Green expansions: Trinseo launches PMMA pilot recycling plant in Italy; Ineos commissions recyclable flexible packaging films pilot line in Belgium
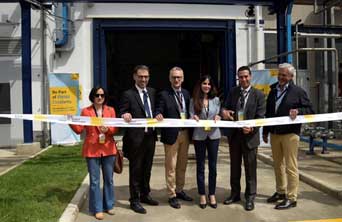
Specialty materials provider Trinseo has announced the launch of its new polymethyl methacrylate (PMMA) depolymerisation plant in Rho, Italy, marking a stride in the company's sustainability and recycling efforts. The facility is part of Trinseo's 2030 sustainability goals and aims to enhance the circularity of acrylic materials by converting them back into their original monomer form, methyl methacrylate (MMA).
The plant utilises an advanced continuous process technology developed in collaboration with the MMAtwo Consortium, backed by the European Union's Horizon 2020 program, to produce high-purity recycled MMA (rMMA). This process is particularly significant as it allows for the recycling of PMMA sheets, which were previously difficult to recycle mechanically. The technology also enables the removal of contaminants and additives from both pre- and post-consumer acrylic products, thus allowing for a broader range of PMMA materials to be recycled.
Trinseo's new facility will support the production of rMMA for use in the company's Altuglas and Plexiglas R-Life product portfolios. The resulting rMMA is said to match the quality of virgin raw materials, making it suitable for applications requiring high optical quality, such as vehicle taillights and caravan windows.
Francesca Reverberi, Senior Vice President of Engineered Materials and Chief Sustainability Officer at Trinseo, expressed enthusiasm for the facility's role in promoting a circular economy. The company's Chief Technology Officer, Han Hendriks, also emphasized the importance of the facility in expanding Trinseo's recycled feedstock capabilities and fostering innovation in recycled acrylic solutions.
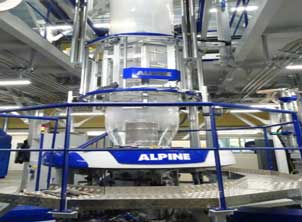
In other news, Ineos Olefins & Polymers Europe says it has become the first polymer producer in the world to successfully commission a new pilot line that it will use with customers to co-develop recyclable flexible packaging films. The multi-million Euro investment could help to prevent around 1 million tonnes of waste from being sent to landfill each year, it adds.
The new multilayer, blown film line, supplied by Japanese machine maker Hosokawa Alpine, with Machine Direction Orientation (MDO) has been installed at Ineos’ R&D centre in Brussels, Belgium. It enables customers to carry out full-scale tests without losing production capacity on their own lines. The first collaboration projects are already under way, developing new films that can be applied directly to customer production lines.
Flexible films provide lightweight, low emission packaging for transporting goods, increasing the shelf life of food products. However, today’s multi-material packaging films combine different polymers, each performing different functions, but which in combination make the film difficult to recycle. Making simpler films with the same performance means the new packaging can be more easily recycled, to meet the requirements of the EU Packaging and Packaging Waste Regulation.
The technology heats and stretches polymer films to improve their physical and barrier properties, enabling them to be used in different product applications.
Subscribe to Get the Latest Updates from IMA Please click here
©2024 Injection Moulding Asia. All rights reserved.