Recycling: Arburg develops digital pilot functions to stabilise moulding process
Manufacturing moulded parts out of virgin material from shot to shot and batch to batch at a consistently high part quality is state of the art, but usually places high demands on the controller technology.
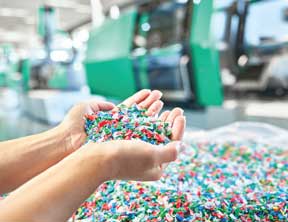
When it comes to processing content such as post-industrial recyclate (PIR), post-consumer recyclate (PCR) and bioplastics, the material and processing properties can vary considerably. Control concepts that ensure constant mould filling and, ultimately, consistent quality of the end products are therefore required if recyclates are to be used efficiently.
Thus, German machinery maker Arburg has developed digital pilot functions for its machine controllers that keep the process stable during the injection and holding pressure phase.
“Black boxes” challenge
From the machine’s point of view, injection moulding involves
two large “black boxes” that significantly influence process
stability and part quality. This is because the machine itself has no
knowledge of
• which material is fed into the hopper, or
• what happens between the two mould mounting platens.
These are two major challenges when it comes to reliably controlling process parameters such as the temperature progression of the moulding compound and the temperature progression and pressure profile in the mould.
The biggest difference between processing recyclates and virgin material is that the material properties and characteristics such as mechanical quality, colour and smell can vary within a delivery or an order over a wider range. Since no clear material specification can currently be assigned to the recycled granules in most recycling processes, no data sheet is available during machine setup, which makes processing significantly more difficult.
However, Arburg says its Gestica and Selogica controllers for Allrounder machines have pilot functions, for example, that counteract fluctuating viscosities in the melt: “aXw Control ReferencePilot” and “aXw Control RecyclatePilot” can detect and reliably even out irregularities and actively control the ongoing injection process in order to keep the mould filling as constant as possible and ensure consistent part quality despite major variations.
Melting process as an influencing factor
A homogeneous and stable melting process is an important influencing factor in the production of good parts. It starts with the material being fed into the plasticising screw as evenly as possible.
If the material is in the form of granules, recycled plastic can generally be processed as well as virgin material without the need for additional hardware.
With flakes, size and shape can vary, while reground material, on the other hand, which is material from plastic parts that have only been shredded with a sprue grinder, consists of fragments of different sizes, ideally in grain sizes of 2-5 mm. These grains are usually accompanied by finer material, up to and including dustlike material. To ensure a stable melting process, any dust must be removed fromtheregroundmaterial.
Recyclate package for reground material and flakes
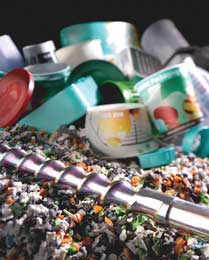
For the processing of reground materials and flakes, Arburg says it offers a retrofittable recyclate package that combines software and hardware features.
Among the software features are multi-stage start-up parameters and the digital “aXw Control ScrewPilot” assistance function, which ensures precise and stable mould filling. In terms of hardware equipment, a modified cylinder module enables uninterrupted feeding even of poorly flowing materials.
A plasticising screw with a modified, deeper highcompression (HC) geometry ensures homogeneous processing. Grooves in the feed zone help the material to be drawn in, despite its irregular shape, and conveyed forward in a stable manner. The screw also has a CrN coating to reduce the formation of deposits and wear caused by unexpected foreign bodies.
ScrewPilot: Control concept for the “fill mould” core process
Filling the mould cavity in a reproducible manner from cycle to cycle is the basis for consistent component quality. A successful control concept for this is the “aXw Control ScrewPilot” or “position-regulated screw” pilot function, where the filling process is adapted to the requirements of the flow path in several stages by a speed-regulated screw movement.
This concept can be compared to a driving assistant for cars: if the movement (in this case of the screw) deviates from the programmed speed due to disruptive influences (here, for example, variations in the viscosity of the plastic melt), it is regulated in a way that ensures that the distance is still covered in the allotted time. The active acceleration and braking dynamically compensates for disruptive influences, so that a constant amount of melt is fed into the cavity.
These dynamics have proven to be particularly useful at high injection volume flows, especially when it comes to preventing pressure peaks and overfilling by targeted and rapid braking.
ReferencePilot: Control in the holding pressure phase
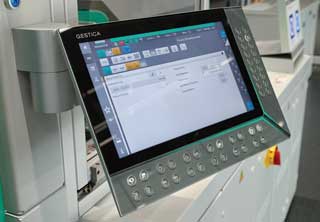
The holding pressure phase is also crucial for part quality. It is usually executed as a quasi-static, pressure-controlled process, with the optimum parameters previously determined by a machine setup technician.
No account is taken of short-term influences during ongoing production, such as viscosity variations in the melt (caused by recyclates, lubricants or colour additives), or long-term wear, e.g. on the nonreturn valve and other mechanical components. In the long term, this can lead to variations in the cavity pressure and hence to irregular part quality
For this reason, as early as 1988, Arburg developed an injection process regulation function that is integrated in the controller and regulates the holding pressure curve in real time via a pressure sensor in the mould.
This software function has been continuously developed and is now known as “aXw Control ReferencePilot”.
The ReferencePilot uses the nominal value reference curve of a good part as the basis for active regulation in the holding pressure phase, where the current holding pressure is adjusted according to the internal pressure. A pressure sensor positioned as close as possible to the sprue in the mould is required as the associated hardware.
Mould cavity pressure as an influencing factor
So that it can quickly counteract disruptive influences and actively balance out pressure variations, the software receives signals regarding mould cavity pressure that are recorded in real time by the sensor. This enables ReferencePilot to regulate the internal pressure curve from the current actual value to the desired nominal value.
When ReferencePilot is used for control, the pressure conditions in the mould are precisely adjusted from shot to shot to match the reference, with the actual value being raised to the nominal value. This results in a constant shot weight and consistently high part quality, without the need for manual intervention during process parameterisation.
Calibrated pressure sensor required
To be able to use ReferencePilot, two conditions must be met:
• The injection moulding machine must be equipped with “aXw
ScrewPilot”, which is standard for electric and hybrid Allrounders.
• There must be enough space in the mould cavity to install a
pressure sensor.
The sensor itself causes additional expense; in addition, expertise and time are required to recalibrate it for each setup process and to maintain it regularly. This is the only way to ensure that the internal pressure sensor measuring equipment is fully functional and delivers the correct signals.
If all requirements are met, the injection moulding process can be stabilised quickly and reliably through the interaction of the sensor and the pilot function. The number of start-up cycles can be greatly reduced and there is less scrap. The results are longer, trouble-free production times, fewer downstream testing processes and increased production efficiency. Depending on the case of application, investing in a sensor system can quickly pay off.
ReyclatePilot: Control in the injection phase
An alternative is the new “aXw Control RecyclatePilot” function,
which controls the injection moulding process directly in the injection
or mould filling phase based solely on data from the standard
machine sensor system. Compared to ReferencePilot, which receives
signals directly fromthecavity, theRecyclatePilot has a longer partial
control circuit. Nevertheless, it offers a number of clear advantages:
• There is no need for additional sensors.
• The pilot function integrated into the controller can be
activated simply by pressing a button.
• The function uses the proven sensor system inside the
machine, which only needs to be calibrated every few years.
• This pilot function balances out short-term variations from
shot to shot and also across cycles.
Process control at the push of a button
The operator initially optimises the process settings as usual so that the required quality of the good part is achieved. This reference is transferred to the pilot function via a control command. An additional command activates RecyclatePilot, which then analyses the injection behaviour, detects distinctive points and deviations in the injection process and ensures that the injected volume and therefore the mould filling remain constant.
This is done by comparing the event pattern in the same cycle with the reference entered during the injection phase and, if necessary, adjusting the switch-over point at short notice. In addition, correcting the dosage volume also makes the overall process more stable in the long term and across cycles.
Conclusion
The controller is the “brain” of an injection moulding machine and can provide operators with comprehensive and active support. With the help of digital pilot functions such as RecyclatePilot and ReferencePilot, process reliability can be significantly increased during the processing of recyclates by means of active control in the injection and holding pressure phases.
The injection profile and filling process of the moulded part remain stable and correspond to the specified reference.
Subscribe to Get the Latest Updates from IMA Please click here
©2025 Injection Moulding Asia. All rights reserved.