Green tie-ups: Yanfeng/Trinseo to collaborate on mechanical recycling; Consortium develops recycling for end-of-life PU mattress foams
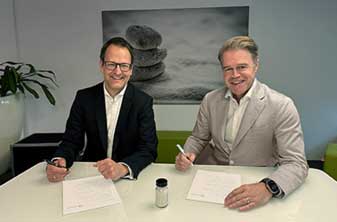
China’s automotive parts supplier Yanfeng, and Trinseo, a specialty material solutions provider, have announced their collaboration in developing circular automotive interior materials. Both partners intend to design and deliver interior materials which meet the 2030 End-of-life-vehicle requirements and OEMs' ambitions with regard to the circular economy targets.
The partnership between Yanfeng and Trinseo aims to accelerate the market launch of circular materials for automotive interiors. It focuses on advanced mechanical recycling and dissolution process technology. Both partners intend to jointly develop, produce and commercialise circular materials for future automotive applications.
“By leveraging our extensive knowledge with Trinseo's technical expertise, we accelerate the development of circular automotive materials and offer our customers benefits along the entire value chain. Together we can provide recycled, high-quality solutions tailored to the automakers’ needs," said Gunnar Büchter, Vice President of Global Sustainability at Yanfeng. “This new partnership is a major step in our commitment to sustainability and part of the journey in realizing our company’s sustainability goals.”
“Trinseo and Yanfeng are a perfect fit. With Yanfeng we can expand and leverage our circular and low carbon solutions for all automotive customers and markets,” said Han Hendriks, Chief Technology Officer at Trinseo.
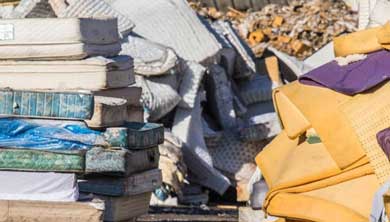
In other news, French company Ecomaison has dedicated itself to collecting and recycling used furniture and has been working with German materials firm Covestro for a few years to utilise its chemical recycling technology for this purpose. With this advanced process, both raw materials originally used can be recovered – the polyol as well as the precursor to the isocyanate TDI.
The aim of the partners is to recycle the sorted polyurethane foams as efficiently as possible by combining mechanical and chemical technologies after careful sorting by foam type in the mattress cutting plants.
Collaborations leveraging own expertises with like-minded partners are key: In addition to Ecomaison and Covestro, the French dismantling company Secondly and Federal Eco Foam, a Belgian specialist in the mechanical recycling of flexible foams, are involved as partners in the project, which is planned to run for a maximum of 24 months. The project is called Foam Recycling Ecosystem Evolution (FREE) and coordinated by Covestro and half-funded by Ecomaison.
For the FREE consortium, the motivation lies in the added value of the material that can be recovered from the used foams and the opportunity to enter a more sustainable circular economy. The partners want to explore all possibilities in a future-oriented foam recycling ecosystem and are convinced that chemical and mechanical recycling will complement each other in a meaningful way. As dismantler and sorting actor, Secondly is interested in empowering its sorting processes to be able to supply to recyclers a specified quality of foam.
At the same time, the project will provide a good picture of how the foam recycling market in the coming years may look like. The partners truly believe that chemical and mechanical recycling can be complementary given different specifications of inlet materials being sorted already at dismantlers. To provide added value to the PU foam material, the consortium will investigate all possibilities in a future oriented eco-system of foam recycling.
The research and development project includes the foam sorting at the dismantling step, as well as a comparative feasibility study for two recycling processes for the sorted foams covering economic and ecologic value co-creation.
A few years ago, Covestro and its partners developed a chemical recycling process that is the only one of its kind capable of ultimately recovering both main raw materials of flexible PU foams in high purity. The company also operates a pilot plant at the Leverkusen site for this purpose. Together with the waste management industry, the company wants to drive the process forward to industrial use.
To make its vision of a fully circular economy a reality, Covestro is making the development of innovative recycling technologies a priority and calls the evolution of recycling Evocycle CQ. The chemolysis of PU mattress foam is the first initiative of Covestro of its kind and is called Evocycle CQ Mattress.
Subscribe to Get the Latest Updates from IMA Please click here
©2024 Injection Moulding Asia. All rights reserved.