Automotive Industry: Plastics hit the ground running in the EV evolution
In transportation, electric vehicles (EVs) are a key to countries around the world achieving climate goals. But the heavyweight EVs are turning to plastics and composites to reducing the weight and meeting sustainability goals, says Angelica Buan in this article.
EV sales on a high
Major industries are recovering from the cataclysmic effects of the Covid-19 pandemic. But this is likely not the case with electric vehicles (EVs). Peddling to the concept of contributing to reductions in carbon emissions, sales have soared for EVs, even in the wake of the pandemic crisis.

To wit, global sales for EVs have increased since 2020 and are projected to grow further as governments double up their support to global sustainable development goals, moored to keeping the global average temperature to below 2°C above pre-industrial levels and limiting the temperature
increase to 1.5°C above pre-industrial levels. It is envisaged that by 2030, the adoption target of between 145 million and 230 million or more EVs (but excluding two/three-wheelers) will be achieved.
The drive to increase the adoption of EVs, made possible by fiscal incentives, has produced positive results. The year 2020 has witnessed 3 million new registrations of EVs – a 41% increase against 2019, led by Europe registering 1.4 million EVs, according to the 2021 IEA Global Electric Vehicle Outlook.
The report has indicated bright prospects ahead for the EV industry. During 2021, the report cited sales growth increasing by around 140% compared to the same period in 2020. The growth is represented by 500,000 sales in China and an estimated 450,000 vehicle sales in Europe. The US vehicle sales more than doubled during this year’s audit, compared to the first-quarter 2020 sales.
This growth trajectory is deemed to continue as advances in battery technologies and mass manufacturing are to lower the cost of EVs, the report said.
Plastics at the helm of under-the-hood applications
Demand for EVs is increasing as eco-awareness grows. Nonetheless, EVs are a work in progress, from reducing the weight to scaling down size since a lighter vehicle consumes less energy, is more fuel efficient and runs longer.
For this reason, OEMs and their suppliers rely on plastics and composite materials to produce lighter weight cars and parts as well as provide properties that meet the performance requirement for EVs.
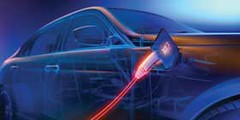
In this area, Belgian chemical company Solvay recently launched Amodel Supreme PPA, a new line of polyphthalamide compounds. The PPAs are said to exhibit stiffness and toughness to replace metal in traditional and structural applications such as clutch cylinders, shift forks and body in white. Other applications range from high-temperature automotive components used in electric drive units including e-motors, power electronics, housings for high-temperature electrical connectors, electric/ electronic devices and telecommunication equipment components.
Solvay says the PPA features the industry’s highest glass transition temperature (Tg) of 165°C, which enables higher mechanical performance compared with traditional PA4T and PA6T-based materials at elevated temperatures. There is also a greater Coefficient of Linear Thermal Expansion (CLTE) match to metals that allows for ease in designing over-moulded components.
In addition to thermo-mechanical performance, Amodel Supreme PPA features improved electrical properties, including volume resistivity and dielectric strength above 150°C. These materials also maintain critical electrical properties, like comparative tracking index (CTI), after exposure to high temperatures over time. The compounds were designed to ensure hydrolytic stability against new EV cooling fluids.

Similarly offering new material solutions for heat-resistance, chemical manufacturer Sabic has introduced a 5-micron Elcres HTV150 dielectric film for high-temperature, high-voltage and professionalgrade capacitor applications, such as traction inverters for hybrid, plug-in hybrid and battery EVs.
This new film, which is produced in collaboration with Japanese ultra-thin film extrusion specialist Shin-Etsu Polymer, features high-heat performance up to 150°C, which exceeds the temperature and voltage capabilities of currently available products in the market. It can help support the transition from conventional semiconductors based on silicon (Si) to next-generation, wide-bandgap technologies based on silicon carbide (SiC), improving the efficiency of inverter modules.
This dielectric film can support the design of high-voltage, high-temperature DC link power capacitors that can store large amounts of electrical energy for long periods without significant leakage of current or loss of charge. The film also offers other advantages for next-generation battery EVs, such as high voltage stability at high temperatures, which an internal testing done showed it having a lifespan of 2,000 hours at 500V and 150°C; low dielectric loss at high frequency and ability to self-heal to avoid catastrophic failure.
Composites for lighter EV batteries
Up to this day, electric cars still come at a hefty price tag, and the battery is one reason for that. The battery is the EV’s life line: it stores energy, powers the car and is responsible for its range. It also takes up space and accounts for the largest share in weight of an EV.

What to make of a bulky, pricey, heavy battery? These are considerations being tackled by a consortium of companies comprising Evonik, Forward Engineering, Lion Smart, Lorenz Kunststofftechnik, and Vestaro. The group has developed a brandindependent, cost-effective battery concept for EVs that has a lightweight construction.
Accordingly, the battery concept’s weight has been reduced by 10% compared with other commonly used material combinations. Lion Smart, a Germanheadquartered service provider for OEMs and suppliers in the automotive sector, has assembled the batteries using the supercell concept developed in-house. The firm says the battery design is particularly safe, as the individual cells are enclosed in a non-flammable dielectric coolant. This also ensures a constantly low average temperature within the battery, which benefits cell aging.
For the battery housing, Lorenz developed a new glass-fibre-reinforced epoxy sheet moulding compound (SMC) using German speciality chemicals company Evonik’s Vestalite S epoxy hardener, with properties in terms of bending, impact, and fire resistance. Vestaro, an Evonik-Forward Engineering joint venture and composites solution provider for the automotive industry, developed the structure of the housing with a bottom plate made of aluminium and the carrier plate for the battery management system attached to it. Transversal beams are used to attach the battery modules.
Lorenz also produced several complex hardware demonstrators to verify the suitability of the material and the manufacturing process for series production.
Meanwhile, Forward Engineering, a German company specialising in design and development of mixed material fibre-reinforced polymer and composite structures, has tested the battery concept for safety and suitability.
The battery concept is available in three energy configurations of 65 kWh at a total weight of 412.1 kg, 85 kWh at 527.3 kg, and 120kWh with 800V at 789.2 kg. The group attested that in terms of energy density, safety and cost, the three energy configurations are at least on a par with current battery models on the market and even surpass them in specific metrics.
Energy-saving material solutions for a safe drive
Along the same vein, German consultancy AMAC and Dutch specialist in composites products Pontis Engineering have joined forces to develop composites for e-mobility applications. These range from the development of lightweight over structural battery housings to complete EVs for road, industry, water and air transportation. Pontis Engineering will utilise its expertise in engineering solutions for advanced composite applications to develop lightweight electrical passenger cars reducing fuel consumption and carbon emissions. It also offers feasibility studies over industrial transportation to last-mile-delivery, as well as tailored cost-efficient solutions, based on a Design for Manufacturing approach.

Similarly, US-based composite solutions provider Continental Structural Plastics (CSP) and Japanese materials firm Teijin Group have teamed up to introduce an array of composite formulations said to meet the most stringent EV battery enclosure performance standards. These include flammability, thermal runaway and VOC emissions while offering the design flexibility of SMC. These new composites include a low VOC formulation, an ATH filled system, an intumescent system and a phenolic system.
The low VOC formulation addresses the stringent EU (European Union) VOC regulations. To address the regulatory and customer targets in Europe and Asia, CSP modified its TCA (Tough Class A) Ultra Lite material, eliminating benzene, a highly flammable compound, as a by-product. The material, first launched in 2014, is a lower 1.2 specific gravity (SPg) SMC formulation.
Modifying the formulation enabled the material to meet VOC requirements after standard prime and E-coat oven bake cycles. However, outside of the US most parts will not undergo high temperature paint bakes so further VOC reduction was required. CSP’s newest low VOC material releases significantly fewer VOCs as moulded.
For EV battery enclosures, where composites can be used to reduce weight, improve strength and stiffness, CSP says its composites can also improve vehicle safety. It is introducing three such formulations that can be adapted using different fibre types or formats, such as glass, carbon, blended, chopped and/or continuous. These include a traditional high-fill polyester/vinyl ester ATH system that uses conventional SMC chemistries and is easily adapted to existing tools and will give baseline flammability performance in the right design; an intumescent system utilising chemistry similar to traditional SMC, but with better flammability and thermal runaway performance, as well as increased mechanical properties over ATHfilled system; and a phenolic system which offers flame retardance, heat and chemical resistance, and electrical non-conductivity characteristics. Clearly, lightweighting innovations are oiling the e-mobility evolution to address market demand for the next generation climate-friendly vehicles.
(IMA)Subscribe to Get the Latest Updates from IMA Please click here
©2021 Injection Moulding Asia. All rights reserved.