Green materials: Mitsui Chemicals produces biomass PP; Qenos, Axens and Plastic Energy partner on chemical recycling
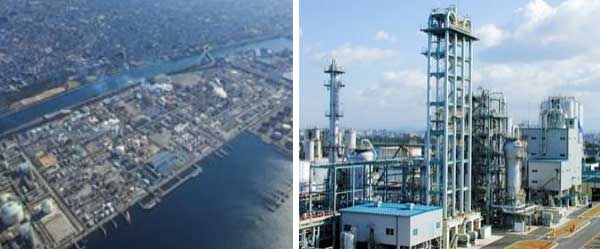
Japan’s Mitsui Chemicals says that its subsidiary Prime Polymer has become the first company in Japan to commercially produce and ship biomass polypropylene (PP). Mitsui Chemicals received the technology last year from sustainable tech firm Neste Corporation at its Osaka Works in Takaishi, Osaka.
Derived from bio-based hydrocarbons, this PP is certified as bio-based using the mass balance method in accordance with ISCC PLUS certification for plastic and chemical derivatives.
It adds that the group is working to realise a circular economy through the two-pronged approach of chemical recycling and conversion to bio-based materials. Aiding in the effort to circumvent global warming, bio-based production represents an avenue of strategic importance when it comes to achieving carbon neutrality by 2050.
In conjunction then with its development of materials and processes toward this end, Mitsui Chemicals aims to make this shipment of a bio-based hydrocarbon derivative the first step toward promoting the implementation of bio-based chemicals and plastics.
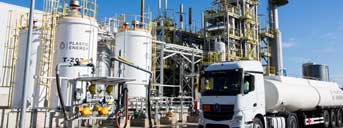
Meanwhile, Plastic Energy (UK), one of the world’s leading advanced plastics recycling technology companies, and Axens (France), worldwide provider of technologies, products and services, are partnering with Australia's only manufacturer of polyethylene and polymers Qenos in the planning of a major circular plastics manufacturing capability in Australia.
Plastic Energy, which specialises in advanced recycling of plastics using its Thermal Anaerobic Conversion (TAC) process and Axens, which has developed the Rewind Mix process will support the recently announced Qenos and Cleanaway joint feasibility study for the conversion of up to 100,000 tonnes of household soft plastic waste and mixed plastics back into Circular Polyethylene.
Circular plastics manufacturing using advanced recycling takes soft plastics and other hard-to-recycle plastic waste which currently goes to landfill, incineration or escapes into the environment and recycles this back into the same products. It is the next major phase in recycling, and is forecast to attract A$680 billion of investment globally by 2050.
Circular Polyethylene has identical properties to virgin polyethylene and can be used in food contact and high-performance applications thereby supporting local packaging and food manufacturers to achieve the 2025 APCO National Packaging Targets.
Qenos CEO, Stephen Bell, said that this important step in the development of the Qenos Circular Plastics Project (QCPP) was the result of an extensive assessment of suitable advanced recycling technologies and partners, supported in part by the Victorian Government.
The Australian Food & Grocery Council (AFGC) is developing the National Plastics Recycling Scheme (NPRS), which aims to collect and recycle nearly 190,000 tonnes/year of soft plastic packaging by 2025.
The QCPP is the largest proposed circular plastics project in Australia, and is currently being considered for support under the Federal Government’s Modern Manufacturing initiative.
The joint feasibility study is expected to be completed by July 2022 and a final investment decision to be made later this year. Pending a successful outcome, the first of the advanced recycling facilities is expected to be operational by 2025. Fully commissioned, the QCPP would secure a leadership role for the Australian manufacturing chain in this emerging global sector.
(IMA)Subscribe to Get the Latest Updates from IMA Please click here
©2022 Injection Moulding Asia. All rights reserved.