StackTeck sets up iMFLUX for processing recycled materials
Injection moulding solutions provider StackTeck Systems Ltd is introducing services in support of adoption of the iMFLUX process in an effort to help customers overcome the challenges of moulding recycled materials. StackTeck has embraced the iMFLUX technology as a process control method that is capable to handle large and sudden material property variations in real time.
The iMFLUX process is a patented technology, belonging to Procter & Gamble, which utilises a closed loop control system to manage injection pressure during every moulding cycle based on real time measurement of the molten plastic in front of the screw in an injection moulding machine.
Pressure measurements are taken at a frequency of 1,000 hertz, and the control system manages the system to maintain a constant injection pressure, regardless of the potential for pressure variations that are caused by material property changes over time.
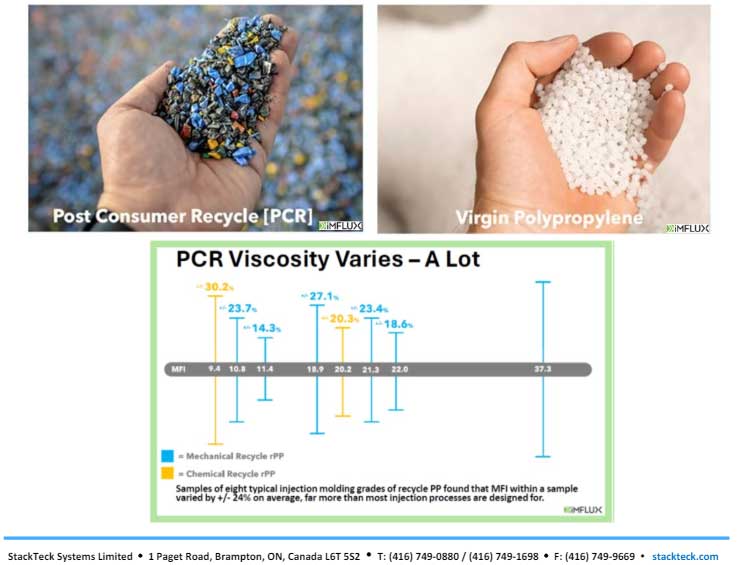
Following the success of using this patented technology to qualify a range of PCR resin grades, StackTeck has received permission from Procter & Gamble to use and share this know-how that can be used for any iMFLUX capable injection moulding machine.
PCR Challenges (and Solutions):
- High degree of variability in Melt Flow Index (MFI) ==> Injection moulding process control (iMFLUX)
- Increased demands on balance and precision ==> Injection mould custom features
- Contaminants and impurities ==> Injection mould design for wear and cleaning
- Process and quality monitoring requirement ==> System control sensors and process control
Jordan Robertson, Vice President Business Development and Marketing at StackTeck, stated: “We are very excited to be in a position to share this capability with all players in the industry. The first time I saw the Automatic Viscosity Adjustment capability of iMFLUX, we did a material change from 40 MFI to 5 MFI polypropylene while running a big mould in one of our test machines. The iMFLUX controller adapted smoothly and flawlessly, we didn’t see a short part - the machine kept running as if nothing had changed at all. Based on many years working with PCR resins for thinwall PCR horticultural products, the power of this technology was immediately evident.”
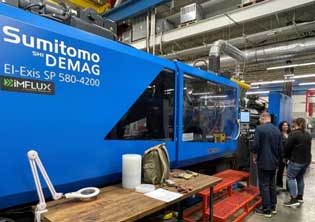
StackTeck President/CEO, Vince Travaglini expects PCR applications growing from a few moulds per year to a substantial proportion of the projects the company is handling. “As a result, we are working to adapt our mold test machines and qualification procedures to suit PCR projects, while also preparing to handle more projects for PCR resin qualifications. We see this as a strategically important step towards helping our customers move to more sustainable products,” he added.
Material property fluctuations have significant implications for the moulding process. As illustrated in the chart below, changes in resin between 30 MFI and 70 MFI result in injection pressure variations that lead to significant quality and efficiency issues in conventional injection molding systems. Per the chart below, such MFI swings can result in injection pressure changes as large as 20%, which can literally stall the cycle, or create scrap.
The company says using iMFLUX low constant pressure combined with "Auto Viscosity Adjust" (AVA) allows:
- Adapts in real time to material property variations by adjusting pressure
- Controls dramatic variations in resin viscosity
- Process changes are monitored and recorded
- Used in concert with Scientific Molding approach for consistent part quality
- Significant productivity boost for PCR applications
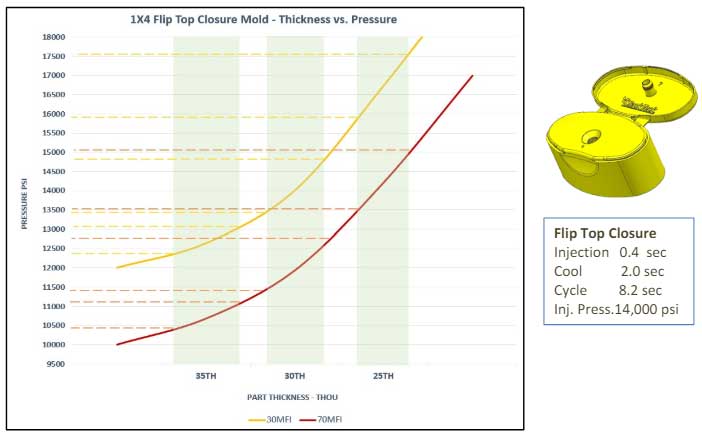
StackTeck has adopted the iMFLUX process to control the injection moulding process for PCR projects that bring material viscosity challenges. StackTeck also works with industry leading partners including RJG, Trexel, and the top tier machinery suppliers to offer the most advanced molding process capability that is available in the industry.
(IMA)Subscribe to Get the Latest Updates from IMA Please click here
©2024 Injection Moulding Asia. All rights reserved.