R&D centres: Ford invests US$185 mn in EV battery centre; BASF breaks ground on 3rd phase of Chinese centre
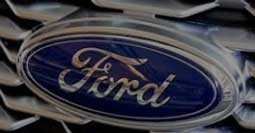
Automotive company Ford is setting up a US$185 million technical centre dedicated to the development, testing and manufacture of battery cells that will open in 2022. Known as Ford Ion Park, it will be in Southeast Michigan on a site that will be selected soon and have a dedicated staff of 150. Due to open in late 2022, it will serve as a centre for battery expertise for Ford operations worldwide and build on the automaker’s experience in building 1 million electrified vehicles since 2005, according to Hau Thai-Tang, Ford Chief Product Platform and Operations Officer.
“We’re already scaling production of all-electric vehicles around the world as more customers experience and crave the fun-to-drive benefits of electric vehicles,” he notes. “Investing in more battery R&D ultimately will help us speed the process to deliver more, even better, lower cost EVs to customers over time.”
By centralizing cross-functional teams of experts in battery technology development, research, manufacturing, planning, purchasing, quality and finance, Ford can more quickly develop and manufacture battery cells and batteries, Thai-Tang adds.
The Ion Park team also will explore better integration and innovation opportunities throughout the value chain – from mines to recycling – by working with all teams within Ford, including staff at the automaker’s Battery Benchmarking and Test Laboratory in Allen Park, MI, which was completed in 2020.
Researchers at the US$100 million, 17,200-sq-m test centre have already analysed more than 150 types of battery cells.
The lab houses battery cell and pack test rooms, test benches and benchmarking facilities to support battery cell design validation, controls calibration, pack development and pilot battery pack projects with different chemistries. The lab team can replicate the performance of full-scale production batteries under extreme weather and customer use cases, speeding implementation in future vehicles.
Thai-Tang says, “We are modernising Ford’s battery development and manufacturing capabilities so we can better control costs and production variables in-house and scale production around the world with speed and quality.”
Thai-Tang says Ford is moving toward vertically integrating battery production into the company’s operations. The current disruption of the semiconductor supply chain has put added focus on the automaker’s need to have tighter control over the supplies of battery cells in the future, he says.
However, Ford is not yet prepared to announce any plans for building a battery cell manufacturing plant.
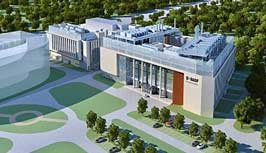
In other news, German chemical firm BASF is strengthening its innovation capabilities in Asia by breaking ground for the third phase of its Innovation Campus Shanghai and by establishing an academic sounding board as part of the Network for Asian Open Research (NAO). The expansion includes an additional R&D building and one R&D workshop building. Construction is expected to be completed by the end of 2022; by then, the total investment of BASF into its Innovation Campus Shanghai will sum up to around EUR280 million.
BASF says this shows its continued commitment to further build up innovation capacities in China and the whole Asia Pacific region. With this expansion, it will strengthen its R&D capabilities for advanced materials and systems as well as for chemical engineering in order to serve the needs of growing industries, such as automotive, construction, and coatings.
Accompanying this expansion at the Innovation Campus Shanghai, BASF is establishing a sounding board made up of experts from top universities in Asia as part of the Network for Asian Open Research (NAO). The sounding board will strengthen BASF’s innovation pipelines and accelerate market introduction by providing professional consultancy for R&D projects, anticipating industry trends, and enhancing the collaborations between BASF and universities.
Launched in 2014, NAO is a joint platform of BASF and meanwhile 12 prestigious universities and institutes in Asia Pacific. To date, more than 70 joint projects have been completed, covering a wide range of research areas including monomers, polymers, surfaces and interfaces, coatings, catalysis, battery materials, chemical and process engineering, insecticides, as well as digitalisation and smart manufacturing in R&D.
The Innovation Campus Shanghai has become an innovation powerhouse for BASF and its partners. Over the past five years, the Innovation Campus Shanghai has applied for more than 220 patents. The site plays an increasing role in the development of innovations for the automotive, construction and consumer goods industries.
(IMA)Subscribe to Get the Latest Updates from IMA Please click here
©2021 Injection Moulding Asia. All rights reserved.