Green materials: Brita uses Ineos solution based on BASF biomass styrene; BASF’s IrgaCycle stabilises recycled plastics used to protect pineapples from sunburn in Malaysia
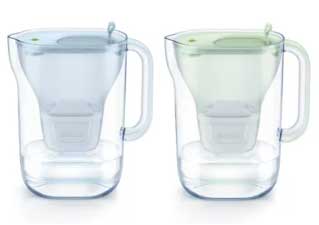
German water filtration firm Brita says it has selected a range of styrene maker Ineos Styrolution’s sustainable Terluran Eco, Styrolution PS Eco and NAS Eco materials as materials for its portfolio of water filter jugs. The materials include the recently introduced NAS Eco, a styrene methyl methacrylate (SMMA) material, which is the result of a cooperation between Ineos and German chemical firm BASF. It is built on BASF’s production of styrene monomer derived from renewable feedstock based on the mass balance approach. Ineo Styrolution uses the material as feedstock in its production of new sustainable styrenics solutions.
BRITA, known as a leading brand in, is among the first customers to benefit from Ineos Styrolution’s new sustainable solution. Specifically, the material is used for the production of Brita’s water filter jugs where it is applied for jug, funnel and lid parts, thus lowering the CO2 footprint without changes of moulding parameters and material performance. It also says the new Eco materials do not cause any interference in Brita’s production as it is a plug-in solution that does not require an adaption to Brita’s production processes.
BASF’s biomass balance (BMB) based styrene, certified by ISCC+, is used by Ineos Styrolution in the production of bio-attributed styrenics specialties, mainly transparent styrenics materials such as the company’s Eco family of SMMA products and the Luran Eco family of SAN (styrene acrylonitrile copolymer) products.
To produce styrene BMB, BASF replaces fossil resources like naphtha or natural gas with renewable feedstocks derived from organic waste or vegetable oils. It is one way to produce styrene via a mass balance approach. Mass balance is a chain-of-custody model that keeps track of the total amount (e.g., circular or other alternative) of feedstock throughout the production process and ensures a proper allocation to the finished goods.
“The mass balance approach, be it based on waste biomass or chemically recycled plastics, helps us to leave fossil resources in the earth and enables a fast transition towards alternative feedstocks,” says Stefanie Kutscher, Head of Business Management Styrene at BASF’s Styrenics Business Europe.” This can only be achieved if the whole value chain takes part.”
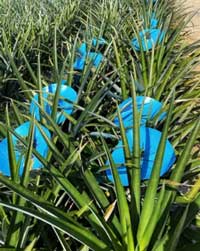
Meanwhile in related news, BASF and Malaysian recycling firm 3T Industries Sdn Bhd are helping pineapple plantations in Malaysia to increase their yields and save resources. For the first time, 3T Industries has applied BASF’s IrgaCycle UV033 DD to enhance 100% recycled high density polyethylene (HDPE) sheets used as protectors for pineapples.
While pineapples require a warm and humid climate, they are susceptible to damage from solar radiation and high temperatures (> 32°C) which can significantly reduce marketable yield and cut deep into a grower’s profit. Symptoms include sunburn or bleaching which are visible as yellow-white skin that turns pale grey or brown upon damage to the tissue underneath. This damaged tissue is susceptible to disease and infestation. The HDPE protector shields the fruit from direct sunlight while still allowing photosynthesis to occur.
Previously, 3T Industries used a combination of antioxidants and light stabilizers to achieve the performance requirements stipulated by the grower – the HDPE protectors needed to last through the intended service lifetime of four seasons.
IrgaCycle offers a one-pack solution that is immediately available for the recycler without the need for further premixing. It is also more efficient at lower concentrations compared to traditional antioxidant systems and reduces the overall quantity of additives required. This results in easy and accurate dosing, improved product quality, as well as upgraded recyclate for use in long-term applications, according to BASF.
“We use our expertise in recycling technology and post-consumer resins to provide better solutions to consumers and communities,” says PH Tan, Managing Director of 3T Industries. “With IrgaCycle, we were able to use recycled feedstock to design a new product that features a high amount of recyclate content and makes more sustainable agricultural plastics possible.”
BASF not only provided 3T Industries with the suitable additive solution, but also the technical recommendations to stabilise the recycled polymers during processing and outdoor weathering. This is important as an effective and sustainable application of recycled materials depends on, amongst others, the optimization of process conditions and modifying agents.
Launched in 2021, IrgaCycle consists of a series of plastic additive formulations, which enable recycled plastics to be reused for the production of high-value plastics in combination with virgin materials. The additive solution addresses specific quality issues associated with recycled resins, such as limited processability, poor long-term thermal stability and insufficient protection from outdoor weathering.
The IrgaCycle range is offered as part of the Valeras portfolio.
(IMA)Subscribe to Get the Latest Updates from IMA Please click here
©2022 Injection Moulding Asia. All rights reserved.