3D Printing/Additive Manufacturing: Market uptake, research abounds on new materials
Pandemic no deterrent to growth
Even with the Covid-19 pandemic, the 3D printing/additive manufacturing sector expanded by 7.5% to nearly US$12.8 billion in 2020. However, growth was down considerably, compared to average growth of 27.4% over the previous ten years, said consulting firm Wohlers Associates in its latest report on the industry sector.
Most established manufacturers of AM systems saw a decline in equipment sales, but many less-established companies grew in 2020. An increase in business by AM service providers supported industrywide growth. The chart shows 7.1% growth from independent service providers worldwide, resulting in nearly US$5.3 billion of revenue from this group.
The Wohlers Report 2021 also includes commentary on 74 early-stage investments and 35 acquisitions and public offerings. AM start-ups and established companies have received substantial funding in the recent past. One example is Desktop Metal, which received US$575 million as part of a merger with a special acquisitions company. After going public in December 2020, Desktop Metal’s market capitalisation exceeded US$7.5 billion in February 2021.
Cellulose-based materials for 3D printing of components
Cellulose is an ideal raw material for electrical insulation components, because it is clean and capable of resisting high temperatures, and it remains firm in oil used in transformers for both insulation and cooling purposes. However, the raw material must be packaged into the moulds manually, and a variety of different moulds are required. The process also consumes energy and produces plenty of waste. With the current methods, the value of production is approximately EUR 1 billion a year.
In the EU-funded Novum project coordinated by Finnish research company VTT, the focus is on developing automated methods for the production of cellulose-based electrical insulation components and for other applications such as the automotive industry and cruise ships.
The project, which started in October 2017, has been limited to the most promising manufacturing methods: 3D printing and foam forming since the former offers efficiency as well as new freedom in design while the latter saves energy in the manufacturing process.
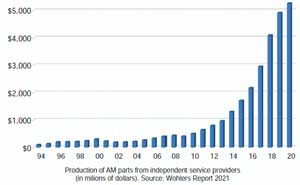
As the research group works on developing cellulosebased materials and the manufacturing methods, it also investigates which other applications could be potential for the combination, in addition to transformers. A good starting point for the applications is the need to produce individual products or small series easily or to replace plastic parts with renewable material.
The automated production line built in the project will be tested and validated with electrical insulation components and parts used in car and cruise ship interiors. The applications are of interest to Hitachi ABB Power Grids, manufacturer of electrical insulation components for its own transformers in Poland; Meyer Turku, a shipbuilding company and CRF, the research company of Fiat in Italy.
The Novum project also involves Brinter, developer of 3D printing technology in Finland, AGH University of Science and Technology in Poland, ABIS, an engineering company from Poland, JRS, supplier of renewable materials from Germany and Vertech Group, a sustainability expert from France.
VTT’s main focus in the project lies in material development since in order for cellulose to be 3D printable, it must be made thermoplastic, that is, pliable at an elevated temperature. Thermoplastic cellulose-based materials similar to oil-based plastics have previously been developed at VTT. However, for the Novum project, it is important that the cellulose-based material also contains pure cellulose as much as possible as this is essential for insulation materials.
In addition to modifying the material to ensure compatibility with the manufacturing process, the material’s properties, such as its strength and heat resistance, are also adjusted in accordance with the application requirements.
Irrespective of the exact composition of the material, VTT says it is already clear that the pieces produced can be ground and re-used as raw material on the same production line as many as eight times.
Composites material for 3D printers
US firm Stratasys has introduced an ABS-based carbonfibre material for its line of F123 Series 3D printers, said to be the first composite material for the printers. Carbon-fibre materials have been used on Stratasys’s industrial-scale FDM 3D printers for a variety of applications such as jigs, fixtures, and tooling. With FDM ABS-CF10, Stratasys says it is now making carbon fibre much more accessible to the engineering and manufacturing community with highperformance F170, F270, and F370 3D printers.

Featuring 10% carbon fibre, FDM ABS-CF10 is a welcomed alternative to metal parts, since it is also 15% stronger and more than 50% stiffer than standard ABS, without the weight of metal, and can be printed with a high degree of accuracy. QSR Support water-soluble material makes it possible to 3D print intricate and complex parts without time-consuming manual support removal.
Stratasys’ internal analysis suggests the additive manufacturing market for polymer jigs and fixtures is expected to grow at a 14.2% annual rate between 2019 and 2023, to nearly US$600 million, double the growth rate of the prior four years. With its FDM ABS-CF10 material, Stratasys says it is particularly focused on addressing applications in the aerospace, automotive, industrial, and recreational manufacturing industries. Parts applications include end effectors used with industrial robots, ergonomic aids such as lift assists and hand tools, and alignment fixtures on assembly lines.
Read more...
Subscribe to Get the Latest Updates from IMA Please click here
©2021 Injection Moulding Asia. All rights reserved.