Green materials: Genomatica, Aquafil breakthrough in plant-based PA6; Ineos to design recyclable PP/PE flexible packaging film using Alpine technology
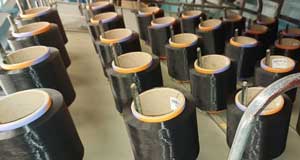
Sustainability firm Genomatica (Geno) alongside long-time collaborator Italy-based nylon maker Aquafil say they have successfully completed the first demonstration scale production runs for plant-based nylon-6 (PA6). The material is intended to reshape the US$22 billion nylon industry, enabling brands to meet demand from consumers for sustainable everyday materials from apparel to automotive parts to carpets. Geno and Aquafil have produced the first several tons of plant-based nylon-6 building block caprolactam, have converted it to PA6 polymer, and are now in the process of transforming it for evaluation in nylon applications such as yarns for textile and carpet and engineering plastics as part of pre-commercial quantities from demonstration production taking place in Europe.
The companies have been collaborating to first produce pilot-scale quantities of plant-based PA6 and have now advanced to produce pre-commercial quantities at demonstration scale which will help determine the final design of future commercial plants. The material will go to leading global brands and their value chain partners who are eager to explore and develop renewable products, create showcase goods and test feedback with customers.
Plant-based nylon-6 is Geno’s third major product line on a path to commercialisation. The company has executed high impact deals with a range of brands to accelerate the global commercialisation of sustainable materials, with the potential to reduce greenhouse gas emissions by 100 million tonnes in upcoming years. Recent milestones advancing the sustainable materials transition include: a collaboration with lululemon to bring plant-based materials into lululemon’s products, a production milestone with partner Covestro (for plant-based HMD used in sustainable coatings, and a partnership with Asahi Kasei (and a newly formed venture with Unilever to commercialise and scale plant-based alternatives to feedstocks like palm oil or fossil fuels, to make key ingredients used in everyday cleaning and personal care products.
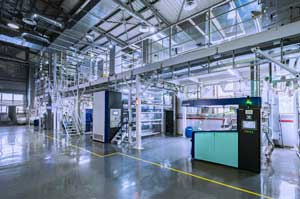
Meanwhile in other news, Ineos Olefins & Polymers Europe has announced a multi-million Euro investment in technology that will enable it to work with converters, brands and retailers to develop simpler, more recyclable flexible packaging film. The investment could help to prevent around 1 million tonnes of waste from being sent to landfill each year, it adds.
Using new multilayer, blown line technology with Machine Direction Orientation (MDO), Ineos and partners will work together to develop, design and produce PE and PP-based flexible packaging film using fewer polymers, increasing the recyclability of the product.
Flexible packaging films are a low carbon solution for transporting food and other goods; and they increase food shelf life, helping consumers to manage household bills. However today’s multi-material products combine polymers from different chemical families, making them difficult to recycle. Reducing the number of polymers used to produce packaging film will make packaging that is designed to be recycled.
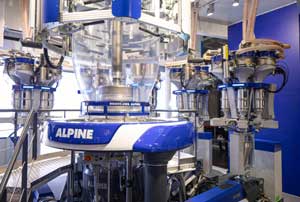
Ineos says it is the only raw material supplier to have invested in an inline MDO-multilayer line from Hosokawa Alpine, a pioneer in MDO technology, which heats and stretches polymer films to improve their physical and barrier properties, enabling them to be used in different product applications.
The new line will be installed in Ineos’ R&D labs in Brussels, Belgium, in 2023, where it will develop new, mono-material flexible film packaging products. It will leverage this capability and its expertise in resin design to work alongside partners on new generations of resins specially engineered for their flexible packaging products.
(IMA)Subscribe to Get the Latest Updates from IMA Please click here
©2022 Injection Moulding Asia. All rights reserved.