Green tie-ups: Stora Enso/Kolon collaborate on biobased polyesters; DSM Engineering Materials works with noho to biobased nylon furniture portfolio
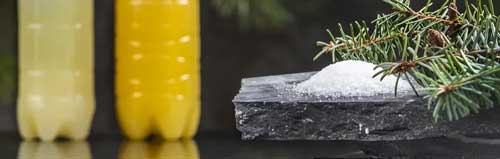
Renewable materials company Stora Enso and Kolon Industries have ties up to develop and industrialise biobased polyesters and their applications, as well as renewable binder resin formulations. Application areas can cover, for example, packaging, car tyre reinforcements, and films for high value-added products such as electronics, panels and displays.
The development work will combine FuraCore by Stora Enso – a proprietary process for converting fructose into FDCA (Furandicarboxylic acid) via HMF (5-hydroxymethylfurfural) – and Stora Enso’s expertise in the packaging industry with Kolon Industries’ expertise in polyester and phenolic resin development as well as manufacturing for a range of applications.
FDCA is an organic chemical compound that occurs in nature and is the key building block for bio-based plastics such as PEF (polyethylene furanoate). PEF holds great potential as a packaging material and for technical films where its attractive barrier properties open exciting opportunities. PEF may enable renewable textiles as well, offering consumers a more sustainable choice. HMF is the precursor to FDCA in the FuraCore® process. As a versatile specialty chemical, it adds renewability and performance to certain resin formulations.
“This partnership is significant in that it enables the solidification of the foundation for building a new bioplastics ecosystem. We will continue to accelerate the development of sustainable polymer technologies for a greener environment,” says Sung Han, CTO of Kolon Group.
“Together with Kolon Industries, we will be developing and validating commercially attractive formulations and applications based on FDCA-based polyesters and HMF-based resins. We look forward to partnering with a leader in the field for applying our elegant FuraCore technology,” says Johanna Hagelberg, Executive Vice President, Biomaterials Division at Stora Enso.
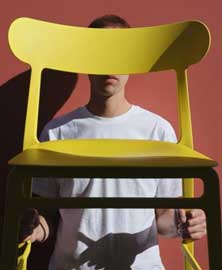
Meanwhile in other news, Dutch firm DSM Engineering Materials has announced the launch of its first collaboration with New Zealand-based direct-to-consumer furniture brand noho: Lightly stackable chairs. The new plant and recycled-based product is the first chair to be manufactured from DSM’s EcoPaXX biobased polyamide, which is derived from the castor bean plant.
This renewable resource is highly CO2 absorbent while it is growing, giving EcoPaXX a lower carbon footprint compared to fossil-based alternatives. Combining functional performance, optimal durability, and aesthetics with a significantly reduced environmental impact, EcoPaXX is facilitating noho’s goal of sustainability, according to the companies.
The launch of Lightly marks the second entry in noho’s portfolio of ergonomically designed and more sustainably produced chairs for work, home, and events. Lightly will be available to order in the US and New Zealand from March.
The chair is created using both EcoPaXX (~71%) and recycled post-consumer waste materials (~28%). EcoPaXX is 70% biobased, with its renewable content derived from castor bean plants. EcoPaXX biobased polyamides have a wide range of uses across industries such as automotive, water management, consumer goods and electronics, and food packaging.
Combining comfort and convenience, Lightly is designed to be light and easily stackable for simplified storage, mobility and versatility: one chair weighs only 2.7kg and a stack of 10 chairs reaches 106 cm from the ground – allowing users to easily tidy them away when not in use. This compactness also reduces the greenhouse gas (GHG) emissions related to shipping the products, as more chairs can be loaded into a single container.
Lightly’s thin frame is manufactured using as little material as possible to reduce GHG emissions related to raw material sourcing. This means the material used must meet demanding performance standards, and EcoPaXX is said to provide the ideal combination of strength, durability, low moisture uptake, and surface finish – resulting in a product that is as attractive and robust as it is sustainable.
(IMA)Subscribe to Get the Latest Updates from IMA Please click here
©2023 Injection Moulding Asia. All rights reserved.