Batteries: Iveco selects BASF as recycling partner for EV batteries; Lanxess/IBU-tec to develop iron oxides for LFP battery material
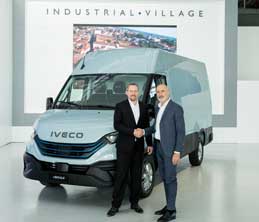
Automotive firm Iveco Group has announces the selection of German chemical firm BASF as its first partner to provide a recycling solution for the lithium-ion batteries of the group’s electric vehicles.
This decision is part of Iveco’s circular economy strategy to increase the lifetime of the batteries while decreasing their overall environmental impact, and Iveco says it will ensure compliance with the Extended Producer Responsibility policy which holds producers responsible for the entire life cycle of the products they introduce on the market, from their design until end-of-life.
BASF, which has recently inaugurated Europe’s first co-located centre of battery material production and battery recycling in Schwarzheide, Germany, will organise and manage the entire recycling process for the lithium-ion batteries used on Iveco’s electric vans, buses and trucks. The agreement includes the collection, packaging, transport, and recycling of batteries, in various European countries including, among others, France, Germany and UK.
After collection, BASF will mechanically process the batteries to black mass, from which critical raw materials – such as nickel, cobalt, lithium – can be extracted and recovered for use in the manufacturing of new batteries. Thus, BASF will establish the full battery recycling value chain in Europe to locally provide recycled metals with a low carbon footprint for the battery industry.
“The partnership with Iveco Group is our first agreement to recycle batteries from electric vans, buses and trucks and an important step for our battery recycling business to expand our activities into the commercial vehicle space,” said Dr. Daniel Schönfelder, President of BASF’s Catalysts division, who is also responsible for the company’s battery materials and battery recycling business. “
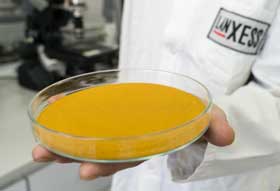
In other news, specialty chemicals company Lanxess and battery materials manufacturer IBU-tec have entered into a research cooperation in the battery sector. The goal of the two German companies is to develop innovative iron oxides for the production of cathode material for LFP batteries and thus increase the performance of this battery type. The companies aim to optimise the electrochemical properties of LFP batteries, such as energy density, charging speed and number of charging cycles.
More and more car manufacturers are increasingly relying on LFP (lithium/iron/phosphate) batteries for their e-vehicles - especially for volume models. Compared to NMC (nickel/manganese/cobalt oxide) and NCA (nickel/cobalt/aluminum oxide) cell chemistry systems, LFP technology offers cost advantages of up to 50% and promises safer use, as the system makes the batteries virtually impossible to ignite.
The demand for LFP in Europe is expected to grow by 20% per year until 2030. So far, however, this demand has been met almost exclusively by non-European suppliers. With their development, both companies aim to contribute to the establishment of an independent, robust value chain in the European LFP battery market, while at the same time reducing the carbon footprint of batteries.
IBU-tec, based in Weimar, Germany, is currently the only European manufacturer of LFP cathode material.
Meanwhile, Lanxess operates the world’s largest plant for the key raw material iron oxide in Krefeld-Uerdingen. The company has almost 100 years of experience in developing this material and can supply iron oxide particles for LFP batteries in the required size, purity, morphology and quantities.
In addition to key ingredients for LFP precursors, Lanxess offers many other solutions for electromobility and the battery industry, including raw materials for electrolytes, battery coolants, flame retardants for plastic components in electric vehicles and charging infrastructure, and orange dyes for colouring high-voltage components.
(IMA)Subscribe to Get the Latest Updates from IMA Please click here
©2024 Injection Moulding Asia. All rights reserved.