Expansions: Röhm expands capacity of PMMA moulding compounds in US; MBA Polymers sets up line for advanced recycling of car bumpers
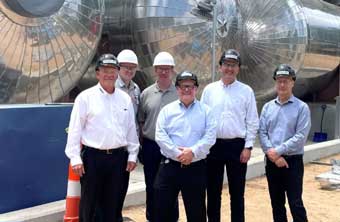
To further strengthen the market position of its specialty moulding compounds globally, German materials firm Röhm has significantly expanded its production capacity at the Wallingford plant in Connecticut (US) in June 2024. The improvement was possible by modifying and redeploying an existing production line at the Wallingford site, providing customers with faster delivery and meeting increasing demand globally.
Polymethyl methacrylate (PMMA) products from Röhm are sold on the European, Asian, African and Australian continent under the registered trademark Plexiglas and in the Americas under the registered trademark Acrylite. The Wallingford facility has more than 50 workers and operates several production lines that manufacture specialty PMMA moulding compounds.
The Wallingford site is also a key production site for Cyrolite, a transparent, acrylic-based plastic especially for medical applications.
“Röhm is a reliable partner worldwide and is driving forward the expansion of capacities, both in production and in technical service, in all relevant regions.” says Siamak Djafarian, Senior Vice President and Head of Röhm’s Moulding Compounds business unit. “We are the only global manufacturer of MMA and PMMA, complete with downstream compounding, in all three important regions of Asia, Europe and North America. This makes Röhm a strategic and reliable partner for customers around the world.” Röhm is the European market leader in PMMA moulding compounds and ranks second on a global scale.
PMMA from Röhm has been established on the market for 90 years and is well-suited for applications where durability, resistance to weather and UV, colour fastness, high luminosity and transparency as well as hardness and scratch-resistance are key. Started as an independent company almost five years ago with the goal of creating methacrylate, Röhm is well on its way to achieving this target. The central component of the strategy and the flagship project is the construction of a production plant for methyl methacrylate (MMA) in Bay City, Texas (US) where the LiMA technology developed by Röhm is used.
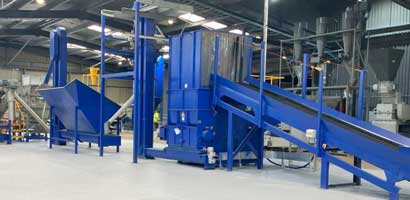
In other news, recycling firm MBA Polymers UK has launched a specialist processing line to recycle car bumpers from end-of-life vehicles (ELVs), the company has announced. The move will significantly advance its plans to create a fully circular economy for car bumpers in the UK.
The facility will also help car manufacturers meet proposed amendments to the ELV directive in the EU and the UK which has proposed a that at least 25% of plastics in a car must be made from post-consumer plastics.
By expanding the recycling of car bumpers, MBA Polymers UK will significantly reduce the more than 900,000 tonnes of plastic from cars which currently goes to landfill or incineration in the UK and EU each year.
Based in Wimblington, near Cambridge, the dedicated line will be supplied from MBA Polymers’ growing number of collection sites and access feedstock from the UK’s biggest ELV recycler, EMR. This creates consistent and high-quality recycled resins for the production of high-impact polypropylene and filled polypropylene.
MBA Polymers UK's pioneering technology and the reliable performance of its recycled plastics has already seen some of the largest automotive manufacturers switch to using the firm’s sustainable materials in their new vehicles.
In contrast, the sustainable materials MBA Polymers UK delivers on to manufacturers achieve carbon savings of between 75% and 86%making it the first recycled plastics to carry the Carbon Trust's Low CO2 label, it adds.
Earlier this year, MBA Polymers UK announced it had achieved RecyClass certification for the sorting, washing, extrusion and pellet production for a range of recycled plastics including ABS, PP, FPP, HIPS and HDPE. RecyClass is a not-for-profit cross-industry initiative that uses rigorous scientific analysis to ensure the traceability of waste in plastic recycling processes based on the principles of the EN 15343 standards.
Paul Mayhew, General Manager at MBA Polymers UK, said: “As the automotive industry faces the challenge of meeting recycling targets mandated by the upcoming revision to the EU’s ELV Directive, sourcing truly sustainable recycled plastics is becoming more important than ever.
“The opening of this new dedicated line at our facility in Wimblington will enable MBA Polymers UK to recycle ever greater volumes of plastics, using our advanced separation and processing techniques to deliver high-quality polymers back to manufacturers.
“Plastics make up around 12% of a cars’ weight and this latest development highlights how MBA Polymers UK will enable the automotive industry to create truly circular supply chains on the path to net zero.”
Subscribe to Get the Latest Updates from IMA Please click here
©2024 Injection Moulding Asia. All rights reserved.