3D Printing: Ineos reports energy savings with styrenics; Synthomer/University of Loughborough collaborate on 3D concrete printing
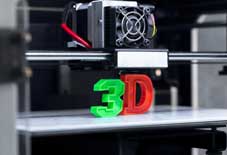
Styrenics maker Ineos Styrolution has released the first results of the PolySLS project, which is focused on developing a new energy saving styrenics based material for additive manufacturing, or 3D printing. Ineos adds that the new polymer compound has been developed for R&D purpose only. Potential future commercial availability will depend on various factors including results of further tests, demand and production capacity.
The project has been able to show that significant overall energy savings of up to 67% have been achieved when taking the entire life cycle of a new styrenics polymer compound into account compared to using traditional Polyamide 12 (PA12.
A direct energy saving of 25% was achieved from the 3D printing equipment when using the new styrenics polymer, resulting from lower process temperatures and shorter heating and cooling phases. This also improved the time needed to complete printing jobs, with processing times 7.5% shorter than with PA12.
The PolySLS project was funded by the German Ministry for Economic Affairs and Energy (BMWi). The purpose of the PolySLS project was to develop and test a new styrene based polymer compound for Selective Laser Sintering (SLS). A particular focus of the project was on researching energy and material requirements.
The project was started in August 2017 and carried out in collaboration with the Süddeutsche Kunststoffzentrum (SKZ-KFE gGmbH) and the Friedrich-Alexander-University Erlangen-Nuremberg. The project ended in November 2020.
Bianca Wilhelmus, Global Application Development Manager at Ineos Styrolution and Project Lead for PolySLS: “Styrenics based materials continue to amaze me. Even 90 years after the first production of polystyrene, there are still new things to explore. Styrenics based materials have incredible, beneficial properties.”
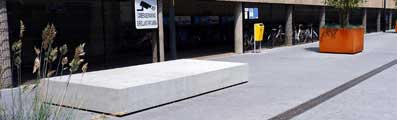
In other related news, UK-headquartered polymers firm Synthomer Plc, has linked up with the University of Loughborough in a project aimed at developing the next generation of concrete manufacturing technology. The project is led by construction experts at the UK university and supported by a grant of £1.2 million from the EPSRC’s Industrial Strategy Challenge Fund (ISCF). The project team also includes Autodesk; Concrenetics; Cundall; Foster + Partners; University of Sheffield; and Urbastyle.
3D Concrete Printing (3DCP) is a digitally-driven, off-site manufacturing technology that is establishing itself worldwide as a viable manufacturing process. However, its use beyond purely aesthetic objects is currently limited by the manufacturing accuracy achievable. The work undertaken by this group will develop the next generation, Hybrid Concrete Printing (HCP), technology that uses 3DCP to create a near-net-shape (an object slightly larger than the desired object) and then uses a subtractive process (cutting, milling and drilling) to remove a small amount of material to create the net-shape - the desired object to sub-millimetre precision. HCP technology offers an alternative to traditional cast concrete, freed from the need to construct moulds and traditional constraints on form and finish.
The project team has mapped out the global impact of the project thorough a supply chain initiative they refer to as MADE: Materials, Automation, Design and End user.
Materials: New polymer products developed and marketed by Synthomer for use as components of the concrete admixture used to modify the performance and properties of the printed concrete. Such components could, for example, control the rate at which the concrete flows and the rate it dries at, building on Synthomer’s portfolio of construction materials.
Automation: The digital work flow used during printing and subsequent subtractive HCP operations will inform future developments of the Autodesk Powermill software capability. This builds on Autodesk’s success with the hybrid welding process used to create the world’s first 3D printed ship’s propeller WAAMpeller. The HCP project will also open up new opportunities for concrete design, freed from traditional constraints on form and function.
Design: The design methods will be embedded in software developed within Cundall and Foster + Partners, to enable them to design for manufacture using 3DCP and HCP. This capability places both organisations ready to deliver HCP as a solution for clients.
End user: Concrete street furniture designer and manufacturer Urba-Style, together with HCP tool and concrete manufacturer Concrenetics, provide an established route to market for the technology.
The project is led by Professor Richard Buswell of the Loughborough School of Architecture, Building and Civil Engineering. Richard has over 30 years’ experience in building systems engineering in both industry and academia, and has been working in the field of additive manufacturing in the construction sector for more than 15 years.
An industry focused case study report will be written, making the case for the commercial viability of HCP. This will be disseminated through dedicated industry workshops and dissemination partners, e.g. the BRE, to promote the technology, attract investment, engage potential customers and other organisations interested in becoming part of the technology supply chain.
Towards the end of the project, the companies will take a stand at the 2021 UK Concrete Show (+180 exhibitors) to showcase the project outcomes to the wider UK and international concrete industrialists and public through the stand and technical lectures.
Subscribe to Get the Latest Updates from IMA Please click here
©2021 Injection Moulding Asia. All rights reserved.