Collaborative project for thinwall containers using recycled materials
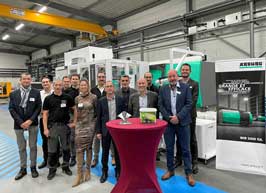
How do you economically produce thin-walled containers using top-quality recycled material and with maximum output? By having several specialists combine their expertise. This is what has happened in France as part of the Thin Wall Integra collaborative project. The collaboration pursues several objectives simultaneously, namely the high-volume processing of recycled material into thinwall containers in a way that is fully automated, fast, and of a consistently high quality.
Arburg’s subsidiary in France has teamed up with Collomb, a mould maker specialising in thinwall containers, Pagès Group, a robotics expert for packaging, Verstraete, an IML label manufacturer, Koch-Technik, a material flow specialist, and Borealis, a raw materials supplier, to present Thin Wall Integra as a new one-stop shop concept for the production of thinwall 5 l buckets.
The jointly developed concept is based on a fully automated injection moulding cell around a hybrid Allrounder 720 H in packaging version with a 1-cavity mould. The complete cycle only takes around five seconds. In addition to the injection moulding machine optimised for fast cycles, the sequentially operating robotic system is also a top performer. The handling system with telescopic arm that engages from the rear side of the machine first loads the mould with the IML labels. The robotic system then removes the labelled buckets and stacks them on a deposit mat. The stacks are then automatically picked up by a robot for palletising. The two robot technologies used make the system particularly compact. The recyclate is continuously fed in via an automatic conveyor system.
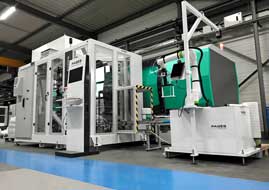
Arburg adds that the Thin Wall Integra partners contributeD their specific expertise at every stage of the project to demonstrate the technology to manufacturers of thinwall containers, while also ensuring the necessary quality and meeting the tight deadlines of the packaging industry.
In addition, the joint project is in line with the ecological aspects of plastics processing that are so important today. The product has a proportion of 55% recycled material, and its ‘ecological design’ enables material savings of up to 35%. Added to this are the simplified stackability of the buckets and the use of ‘HolyGrail 2.0’ labels, which make it easy to recycle the materials used by type.
The fully automated project system is specifically designed for high-performance packaging applications that require speed, precision and efficiency, as well as ease of maintenance, adds Arburg.
(IMA)Subscribe to Get the Latest Updates from IMA Please click here
©2022 Injection Moulding Asia. All rights reserved.