Machinery news: New machinery adds to personal touch
In an industry that thrives on personalised (rather than online) meetings, machinery makers at the recent Fakuma show, held in Friedrichshafen, Germany, were finally able to meet customers and partners face-to-face, after the past two years of no shows, and launch new machines, too.
Positive vibes from exhibitors
With exhibitions having been cancelled or postponed as a result of the Covid-19 pandemic, companies breathed a sigh relief at the recent Fakuma show. Christoph Schumacher, Director of Marketing at injection moulding machine maker Arburg, said, “Our expectations were more than met: the quality of the trade visitors and their interest in our exhibits and innovations was very high. Many decision-makers came to our stand to discuss specific projects.”
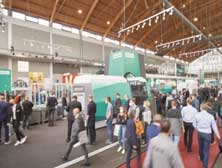
Meanwhile, compatriot company, Austrian machine maker Engel, also said Fakuma 2021 was a great success. Christoph Steger, CSO of the Engel Group, said, “The automotive industry has come back with a bang, and the investment backlog has cleared. Even if the Corona pandemic is still preventing some travel, Engel’s stand was well attended.“ He also said visitors came not only from the automotive industry, but also the medical technologies, packaging and technical moulding sectors.
Peter Kochs, Director Sales & Business Development, Europe, of Ferromatik Milacron, said, “Our team met in person with a significant number of injection moulding prospects as well as existing customers from Europe and abroad.“
Arburg displays variety of machinery and technology
Arburg had the largest trade fair stand and many new products on display, combining major topics of the future – digitalisation as well as sustainability and resource conservation in 2021 – with its declared aim of increasing customers’ production efficiency.
As is well known, the “arburgGREENworld” programme brings together all aspects of resource conservation and the circular economy. At its stand, Arburg used several applications to demonstrate how resources can be conserved and materials recycled. Examples included the processing of transparent biobased P 12, a bio-plastic consisting of 39% renewable raw materials based on castor oil. This material was used to create the well-known Uvex sunglasses on a turnkey system based on an Allrounder 520 A.
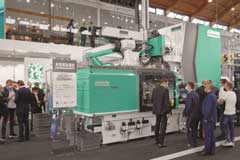
Post consumer recyclate (PCR) was used on an Allrounder 1300 T rotary table machine at the stand of Arburg’s partner, Lauffer.
In the case of recyclates, the sharply fluctuating quality of the material places high demands on injection moulding machines and injection moulding processes. To address this, Arburg has put together a new “recyclate package”, which premiered at Fakuma. The package includes various control functions and special plasticising features to enable recyclates to be processed reliably. The recyclate package is available for all Allrounders and can also be retrofitted to older models.
Just how sustainability and digitalisation interact was demonstrated by the “CurveCode” and “HolyGrail” marking technologies as innovative solutions for separating plastics by type and returning them to the materials cycle.
Arburg’s new Allrounder More machine series also made its first debut at an exhibition. The series covers the two sizes 1600 and 2000 and caters to multi- component injection moulding, with a flexible design to offer more space for larger moulds and ejectors, more modularity in its assembly, and ease of use via the Gestica control system. An Allrounder More 1600 produced a complex lab-on-a-chip for medical technology at the trade fair.
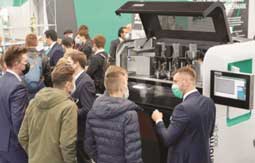
Other focal points were the Gestica control system and the planetary roller screw drive – both “made by Arburg” and benchmarks in the plastics industry. Arburg also highlighted its drive element, the planetary roller screw drive as an important part of the drive train, which is a central feature for the performance and durability of an injection moulding machine and accordingly a “seal of quality”.
Additive manufacturing also played an important role at Fakuma. A live presentation was given of the processing of high-temperature material Ultem on a freeformer 300-3X. In addition, a large number of components demonstrated the potential offered by Arburg Plastic Freeforming for the medical technology and automotive sectors, where Arburg is working on exciting projects together with partners and customers.
Also prominently represented on Arburg’s stand was sister company innovatiQ and its LiQ 320 printing system, which processes liquid silicone (LSR) using the LAM (liquid additive manufacturing) process.
Engel leveraging the full potential of its machines
At Engel’s stand, solutions for more sustainability in injection moulding and further digitalisation of production processes met with great interest, since “the two topics are closely linked”.
“Digitalisation is an important precursor to the circular economy,” said Steger. “Smart assistance systems and interconnected systems help us to leverage the full potential of injection moulding machines, for more efficient production while reducing the CO2 footprint.”
Compared to the last Fakuma, Engel’s stand was larger with additional space used to present digital products and solutions.
The Austrian firm presented a closed process chain for PP involving the production of mono-material food packaging using IML thin-wall technology and the production of protective covers from label offcuts.
At the same time, thee-speed 420 machine celebrated its world premiere. “Hybrid and all-electric injection moulding machines are seeing deployment in an increasing number of applications,” says Steger.
Demanding precision applications gave insights into the performance of the various hybrid and all-electric machine series.
In this regard, two machine exhibits that Engel presented on site in Friedrichshafen was the production of pipette tips on an all-electric e-mac and the manufacture of microcomponents from LSR on an all-electric and tiebar- less e-motion TL.
Moulders get first look at Milacron’s new eQ all-electric
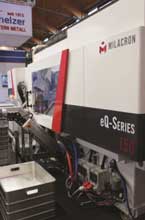
Germany’s Ferromatik Milacron announced a new addition to parent copany Milacron’s all-electric eQ -Series CE, now available to injection moulders across Europe at Fakuma. The new Milacron 150-tonne eQ-series injection moulding machine was displayed with a 24-cavity HDPE moulded cap application with a 2.7 cycle time.
The eQ series is a high-precision electric machine, which is said to combine accuracy and reliability across all processes. Optimised energy consumption through regenerative power recovery system stores energy during motor braking and allows up to 70% reduced melt stress.
The machinery supports additional specialised processes like thin wall moulding and multi-component moulding. This machinery line can be requested by moulders across Europe and Asia, said Milacron.
Some highlights of the machine are: screw diameter of 18-90 mm; maximum energy efficiency thanks to regenerative servo drive technology; low maintenance costs; series-standard overvoltage protection device; latest servo drive technology for increased efficiency throughout the entire injection process; improved kinematics of the toggle joint combined with steering of the closing force into the tool centre and latest Milacron control generation Mosaic G3.
(IMA)Subscribe to Get the Latest Updates from IMA Please click here
©2021 Injection Moulding Asia. All rights reserved.