Husky’s latest UltraShot injection system
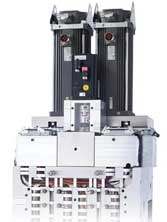
Canadian machinery maker Husky Injection Molding Systems has launched the UltraShot Injection System, a next generation melt delivery and control system that is said to eliminate the deficiencies of traditional injection moulding.
“With the UltraShot Injection System, we are re-engineering the injection moulding process. We are breaking down the barriers of traditional injection moulding processes in order to achieve higher levels of capability, control and overall part design freedom. The UltraShot Injection System is a game changer and provides better control than anything else in the industry. This approach is especially important now with massive, increased demand and speed-to-market, especially in the medical market, for example, where production risks and scalability are critical,” said John Galt, President/CEO, Husky.
The UltraShot’s advanced injection control technology enables risk-free scalability with part capability. Identical system behaviour for each injection circuit provides process condition consistency with cavitation scaling. It allows up to 128 cavities, thus enabling producers to maximise cavities without negative performance on balance or shot-to-shot variation. Brand owners can accelerate from prototype to high cavity production qualification, increasing speed-to-market.
The new injection system also enables brand owners to produce highly functional and validated parts, economically, where conventional injection moulding processes cannot. This cavity filling control and process optimisation overcomes traditional constraints of pressure, L/T and difficult-to-mould resins. This enables part lightweighting for resin and process time savings and provides resin selection flexibility. Ultimately, this means greater part design freedom, opening up endless possibilities for brand owners looking to take plastic part designs to the next level, adds Husky.
Compared to conventional hot runners, melt in the UltraShot experiences fewer high-pressure injection cycles, thus preserving the original resin properties. This leads to lower mould-in stress and better mechanical and optical properties in the moulded part. With this technology, the best physical properties are obtained for a moulded part.
Powered by the Altanium Mold Controller, the UltraShot provides highly advanced process monitoring and control for injection moulding. The Altanium process control provides repeatability and traceability for part dimension consistency, perfect balance and a more stable process. Providing digital analysis creates a measurable discipline around the moulding process, and gives customers full control and trend analysis of various processes resulting in improved, lower risk operations.
The melt delivery system is the “heart” of the injection moulding process and is essential to mould cell performance. The UltraShot masters part filling in a way that provides part design freedom, while reducing risk and improving part quality and speed of mould qualification. With “Husky Inside”, producers ensure that the centre of their system performs optimally, every shot. It offers increased productivity, at a reduced footprint, resulting in lowest total part production cost.
It is the perfect fit for medical, technical packaging and consumer electronic part producers looking to scale up, implement more efficient process control, address competitive marketplaces, and reduce risk, scrap, waste and cost.
Subscribe to Get the Latest Updates from IMA Please click here
©2021 Injection Moulding Asia. All rights reserved.