Additive Manufacturing
After a consolidation phase and reorganisation of its shareholder structure, after a management buyout, 3D printer manufacturer AIM3D is back in the game, it adds.
Germany-based AIM3D says it has also succeeded in optimising its patented Voxelfill process, for overcoming inhomogeneous strengths in 3D-printed components. The firm adds that Voxelfill achieves a high level of process stability comparable to injection moulding thanks to material-friendly extrusion and cross-layer material filling. Tensile tests with materials firm Sabic’s Ultem PEI 9085 resin confirm the homogeneous properties.
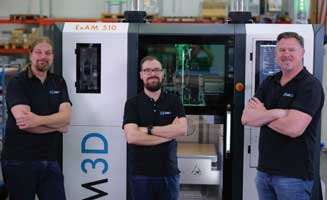
Variations of the Voxelfill strategy enable hybrid multi-material solutions with different Voxelfill materials and different materials, including within the same component. In this way, the material properties can be ‘customised’. Defined component weight, damping properties, elasticity or changes to the centre volume chambers (selective densities), component properties could be influenced in a targeted manner on the basis of FE simulations.
Clemens Lieberwirth, CTO at AIM3D, commented, “Of course, the Voxelfill process is particularly suitable for 3D printing of plastics and fibre-filled plastics, but it is also suitable for 3D printing of metal and ceramic components using the CEM process. In general, there are advantages due to the higher build speed and cross-layer filling.”
Meanwhile, AIM3D is cooperating with Denmark-based software development company Create it Real on software optimisation and Germany’s Replique for Ultem applications, which is extensively used in aerospace and industrial applications. The amorphous material has high temperature resistance, is flame retardant, and has good strength and chemical resistance. Although expensive, it meets many requirements for manufacturing components for industrial and aerospace applications.
However, for serial production, printing needs to be improved and material costs need to be decreased. If AIM3D can achieve this, it can move into producing high-value components with Replique, with whom it has collaborated on a panel for Alstom.
In its tie-up with Create it Real it hopes to improve slicing in its slicing software, SlicEx, which it white labels from Create it Real. The company is hopeful it can enhance properties while printing at 150 cm³/ hour and is aiming for a single machine to produce 1-4 tonnes of parts.
As well, AIM3D’s ExAM 510 system is predestined for use in industrial production. The system, which was launched in 2022, currently operates at a maximum build rate of 150 cm³/hour, and it is aiming to up it to 300-600 cm³/hour.
Bio-based resins could offer recyclable future for 3D printing
A new type of recyclable resin, made from biosourced materials, has been designed for use in 3D printing applications.
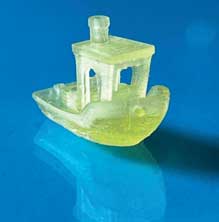
In a study, published in Nature, researchers from the University of Birmingham, UK, showed that highresolution, 3D printed structures can be manufactured from an entirely bio-sourced feedstock.
Once they have reached the end of their useful life, the products can be recycled within an almost fully closed-loop system.
Photopolymer resins, which harden – or cure – on exposure to light, are commonly used in the manufacture of bespoke 3D printed parts. However, while technologies to improve the resolution of 3D printing and its speed of manufacture have advanced considerably, the resins themselves have changed very little since the process first emerged in the 1980s.
The basic materials – usually epoxies or acrylics – come mostly from petrochemical feedstocks. Although some progress has been made in the use of more sustainable resins derived from biomass, the recyclability of these is still limited, because they rely on irreversible bonds being created when the resin hardens. To break these bonds, additional chemicals have to be added at each stage, resulting in a ‘snowballing effect’, in which the only way to recycle the material is to make more of it.
In contrast, the Birmingham-led team has, for the first time, succeeded in producing a photopolymer resin that can be printed at high resolution but can then be broken back down to its constituent parts, recycled and reprinted, with the addition of just a small amount of photoinitiator to maintain the material’s curable properties.
The feedstock for the process is made from lipoic acid, a naturally occurring fatty acid molecule that is commonly sold as a dietary supplement. The team made a combination of two monomers from the lipoic acid from which they were able to make a resin that could be recycled either back into the monomers, or right back to the original molecule for recycling.
In the study, the researchers completed two ‘recycles’, but anticipate that further recycles would be possible.
Uses for the material could include industries where rapid prototyping is used to test products before moving to mass production. Although currently the material is more flexible than might be commonly used in industry, future applications could include automotive parts, medical and dental components, and even jewellery design.
University of Birmingham Enterprise has filed a patent application covering the resin and its use in 3D printing.
China slated for US$8 billion in 3D printing hardware sales by 2032
China’s additive manufacturing (AM) market is expected to reach US$8 billion a year in hardware sales by 2032, according to a new Market Opportunity Brief by Additive Manufacturing (AM) Research.
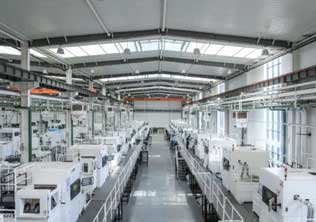
The report titled “The State of Chinese Additive Manufacturing” analyses the state and outlook for the additive manufacturing (AM) industry in China and considers such formative topics such as standards development, regional and governmental support, and foreign AM companies operating in China, as they shape Chinese 3D printing landscape today. Chinese AM markets are detailed for both the metal 3D printing and polymer 3D printing markets, and sectors analysed include Aerospace & Defense, Automotive, Medical & Dental, Energy, General Industry & Tooling, and Services Bureaus.
Analyst for AM Research Molitch-Hou, attributes the growth in part to “government stimulus”. However, he adds that it can be tough to validate claims from the outside. For instance, in 2023, one of the country’s leading makers of metal 3D printers, Xi’an Bright Laser Technologies (BLT) announced nearly 60% revenue growth from the prior year. This figure, combined with the increasing number of lasers that can be configured on Chinese metal 3D printers, should more than pique the interest of manufacturers globally.
In fact, evidence coming out of the Chinese AM industry suggests that country is catching up to and, in many ways, surpassing the US and Europe in terms of 3D printing adoption and manufacturing.
From 2015 to 2022, China’s AM sector grew at a rate of about 30%. This has significance both inside and outside of China, as well as inside and outside of the 3D printing industry.
He adds that much of the growth that’s taking place is remaining within the country. While AM professionals are now well aware of a handful of prominent Chinese players, there are many more that they have never heard of and, despite this fact, some of those lesser-known businesses are advancing at a pace similar to their more recognised competitors, according to Molitch-Hou.
Subscribe to Get the Latest Updates from IMA Please click here
©2024 Injection Moulding Asia. All rights reserved.