Plants: Mitsui Chemicals to cut TDI capacity in Japan; Sulzer starts up world’s largest pygas-to-styrene extraction unit in China
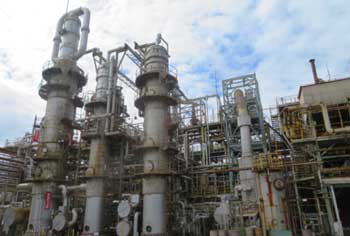
Japan’s Mitsui Chemicals says it is cutting the production capacity of its toluene diisocyanate (TDI) plant at Omuta, Japan, to 50,000 tonnes/year from 120,000 tonnes/year currently, in July 2025.
It adds that “while maintaining a stable supply setup to meet domestic demand for TDI, the Omuta Works will contribute to expansion in growth domains as part of Mitsui Chemicals’ business portfolio transformation by bolstering competitiveness as the company’s principal centre for the manufacture of high-performance products, including ophthalmic lens materials and agrochemical products”.
Mitsui Chemicals adds that it has positioned polyurethane (PU) as one of several businesses in its materials business sector that would be subject to restructuring.
In addition to the forthcoming optimisation of TDI production capacity, the restructure will encompass the development of high value-added products, including high-performance methylene diphenyl diisocyanate and high-performance polyols such as polypropylene glycol.
It adds that “pursuing these efforts will allow Mitsui Chemicals to reduce earnings volatility, improve capital investment efficiency and lay the business foundations for generating stable earnings”. Furthermore, it is looking at setting up a chemical recycling scheme for polyurethane foam and considering the use of ISCC PLUS-certified bio-based toluene produced at the Osaka Works to manufacture greener TDI.
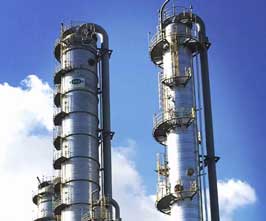
Meanwhile in other news, Sulzer Chemtech (GTC Technology) has completed the start-up of the world’s largest facility for styrene extraction from pyrolysis gasoline (pygas) derived from naphtha cracking. Located in Zhejiang Petroleum & Chemical Co.’s (ZPC) integrated refining and petrochemical complex in Zhoushan, China, the unit uses Sulzer Chemtech’s proprietary GT-Styrene licensed technology to produce 100,000 tonnes/year of styrene.
The new facility upgrades pygas, a by-product obtained from three steam crackers in Zhoushan’s plant, by extracting valuable styrene for use in the petrochemical industry. The process flexibility offered by GT-Styrene is enabling the plant to obtain high-quality ASTM 2827 grade styrene from three different units within a single train. This will help ZPC increase the overall profitability of its integrated refining and petrochemical complex.

ZPC selected Sulzer Chemtech due to its prior extensive experience in styrene extraction and positive outcome of previous collaborations.
Sulzer Chemtech supported all stages of the project, from delivering a licensed Basic Engineering Package, to supplying proprietary equipment and chemicals, providing support during the detailed engineering phase, and successfully completing commissioning and startup of the unit.
Zhang Shoumin, Director of Olefin Separation Department at ZPC, adds: “Sulzer Chemtech is a leading licensor with a proven track record of implementing advanced pygas styrene extraction technology. Hence, the company and its GT-Styrene were an obvious choice. We are impressed with the level of support received throughout all stages of the project as well as the technology’s ability to meet product specification soon after start-up.”
Sander van Donk, Head Clean Fuels & Chemicals Licensing at Sulzer Chemtech, concludes: “We are delighted to have played a key role in this ambitious project. This was a successful deployment of GT-Styrene for the world’s largest pygas-based styrene extraction plant and demonstrates our ability to scale up process technology while achieving demanding performance objectives.”
(IMA)Subscribe to Get the Latest Updates from IMA Please click here
©2023 Injection Moulding Asia. All rights reserved.