emission optimised release agents for moulded foams and elastomers.
“Our new laboratory and innovation centre sends a strong signal to the market and reinforces our strategy to not only be the leading, but also the most innovative, solutions provider to the PU industry,” said Ralph Marquardt, Head of Evonik's PU additives business. “This latest investment enables us to develop innovative and more sustainable additive solutions for our customers to help them meet changing market demands and increasing environmental regulations.”
Evonik's specialty additives and processing aids make, for example, the production of artificial leather more sustainable by replacing organic solvents with water in the production process. Another application area that Evonik’s PU experts are already working on in the new laboratory and innovation facility are environmentally friendly catalysts for polyurethane foams and materials with rubber-like properties (elastomers). They are used in the production of high-performance PU materials that protect electronic components in cell phones from vibrations or prevent the mechanical failure of electric car battery components during the charging and discharging process. Another example are additives and processing aids that extend the lifespan of PU shoe soles by improving the durability, appearance and wearing comfort.
"The new facility’s state-of-the-art equipment enables our team to work efficiently and safely on developing new additive solutions and bring them to market much quicker," said Matt Aldag, Head of Evonik’s Advanced PU business.
(IMA)Subscribe to Get the Latest Updates from IMA Please click here
©2021 Injection Moulding Asia. All rights reserved.