Expansions: BASF starts up its first plant for recycled PA6; Covestro to open laboratory for coating and adhesive formulations
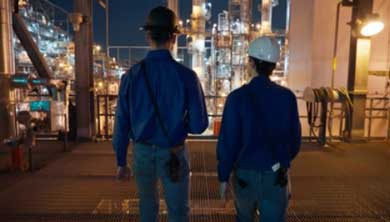
German chemicals firm BASF has announced the start-up of what it says is the world’s first commercial loopamid PA6 plant. The production facility at the Caojing site in Shanghai, China, has an annual capacity of 500 tonnes and is said to mark an important step in the supply of sustainable products for the textile industry. “
Loopamid is a recycled polyamide (PA) 6 that is entirely based on textile waste. The new production facility supports the growing demand for sustainable PA6 fibres in the textile industry.
The plant as well as the quantities of loopamid produced are certified according to the Global Recycled Standard (GRS). This certification guarantees to consumers and textile manufacturers that loopamid is made from recycled materials and that the production processes comply with specific environmental and social criteria. In addition, first yarn manufacturers are successfully using loopamid, it adds.
To produce loopamid in its new plant, BASF currently utilises industrial textile waste from textile manufacturing and will gradually increase the share of post-consumer waste. This feedstock includes cutting scraps, defective cuts, offcuts and other production textile waste from the textile industry. These materials are collected and provided to BASF by customers and partners. End-of-life garments made from PA6 and other textile products can also be utilised for the production of loopamid.
All these waste materials are challenging to recycle because they typically consist of a mixture of different fibres and materials as well as dyes and additives. Additionally, for post-consumer waste recycling, buttons, zippers and accessories must be removed in advance.
BASF adds that it works closely with partners and customers to accelerate the development of collection and sorting systems.
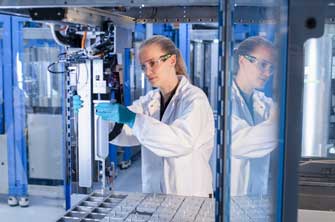
In other news, coating and adhesive manufacturers are under pressure: They compete for market share, optimise their products in rapid succession, and must focus on efficiency while ensuring sustainability and regulatory compliance. At the same time, products need to become increasingly circular – without compromising the properties of a coating or adhesive. A critical factor in all of this: The right binders and crosslinkers. Their development takes place at material manufacturers like Covestro. The German company is now addressing these requirements by announcing that in the course of 2025, it will open a specifically developed, automated laboratory for optimizing coating and adhesive formulations to provide better support to its customers.
"With our automated laboratory, we can work together with our customers on the future of coatings and adhesives. Because it operates almost completely autonomously and learns from our existing knowledge and data lake as well as newly generated data, it makes the process of optimising and developing formulations many times more efficient and precise. This allows us to optimise existing formulations faster or even develop completely new formulations for and together with our customers. We can say: We are reaching a new level of modern research," says Thomas Büsgen, head of the laboratory.
Specifically, the new laboratory will test formulations with Covestro binders and crosslinkers for coatings and adhesives. Their clever selection ensures properties such as hardness, adhesion, opacity, gloss, or durability. Such formulations typically consist of seven to 15 components, whose combination determines the properties of the final product. The resulting high number of possible combinations means that standard formulations are usually used. The new laboratory now enables more extensive test series, also thanks to the computer-aided design of test series and the use of automation.
Martin Merkens, Head of Sales & Market Development EMLA in Covestro's Coatings and Adhesives business entity, said, “This will particularly help us in the area of circular economy: Alternative raw materials, for example bio-based or recycled materials, can be tested faster and evaluated for their properties in the final product.”
The new facility can operate 24 hours a day, 7 days a week. The goal is to run tens of thousands of tests annually. This sets a new standard in terms of number, variety, precision, and testing speed. Another advantage: The automated laboratory generates a large amount of structured data. The knowledge about formulation possibilities and influencing factors thus will grow rapidly. The collected data, combined with measurement data from existing studies, is evaluated using special machine learning algorithms to further improve formulations. Artificial intelligence is also used to predict new experiments based on property goals and simultaneously verify them in the automated laboratory – creating a self-learning system.
In addition to formulating water- and solvent-based 1K and 2K systems, the automated laboratory also performs numerous material tests on the raw materials themselves, their formulations, and applied films. Application can even take place in different climates in the lab to simulate product use under application conditions. The progressing laboratory digitalization across Covestro also enables easy forwarding of generated samples to more specialized testing laboratories. This makes it possible to supplement the datasets with market-specific test results and identify relevant dependencies more quickly.
Subscribe to Get the Latest Updates from IMA Please click here
©2025 Injection Moulding Asia. All rights reserved.