Green tie-ups: Covestro/Lanxess to produce sustainable raw materials with reduced CO2 footprint; Sumika/Hexagon enable 60% plastic carbon reduction for new vehicles
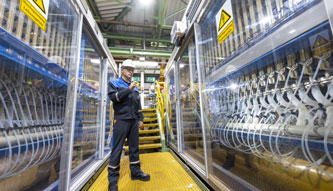
German chemical companies Covestro and Lanxess are cooperating in the energy-intensive production of basic chemicals at their Lower Rhine sites in Germany and make them more climate friendly. Lanxess procures chlorine, caustic soda and hydrogen from the ISCC PLUS-certified sites of Covestro in Leverkusen and Krefeld-Uerdingen. With immediate effect, Covestro is manufacturing around one-third of the volume of products it supplies to Lanxess using energy from hydropower based on guarantees of origin.
“Covestro is pursuing the goal of completely converting its production to electricity from renewable sources on its path to operational climate neutrality in 2035,” says Dr. Klaus Schäfer, Chief Technology Officer of Covestro. “A particular focus is on the energy-intensive production of basic raw materials. In cooperation with Lanxess, we use energy in our electrolysis plants in North Rhine-Westphalia on a pro-rata basis, which enables us to reduce our reported emissions by up to 120,000 metric tons of CO₂ per year.”
“The joint project with Covestro is an important building block in making our entire value chain climate-neutral. By sourcing raw materials for these products with a significantly reduced carbon footprint, we will be able to reduce our reported indirect emissions by up to 120,000 tonnes/year of CO₂ equivalents,” says Dr. Hubert Fink, member of the Lanxess Board of Management.
With its Net Zero Value Chain Initiative, the specialty chemicals group plans to eliminate Scope 3 emissions within its upstream and downstream supply chain by 2050. This includes indirect emissions, particularly from purchased raw materials, but also in logistics or disposal. For Scope 1 and 2 emissions, the company aims to be climate neutral as early as 2040. “With this program, we are taking the next step towards a climate-neutral product portfolio and also supporting our customers, who are increasingly looking for sustainable solutions,” says Fink.
Chlorine, caustic soda and hydrogen are basic building blocks for many products in the chemical industry. However, their production is very energy-intensive.
Lanxess uses the raw materials supplied by Covestro, for example, for products that are then used in the food and agricultural industries. Covestro produces the three basic raw materials at its North Rhine-Westphalian sites in Leverkusen, Krefeld-Uerdingen and Dormagen. Both the former have already been certified to the internationally recognised ISCC PLUS standard for the production of the strategic raw material chlorine, while this is also planned for Dormagen in the near future.
The correct allocation of the electricity to the products is ensured via this certification and the use of the renewable energy is proven by the invalidation of certificates of origin at the Federal Environment Agency.
Covestro is also actively involved in various projects to build a hydrogen economy that uses mainly or exclusively green hydrogen as an energy carrier. Among other things, the company is supporting, in cooperation with Hydrogenious LOHC Technologies, to build the world’s largest plant for storing renewable hydrogen in liquid organic carriers in Dormagen, Germany.
With regard to its energy supply, Covestro focuses on power purchase agreements (PPAs) for renewable energy or high-level certificates. Only recently, the company signed PPAs with Chinese supplier CGN New Energy on wind and solar power that will cover around 30% of the electricity needs of its important production site in Shanghai. Under another, utility Ørsted will supply offshore wind energy starting in 2025, which is expected to meet 10% of the electricity needs of Covestro’s sites in Germany.
Engie, Belgium’s largest renewable energy producer, will provide onshore wind energy to meet 45% of the electricity demand of Covestro’s Antwerp production site in Belgium.
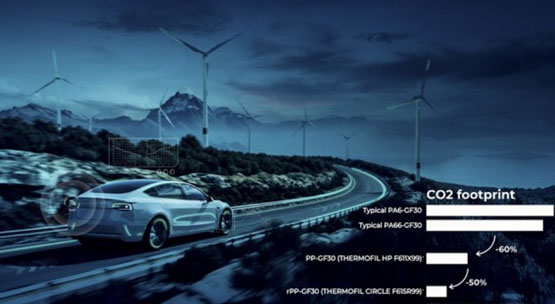
In other news, Hexagon’s Manufacturing Intelligence division and thermoplastic compounds maker Sumika Polymer Compounds Europe (SPC Europe), are partnering to digitise the performance of new sustainable automotive-grade polypropylene (PP) compounds, enabling engineers to design components that are more recyclable and offer a lower carbon footprint for future vehicles.
Sumika Polymer Compounds’ short glass-fibre polypropylene (GF-PP) Thermofil HP and recycled polypropylene (GF-rPP) Thermofil Circle materials benefit from sustainable manufacturing and recycling processes and offer carmakers performance equivalent to incumbent engineering plastics, but with an up to 60% lower carbon footprint. A growing proportion of today’s PP components are recovered and recycled compared to polyamides (PA), of which up to 70% are utilised in waste-to-energy initiatives or finish up in landfill, but there remains substantial room for improvement. These new Sumika recycled PP compounds are designed for the circular economy, contributing to plastic waste reduction at vehicle end-of-life, says the firm.
Plastics can contribute up to 20% of the total weight of a car, and their application is escalating with the continuing replacement of metals. The automotive industry’s shift to eMobility has increased the need for lightweighting components to maximise the energy efficiency of vehicles and mitigate the considerable weight of battery packs, but their environmental performance throughout the lifecycle must also be considered by product development teams.
“Limited material behaviour data is a barrier to sustainable eMobility innovations because automotive engineering teams have not been able to put new materials through the rigorous virtual durability and safety tests required for automotive endorsement,” said Guillaume Boisot, head of the Materials Centre of Excellence at Hexagon. “Our unique multiscale material modelling technology accelerates the adoption of SPC Europe’s ground-breaking recycled materials by making it possible for product development teams to accurately simulate a component and subject it to established automotive engineering test and validation.”
This vital engineering data is the result of a long-term partnership between the two companies, providing product development teams the ability to evaluate the suitability of GF-PP compounds in new designs to address carbon-neutral targets by replacing traditional engineering plastics.
“Our Thermofil short glass-fibre reinforced polypropylene compounds offer equivalent performance to traditional engineering plastics while providing a much lower carbon footprint, which makes them highly suitable to meet design challenges that sustainable eMobility brings,” said Bruno Pendélio, marketing manager for SPC Europe. “Combining our efforts with Hexagon allows us to support the race towards carbon neutrality by further lightweighting our customers’ automotive components, reducing physical material testing and prototyping.”
Hexagon conducted a detailed and rigorous testing and physical validation programme with SPC Europe to produce highly accurate multi-scale behavioural models of its Thermofil HP grades and Thermofil Circle portfolio of recycled PP grades. Each material grade has a model that simulates the materials’ mechanical and environmental performance throughout a component’s lifecycle. The encrypted proprietary material models can be accessed by SPC Europe customers through Hexagon’s Digimat software. Digimat is interoperable with popular computer-aided engineering (CAE) software tools, such as MSC Nastran, Marc, and third-party software, empowering engineers to perform accurate analyses using established digital engineering workflows.
(IMA)Subscribe to Get the Latest Updates from IMA Please click here
©2023 Injection Moulding Asia. All rights reserved.