Greening auto sector: Covestro recycles end-of-life headlamps for vehicle use; Hyundai’s EV3 car made with BASF’s sustainable solutions
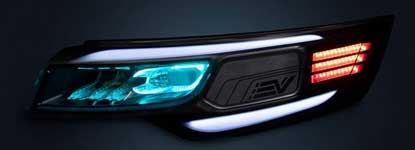
German materials manufacturer Covestro has introduced a new line of post-consumer recycled (PCR) polycarbonates made from end-of-life automotive headlamps, marking another milestone in closing the loop for automotive materials.
Developed through a joint program initiated by the German federal enterprise GIZ (Deutsche Gesellschaft für Internationale Zusammenarbeit), with Volkswagen and NIO as key partners, these TÜV Rheinland-certified grades contain 50% recycled content and are now commercially available for new automotive applications. Volkswagen and NIO are already validating the material for potential use in future vehicle designs.
Under this initiative, Covestro has been collaborating with partners, including Chinese recycler Ausell and automakers, to establish closed-loop pathways for high-value plastics from end-of-life vehicles (ELVs). This program focuses on strengthening recycling processes and establishing reliable supply chains for high-quality recycled materials from automotive waste streams.
Through this partnership, Covestro and its value chain allies have developed practical solutions for collecting and mechanically processing end-of-life headlamps into high-quality PCR grades suitable for a range of automotive applications.
"This partnership underscores the importance of cross-sector collaboration in driving the circular economy forward," said Martin Hansen, Regional Director of GIZ in East Asia. "By bringing together key industry players, we are not only creating viable solutions for recycling high-value plastics from end-of-life vehicles but also fostering innovation that supports a sustainable, closed-loop material flow in the automotive industry."
The introduction of these new PCR grades comes at a critical time as the automotive industry, one of the most resource-intensive sectors, faces increasing environmental challenges and regulatory pressures. The EU's End-of-Life Vehicle Directive, which sets recycling targets, along with China's Extended Producer Responsibility (EPR) program and growing sustainability requirements in key global markets, are pushing automotive manufacturers worldwide to seek innovative and sustainable material solutions that comply with evolving regulations.
Covestro adds its new PCR grades meet the standards required for demanding automotive applications, offering surface quality for aesthetics and adhering to strict Vehicle Interior Air Quality (VIAQ) requirements.
In recent years, the company says it has introduced PCR polycarbonates with up to 90% recycled content, and opened its first dedicated mechanical recycling compounding line for polycarbonates in Shanghai. Last year, it introduced a new range of polycarbonates based on chemically recycled, attributed material from post-consumer waste via mass balance for the first time.
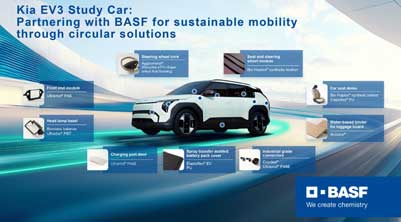
Along a similar vein, Hyundai-Kia and German materials firm BASF have once again co-created the third concept car - the Kia EV3 Study Car, an experimental model developed together with Hyundai-Kia’s R&D division.
The Kia EV3 Study Car features eight sustainable materials from BASF in various parts and components of the car. These material solutions include Ccycled & Biomass Balance (BMB) Engineering Plastics (Ultramid and Ultradur), Bio-based, Ccycled Polyurethanes (Elastoflex), Polyisocyanurate (PIR) Infinergy (E-TPU) in Super Critical Foaming (SCF), Bio PU synthetic leather (Haptex), and water-based binder (Acrodur).
“We are delighted for the opportunity to work with Hyundai-Kia Group again for what is now our 3rd concept car*,” said Andy Postlethwaite, Senior Vice President, Performance Materials Asia Pacific. “This project exemplifies BASF’s ongoing efforts to support the automotive industry’s transition to more sustainable practices and to provide innovative solutions that meet the evolving needs of consumers and manufacturers alike.”
Subscribe to Get the Latest Updates from IMA Please click here
©2025 Injection Moulding Asia. All rights reserved.