Green expansions: Changhua Chemical breaks ground on carbon-to-polyols plant; APK scales Newcycling for post-consumer waste
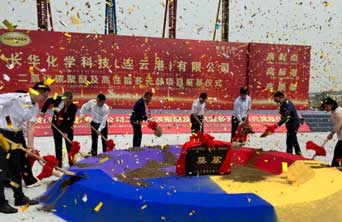
China’s Changhua Chemical is beginning the construction of the country’s first manufacturing site for sustainable polyols made from renewable carbon. Located in Lianyungang, the world scale facility will produce Carnol, a new line of polycarbonate ether (PCE) polyols with 20-30% fewer greenhouse gases compared to standard chemistries.
The technology for Carnol is based on a proprietary process and catalyst from UK’s Econic Technologies, which replaces fossil feedstocks with captured CO2. Changhua’s new site is expected to produce annual commercial volumes of about 80,000 tonnes in early 2025 and will scale to over 1 million tonnes in the coming years.
Carnol polyols can be used to manufacture polyurethane foams, coatings, and elastomers with improved environmental and performance claims. They reduce carbon footprint and enable circular design by keeping CO2 out of the atmosphere and inside products like furniture and mattresses, automotive parts, apparel and footwear, and construction materials. Notably, adding captured carbon at the molecular level also lets formulators finetune and enhance performance characteristics such as the comfort of mattress foams, the durability of coatings, and tensile strength in a variety of applications.
Carnol polyols are compatible with emerging recycling technologies and can be used in combination with recycled and bio-based polyols to achieve even greater reductions in greenhouse gas emissions.
“The chemical sector in China has an important role to play in supporting national and global sustainability goals. At Changhua Chemical, we are proud to be taking a leading position by introducing new sustainable polyols. Carnol polyols will help manufacturers across a range of industries bring new solutions to market that have fewer greenhouse gases and less waste,” said Dr. Gu, Chairman/Owner of Changhua Group.
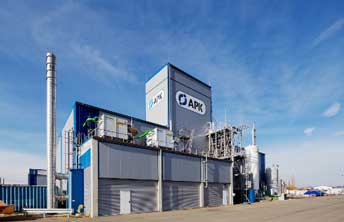
In other news, Germany’s APK AG says it has successfully scaled its proprietary Newcycling technology for the recycling of post-consumer plastic waste. Flexible, multi-material packaging waste is the focus as a material stream.
“We were able to increase the laboratory scale by 200 times and have reached an industrial scale," explains Dr Robert Marx, Chief Technology Officer of APK AG. "The development of Newcycling is progressing continuously, even during the provisional self-administration procedure in which APK AG is currently engaged. Our post-consumer process runs smoothly day after day and the quality of the corresponding Newcycling recyclates is impressive. Sensitive applications such as packaging in the personal care sector will represent an important market for our LDPE recyclate.”
Newcycling combines mechanical pre-treatment steps with solvent-based purification and separation processes. This enables the physical technology to efficiently recycle complex, flexible packaging waste - such as multilayer films - and to obtain high-quality, pure recyclates. After first being scaled up based on waste from multilayer film production and tested up to commercial LDPE and PA products, Newcycling is now dedicated to post-consumer waste.
The successful scaling of post-consumer Newcycling was advanced quickly thanks to the subsidiary APK Newcycling Competence Center GmbH (APK NCC).
In 2022, APK AG acquired the technical centre in the Höchst Industrial Park, Frankfurt, Germany.
“The most important task of our pilot plant is to prepare and optimise the processes developed by APK AG for later production,” says Dr David Blum, Managing Director of the APK NCC and Operations Manager of the technical centre. Not only was the volume increased 200-fold - the quality of the recyclates was also successfully reproduced and optimised in terms of decolourisation and yield. “We have shown that recyclates from our campaigns can be used for personal care packaging, especially for cosmetic rinse-off applications. External toxicologists have confirmed this based on our data,” explains Hagen Hanel, Head of Technology and Science, APK AG.
Plastic recyclates that meet the demanding quality requirements for use in the sensitive area of personal care and cosmetic packaging are in short supply. The current changes to the EU packaging regulation continue to drive demand. Harmonised toxicological guidelines and standards can strengthen trust in the market and promote the use of post-consumer recyclates, especially regarding polyolefins such as PP and PE.
In April 2024, the CosPaTox (“Cosmetics, Packaging and Toxicology”) consortium published a guideline with comprehensive recommendations for the safety assessment of recycled plastics in cosmetics and cleaning packaging. As a member of the consortium, APK AG contributed to the expertise in the guidelines. The quality classifications of the Newcycling recyclates are carried out accordingly.
“With the help of our piloting, we are reducing investment and manufacturing costs for future plants, enable further product and technology development, and are thus creating an important basis for successful restructuring and future expansion with new APK investors,” explains Dr Robert Marx.
Since the end of May, APK AG has been restructuring itself as part of a self-administration process. The company's goals of maintaining APK AG in Merseburg and building further large-scale plants for the Newcycling of post-consumer packaging waste remain priority.
Subscribe to Get the Latest Updates from IMA Please click here
©2024 Injection Moulding Asia. All rights reserved.