StackTeck’s TRIM allows for lightweighting; saving material costs
Canada-based StackTeck developed a technology called TRIM for light weighting injection moulded parts in 2014, which has developed over the years and developments have demonstrated lightweighting technologies that were used for a range of more complex moulding challenges.
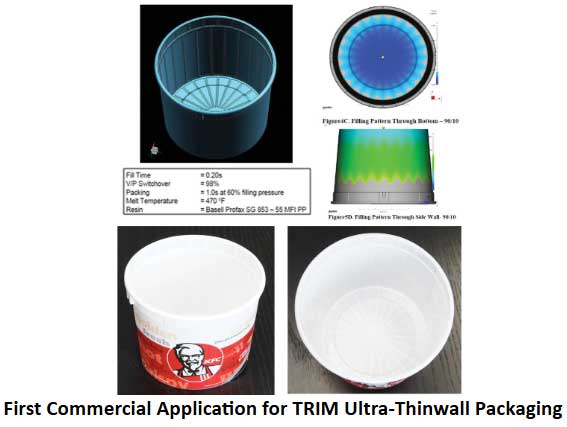
Thin Recess Injection Moulding (TRIM) uses an advanced approach to thin out parts of the wall section well beyond the conventional thin wall packaging approach.
The first commercial TRIM application was a 64 oz. round pail which won a 2014 IMDA award for “Best Thinwall Packaging”. The product was born out of a customer’s challenge to find a way to reduce the weight of an award-winning part that was already at the limit of conventional thinwall packaging. By pushing the TRIM part design to the limit, covering approximately 90% of the part with ultra-thin panels, a weight savings of 41% was achieved. Most of the surface of this part had a wall thickness that corresponded to an L/T ratio of 550.
2015: Next Generation TRIM (Thin Recess Injection Moulding) was presented at NPE2015
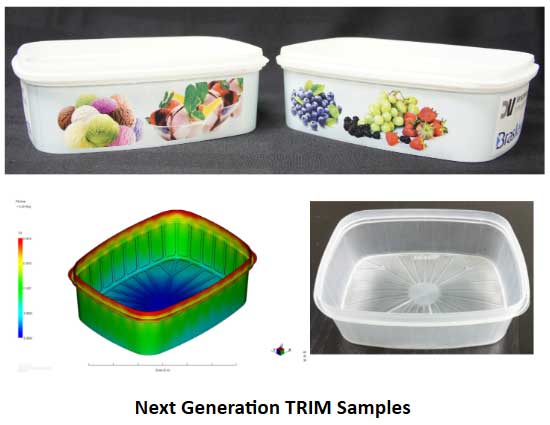
The next generation of TRIM was presented in a single cavity mould for a 32 oz. tamper evident rectangular container, which had ultra-thinwall panels covering 90% of the sidewall and bottom areas. The average L/T ratio of the overall part was 520.
2019: Demonstration of TRIM Technology and MuCell for Ultra-Light Container at K2019
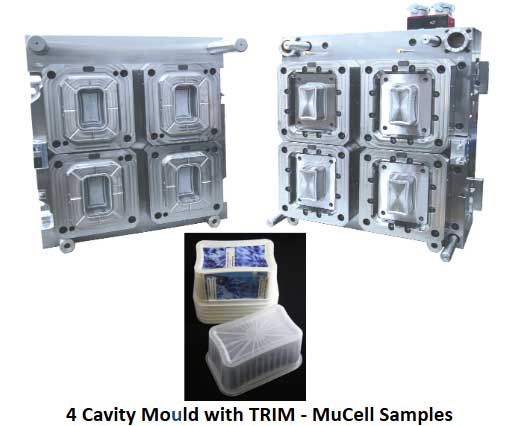
A 1x4 TRIM IML 500g rectangular container mold ran at the KShow with the MuCell process This mold was optimised with StackTeck’s KoolTrackTM Technology built with conformal cooling channels in gate pad/insert and core cap.
The IML container produced, featured a 3-sided label and it is 20% lighter than a conventional thinwall container combining two effective ultra-light-weighting technologies for thinwall applications.
2024: StackTeck Demonstrated Ultra-Thin PET Round IML Container Capability
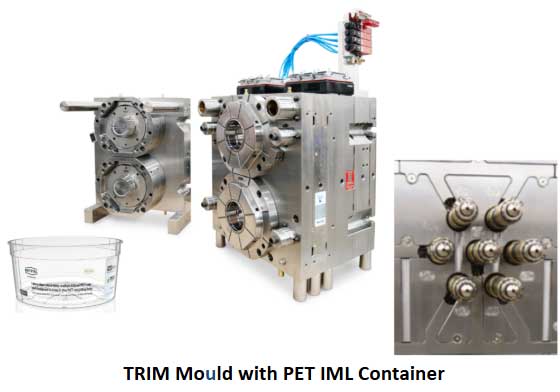
A new approach to molding ultra-thin 450 ml PET food tubs was presented at NPE2024 with a mould technology that delivered thinwalling technology combining TRIM with a set of seven sequentially controlled valve gates to yield the lightest part of this type ever moulded.
A new standard was set in moulding PET containers using at least 30% content of hard-to-fill PET with a high IV level mixed with a high volume, easier filling low IV PET resin with the intention that customers would be able to run the same part using 30% rPET.
This approach to lightweighting enabled such PET parts with thinner wall sections that are typically used for thinwall PP containers.
Today, StackTech says these technologies can be used to produce injection moulded parts at unprecedented part weights, creating new opportunities for injection moulders.
Subscribe to Get the Latest Updates from IMA Please click here
©2025 Injection Moulding Asia. All rights reserved.