Polyamide sustainability: Domo/Hynamics to produce PAs from low-carbon hydrogen; DSM Engineering Materials launches 100% bio-based PA with halved carbon footprint
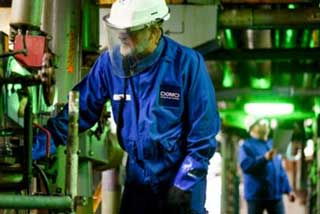
Polyamide (PA) materials maker Domo Chemicals and Hynamics, a 100% subsidiary of EDF Group specialising in the production of low-carbon hydrogen, have entered into a partnership project with the objective of achieving zero-carbon for 100% of the hydrogen used at the Belle-Étoile industrial site, in Saint-Fons (south of Lyon, France), in the heart of the French Vallée de la Chimie (“Chemistry Valley”).
For the first time in France, the “HyDom” project will enable the installation of an 85-megawatt (MW) hydrogen production plant using the water electrolysis process at the Belle-Étoile site, with a production capacity of 11,000 tonnes/year of low-carbon hydrogen. The plant will be powered by the French low-carbon electric power mix. By 2027, it will supply 100% of the annual production of hexamethylene diamine, a key component used in the production of plastics.
The project will eventually prevent the emission of 84 kilotonnes/year of carbon dioxide (CO2). Hexamethylene diamine, and ultimately, durable and low-carbon polyamides, will be used in various applications in major industry sectors, such as automotive, electronics, and heating & cooling.
This project is a major step towards the decarbonisation of industrial sites that use grey hydrogen (produced from fossil fuels). The location in the Vallée de la Chimie within the vicinity of major transport routes opens up opportunities for the creation of a more complete hydrogen ecosystem.
The first phase of the project will consist of building up and ascertaining technical concepts and integrating the low-carbon hydrogen production plant within the larger production process of hexamethylene diamine.
Considering the high-power scale of the future electrolytic hydrogen production facility, the HyDom project is being developed in close collaboration with RTE (an organisation in charge of managing the French power grid), to solve connection issues. As a priority project for the industry's zero-carbon strategy and for the “France 2030” investment plan, HyDom is supported by the French government and has been presented to the European Commission for public funding.
According to Christelle Rouillé, CEO of Hynamics: “In line with the goals set out in the France 2030 investment plan for a resilient and decarbonised industrial sector, Hynamics is proud to support leading hydrogen-consuming industrialists in their decarbonisation efforts. In replacing the unit that currently produces hydrogen from natural gas, our project represents an important step towards industrial sovereignty and reaching our climate objectives.”
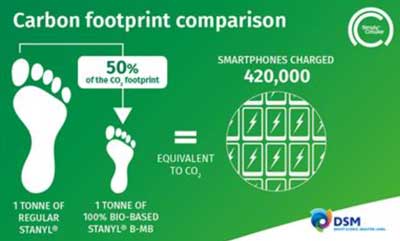
In other news, Dutch firm DSM Engineering Materials says it has launched a new, more sustainable version of its flagship product Stanyl PA: Stanyl B-MB (Bio-based Mass Balanced), with up to 100% bio-based content. Using the maximum possible levels of biomass-waste feedstock, it enables DSM Engineering Materials to halve the carbon footprint of this product line and, in turn, of the Stanyl B-MB-based products of its customers. This industry-first launch of a 100% bio-based high-temperature polyamide underlines the business’s ongoing commitment to helping customers fulfil their sustainability ambitions, it adds.
Global production of bio-based products roughly doubled between 2015 and 2020, but to conserve the planet’s natural resources and stay below the critical 1.5 degrees of global warming, the materials industry urgently needs to accelerate the shift to sustainable feedstocks. Seeing this need, DSM says it has committed to providing bio- and/or recycled-based alternatives for its entire portfolio by 2030.
Stanyl B-MB – now available with up to 100% bio-based content – is a fully ISCC+-certified mass-balancing solution, and delivers exactly the same characteristics, performance, and quality as conventional Stanyl. In addition, production of Stanyl B-MB now generates a carbon footprint up to 50% lower than the fossil-based original. In practice, this means a 3.3-ton CO2 reduction per ton produced – equivalent to charging 420,000 smartphones. Not only does this industry first further support the ‘Sustainable sourcing’ pillar of DSM Engineering Materials’ SimplyCircular initiative, but it also raises the bar for biomass-balanced solutions in the industry, according to DSM.
Said to be the only aliphatic polyamide in its class, Stanyl redefined polyamides when it was introduced, and is still the most used high-temperature polyamide today, according to DSM. Its high-temperature mechanics, flow and processing, and wear and friction resistance make it ideal for high-temperature applications in automotive, electronics, electrical, and consumer goods industries, such as USB connectors, automotive and industrial actuator gears, powertrain timing chains, bearing cages, and food contact conveyors.
(IMA)Subscribe to Get the Latest Updates from IMA Please click here
©2022 Injection Moulding Asia. All rights reserved.